Closed-Loop Control System
Last Updated :
27 Feb, 2024
In this article, we’re going to discuss about closed loop control system. A closed-loop control system is an electronic device that automatically regulates a system to maintain a desired state or set point without human interaction. The advantages of closed-loop control systems lie in their ability to provide precision, stability, and resilience, making them indispensable in numerous technological advancements and industrial processes. The term “closed-loop” reflects the feedback loop that is established, where the output is fed back to the system’s input for constant monitoring and correction.
Control System
A Control System manages commands, directs, or regulates the behavior of other devices or systems using control loops. It is a control system where its control action depends on both its input signal and output response.
There are basically two types of control systems:
Closed-Loop Control System
A closed-loop control system is a system in which the control action is somehow dependent on the output. The primary objective of a closed-loop control system is to enhance the system’s stability, accuracy, and overall performance. A simple example of a closed -loop control system is a home thermostat. The thermostat can send a signal to the heater to turn it on or off. It uses a temperature sensor to detect the current air temperature.
This system is used to maintain a setpoint without human interaction so it does it on its own. This system is also called the feedback controller because it has a feedback loop that performs the action to control a process variable same as the setpoint, i.e. the feedback where some section of the output signal fed back to the input section to reduce errors and maintain the stability in the system.
Examples: Automatic electric iron, missile launcher, speed control DC motor, etc.
Traffic lights control system is an example of control system. Here, a sequence of input signal is applied to this control system and the output is one of the three lights that will be on for some duration of time. During this time, the other two lights will be off. Based on the traffic study at a particular junction, the on and off times of the lights can be determined. Accordingly, the input signal controls the output. So, the traffic lights control system operates on time basis.
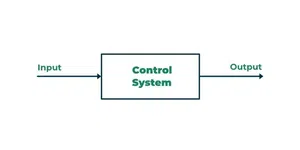
Block-diagram-of-CONTROL-SYSTEM
The error detector produces an error signal, which is the difference between the input and the feedback signal. This feedback signal is obtained from the block (feedback elements) by considering the output of the overall system as an input to this block. Instead of the direct input, the error signal is applied as an input to a controller. So, the controller produces an actuating signal which controls the plant. In this combination, the output of the control system is adjusted automatically till we get the desired response. Hence, the closed loop control systems are also called the automatic control systems. Traffic lights control system having sensor at the input is an example of a closed loop control system.
Closed-Loop Control System is used in applications where feedback and error handling are required. It is a complex system and not economical but optimization is possible. Maintenance of CLCS is difficult.
Operation of Closed Loop Control System
Here we see that the input is fed first and then accept by the controller after the error detection ,before that the input is changed from one form to the another as it performs the role of the reference input with respect to the system. As the controller produces the control signal , action takes place which leads to some specific output. After that the output is measured to check whether it is the desired one or not , for this a section of output signal is fed back to the input which is called as the feedback signal.
This feedback signal gets compared with the input and error signal is generated which is provided to the controller to produce the manipulated signals which proceeds to remove the error and produce the desired output.
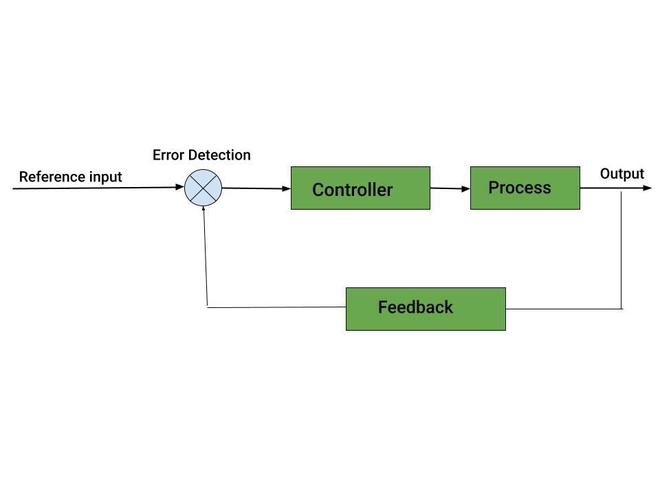
Components of Closed Loop Control System
- Reference input : Reference point is also known as setpoint. Input signal provided by the signal. This is the target output that the system is designed to follow.
- Error Detector : It compares the signal obtained from feedback and the reference input. The error detector is a crucial component in a closed-loop control system. Its primary function is to measure the difference between the desired or reference input (setpoint) and the actual output of the system, generating an error signal.
- Controller: It is the element which produces the desired output from the actuating signal. The controller is a crucial component that calculates the corrective action needed to minimize the error and bring the system output closer to the setpoint.
- Process: The plant or process represents the system being controlled. It could be a physical system like a motor, chemical process, or any other dynamic system. It is the device to be controlled.
- Controlled output: It is the quantity which required to be controlled out the desired level. The controlled output is the parameter or variable that the control system aims to control and regulate.
- Feedback : It is the part of the output signal which fed to the error detector for comparison with reference input. This information is then compared to the reference input to determine the error, which is the difference between the desired and actual outputs.
Types of Feedback
There are two types of feedback:
- Positive Feedback
- Negative Feedback
Positive Feedback
The positive feedback adds the reference input, R(s)R(s) and feedback output. The following figure shows the block diagram of positive feedback control system. The output and input signal are in phase with each other , reference inputs are added with this system in the feedback section which increases the gain of whole system.
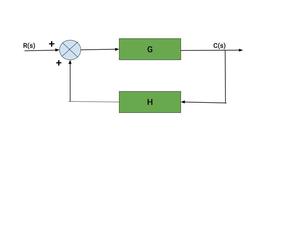
For the time being, consider the transfer function of positive feedback control system is,
T=G/1-GH
Where,
- T s the transfer function or overall gain of positive feedback control system.
- G is the open loop gain, which is function of frequency.
- H is the gain of feedback path, which is function of frequency.
Negative Feedback
Negative feedback reduces the error between the reference input, R(s)R(s) and system output. The input and output signal are out of phase with each other , so to get the error signal – the feedback signal and the input signal get subtracted , so the gain gets reduce of the overall system.
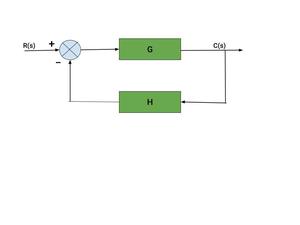
Transfer function of negative feedback control system is,
T=G/1+GH
Where,
- T is the transfer function or overall gain of negative feedback control system.
- G is the open loop gain, which is function of frequency.
- H is the gain of feedback path, which is function of frequency.
Applications of Closed Loop-Control System
- It is widely used in industrial applications, including agriculture, nuclear power plants, etc.
- AC doesn’t stay ON continuously, it will switch from ON to OFF and OFF to ON to maintain defined Temp, that helps to save power by closed loop system.
- Automatic electric iron can be controlled automatically by the heating element’s temperature in the iron.
- In the water level controller, the level of water can be decided by the input water.
Advantages and Disadvantages of Closed Loop-Control System
There are some list of Advantages and Disadvantages of Closed Loop-Control System given below :
Advantages of Closed Loop-Control System
- More accurate operation than that of open-loop control system.
- It can operate efficiently when input or system parameters are variable in nature.
- Less nonlinearity effect of these system on output response.
- High bandwidth of operation.
- There is facility of automation.
- Time to time recalibration of the parameters are not required.
Disadvantages of Closed Loop-Control System
- Complex design and difficult to conduct.
- Expensive than that of open-loop control system.
- Complicate for maintenance.
- Less stable operation than that of open-loop control system.
- Feedback may make system unstable.
Conclusion
Closed-loop systems have many advantages over open-loop systems. The type of control system which uses feedback signals to both control and adjust itself is called a Close-loop System. Closed-Loop Control System are considered as fully automatic control system because it is designed in a way that the achieved output is automatically compared with the reference input to have the required output. Closed-loop systems are designed to automatically achieve and maintain the desired output condition by comparing it with the actual condition.
FAQs on Closed-Loop Control System
What is the purpose of a controller in a closed-loop system?
It is the element which produces the desired output from the actuating signal. The controller is a crucial component that calculates the corrective action needed to minimize the error and bring the system output closer to the setpoint.
Can you give an example of a closed-loop control system in real life?
Traffic lights control system having sensor at the input is an example of a closed loop control system.
What are the main components of a Closed Loop Control System?
The main components of Closed loop Control system are reference input, controller, process, error detector, feedback.
How does a closed-loop control system different from an open-loop control system?
In open loop control system has no feedback path, while a closed loop control system has feedback path.
What are the advantages of closed loop control system?
Closed loop control system more accurate , reliable and high bandwidth and it can operate efficiently when input or system parameters are variable in nature.
Share your thoughts in the comments
Please Login to comment...