What is Flash Welding ?
Last Updated :
27 Feb, 2024
Flash welding, sometimes referred to as flash butt welding, is a type of welding in which two pieces of metal are joined by first melting their ends together and then hammering them together. Its benefits include high joint strength, little stretching, and the absence of consumables, which are frequently needed in traditional welding techniques. In this article, we’ll learn about flash welding, its features, parts, working, applications, advantages, disadvantages, and the difference between flash welding and butt welding with frequently asked questions. Hence we will say that is it a type of resistance welding that is done without the help of the filler metals.
Flash Welding
Flash welding is a welding technique that is quick and effective and used in numerous industries when joining two metals together. The strong bond is created by carefully heating and fusing the ends of two metal parts. The heat causes the end of the metal pieces to melt and produce a pool of molten metal and extra material, which is known as “flash,” is forced out of the joint. The other name for the same is flash butt welding. In this, the workpieces are subjected to electrical current before being brought together, which causes an arc to form.
Key Features of Flash Welding
- Process: The process involves the usage of the ends of the workpieces to melt to form the joint instead of melting the entire workpiece.
- Mechanical Pressure: Workpieces are subjected to mechanical pressure so that a strong bond is formed, which causes extra material to be expelled and a clean joint to form.
- Flash Formation: High temperatures are produced as an electric current passes over the contact area, melting the metal and the extra substance is discharged as a molten flash.
- Flash removal: After the connection has been produced, the extra material of the flash is usually removed mechanically, such as by shearing or cutting, leaving a neat and strong bond in its place.
Parts of Flash Welding
- Flash Gap: It is the distance that must be kept between the parts of work. It is crucial to produce an ideal weld.
- Electrodes: Copper or other conductive materials are used to make flash welding electrodes, which contact with the workpieces, to form an electrical circuit and to produce the heat required for welding.
- Clamping Mechanism: Workpieces are held in place with controlled force by the clamping mechanism during the process.
- Power Source: To deliver a strong electrical current during flash welding, a power source is necessary.
- Control system: The control system manages the flash welding procedure, ensuring that the electrical, pressure and timing conditions are just right to produce a strong weld. Thus, making sure the procedure is carried out accurately and consistently.
- Cooling system: The process of flash welding produces a significant amount of heat. To avoid overheating and guarantee the welded joint decreases down effectively without producing material deformation, a cooling system is commonly used.
Working of Flash Welding
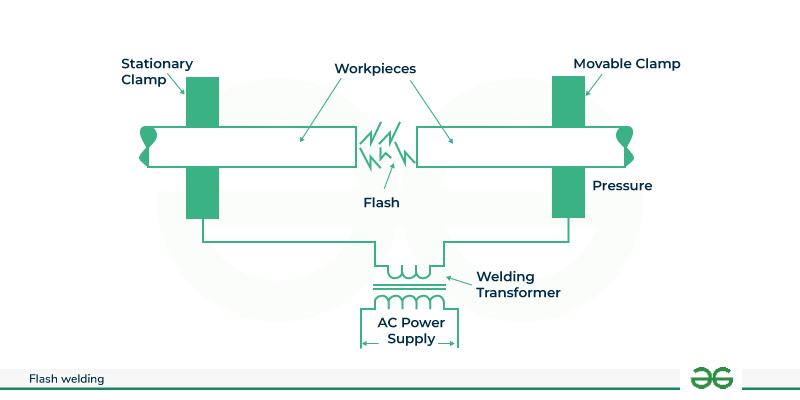
Flash-welding
The two workpieces that need to be welded are tightly secured in a flash welding equipment during this procedure.
When the two workpieces are brought together, the contacting surfaces heat up due to the flash that is produced and the resistance to the current flow and so the joints are heated above their melting point so that formation of flash takes place. The workpieces are quickly brought together under intense mechanical pressure, forcing the fused metal and slag out of the joint and creating a good, solid weld, as soon as they reach their melting temperature. The current supply is then switched off. A flashing effect is produced when the ends of the workpieces collide because the squeezed molten metal flashes out in an outward direction. This technique of welding is known as flash welding because of this flashing effect which takes place because of the heating of the metals.
Applications of Flash Welding
- Aerospace Industry: The aerospace industry uses flash welding to assemble vital pieces such aircraft structures, turbine engine parts and landing gear. The method creates the excellent, accurate welds required for aeronautical applications.
- Railway business: To make strong and dependable welds for railway tracks, flash welding is used in the rail business. Rail junctions that have been welded increase train travel’s safety and comfort while requiring less maintenance.
- Manufacturing of wires and cables: Electrical wiring, fencing eventually and telecommunications are just a few of the applications for which wires and cables are joined using flash welding. It establishes safe connections that keep electrical conductivity intact..
- Military and defense: The ammunition, armored vehicle constructions and tank components industries all use flash welding. The process guarantees the creation of dependable and durable military hardware.
- Metal Manufacturing: Flash welding is used in metal fabrication to unite different metal parts, such as tubes, pipes and rods. It is especially useful for creating robust, leak-resistant and long-lasting welds in oil and gas industry pipelines.
Advantages of Flash Welding
- Speed: Flash welding is a high-speed method that works well in situations involving mass production. The actual welding process often takes only a few seconds.
- Consistency: Flash welding ensures a high degree of accuracy and quality in the welded joints by producing results that are repeatable and consistent.
- No Consumables: Materials like flux or filler metal are not needed for flash welding. When compared to other welding procedures that require consumables, this can save money.
- Appropriate for a Variety of Materials: Flash welding is adaptable and works well for joining a variety of materials, such as various metals and alloys.
Disadvantages of Flash Welding
- Skilled Operator Required: Although flash welding is an automated process, it still needs trained operators to set up and keep an eye on the machinery. The cost of operations may increase due to the requirement for trained labor.
- Restricted to Specific forms: Flash welding works best when combining metal components of specific sizes and forms. Large workpieces or complex shapes could make it less useful.
- Energy Consumption: Since strong electrical currents are needed to produce the extreme heat required for welding, flash welding may be energy-intensive.
- Restricted Joint Types: The method works well for linear configured butt joints. For other joint types or applications which require for complex welding arrangements, it might not be as suitable.
Difference Between Flash Welding and Butt Welding
Parameters
|
Flash Welding
|
Butt Welding
|
Flash Formation
|
When additional molten material is released during the welding process, it produces a visible flash.
|
Visible Flash is not produced.
|
Complexity
|
It is complex than butt welding.
|
It is the much simpler process than flash welding and is used for quick and automated applications.
|
Joint Strength
|
Due to the high temperatures and forming action during the welding process, it creates an extremely strong joint.
|
It can result in strong joints, but the strength will vary based on the particular materials used, the parameters of the procedure and the post-welding treatment.
|
Suitable Materials
|
It is used for metals irrespective of their nature i.e, ferrous and non-ferrous metals.
|
This welding process is used for metals, plastics, and composites.
|
Conclusion
Flash welding is an important technique of welding that do wonders in a different industrial applications. It is a preferred welding technique for a variety of applications, including automotive, aerospace, construction and metal manufacturing, despite the fact that it does have some drawbacks. It continues to be an essential technique for guaranteeing the structural integrity, effectiveness and quality of the goods we depend on every day, even as industries change and demand innovation.
FAQs on Flash Welding
Which sectors utilize flash welding most frequently?
Heavy metal component joining is done by flash welding, which is utilized in the rail, pipeline, wire and cable and structural engineering industries.
In flash welding, how is the flash eliminated?
To obtain a clean and consistent welded joint, any extra material produced during the welding process is usually removed using techniques like shearing, grinding or machining.
Which materials are suitable for flash welding?
Metals that are ferrous or non-ferrous can be joined through flash welding. Its versatility for a range of applications is further enhanced by its suitability for connecting incompatible metals.
Is the technique of flash welding a high-speed process?
Yes, flash welding has a reputation for having a quick welding cycle, which makes it effective in situations when speed is essential.
Is the process of flash welding automated?
Automated flash welding is possible, although significant setup and supervision may be necessary to guarantee that the welding parameters are properly adjusted.
Share your thoughts in the comments
Please Login to comment...