Mechanical properties are defined as how materials react to loads or external forces. It is very important to understand the mechanical properties of engineering materials for creating components and structures that are reliable, efficient, and safe. They are essential in establishing a material’s suitability for particular applications across a range of technical disciplines. Basically, a material’s response to loads or external forces is described by its mechanical properties. They comprise traits such as flexibility, power, toughness, the degree of hardness, and more.
Mechanical Properties of Engineering Materials
- Yield Strength
- Tensile Strength
- Brittleness
- Poisson’s Ratio
- Hardness
- Thermal Expansion
- Wear Resistance
- Stiffness
- Ductility
- Malleability
- Toughness
- Resilience
- Creep
- Fatigue
1. Yield Strength
The maximum stress a material can withstand without permanently deforming is known as yield strength.
It has various phenomena:
- Upper Yield Point: Certain substances have an upper yield point, which is indicated by a sharp decline in the stress-strain curve after a peak. In some applications, this phenomenon, which is more typical of materials like steel with a low carbon content, can cause instability.
- Lower Yield Point: Various materials have a lower yield point, which is indicated by a sharp reduction in stress just as plastic deformation begins. For example, certain alloys.
- Yield Strength without Yield Point: Many plastics, for example, lack an apparent yield point. They show a progressive change from elastic to plastic deformation instead.
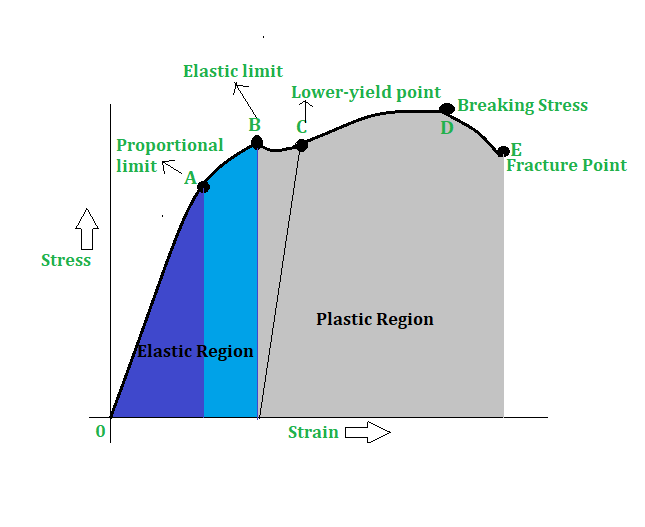
2. Tensile Strength
The maximum stress a material can withstand before breaking under strain is known as tensile strength. It is a key metric used in the fields of materials science and engineering in order to assess a material’s capacity for carrying loads and forecast how it will react under tensile loading.
3. Brittleness
The opposite of ductility is brittleness. Materials that are brittle only slightly bend plastically before breaking. When a material is in the elastic range, it reacts to stress by being stretched, but once the tension is gone, it returns to its former size and shape. Hooke’s Law, which asserts the stress is directly proportional to strain within a material’s elastic limit, governs this property.
4. Poisson’s Ratio
Poisson’s ratio gauges a material’s lateral contraction after axial deformation. It is the difference between axial and lateral strain. There are three types of Poisson’s Ratio:
- Positive Poisson’s Ratio (0<v<0.5): Whenever an axial load is applied to the majority of common materials, the material responds by compressing laterally. This indicates that although the lateral strain is negative, it is smaller in absolute terms than the axial strain, leading to a positive Poisson’s Ratio.
- Negative Poisson’s Ratio (−1<ν<0): In a few designed materials, such as some foams and composites, the side strain is positive when axial tension is applied. The result is a negative Poisson’s Ratio.
- Zero Poisson’s Ratio (ν=0): When an axial load is given to a perfect incompressible material, there is no lateral strain. This means under axial loading, the material’s lateral dimensions do not change.
5. Hardness
Hardness is a material’s resistance to piercing, scratching, or erosion. A tougher substance is less susceptible to deformation because it has stronger atomic bonds. The depth or size of an indentation made by a typical indenter under a specific load is frequently used to measure the property.
Types of Hardness Tests
- Brinell Hardness Test: Under a specific load, the surface of the material is pressed into by a steel ball, generally 10 mm in diameter. The resulting indentation’s diameter is determined, and the hardness rating is computed. Softer materials or ones with tough grain structures are good choices for this test.
- Knoop Hardness Test: Due to the tiny size of the indentation, the Knoop Hardness Test is often applied to thin and weak materials.
- Shore Hardness Test: This test, which generally applies to elastomers and polymers, determines the amount of depth of penetration of a certain indenter with a specific geometry and spring force.
6. Thermal Expansion
A material’s dimensions changing as a result of temperature changes is known as thermal expansion. With variations in temperature, various materials expand or contract to differing degrees.
Types of Thermal Expansion
- Linear Thermal Expansion: A material’s change in length due to a shift in temperature is referred to as linear thermal expansion.
- Area Expansion: This notion applies when working with two-dimensional items like sheets or surfaces.
- Volume Expansion: This process is important in three-dimensional items like solids and liquids.
- Anisotropic Thermal Expansion: It is the ability of different materials to display distinct thermal expansion behavior in various directions.
7. Wear Resistance
The material’s capacity to withstand degradation and wear when in touch with other surfaces is known as wear resistance.
Types of Wear Resistance
- Abrasive Wear: It occurs when sharp particles collide with the surface of a substance, causing material to be removed through scratching, grinding, or cutting.
- Adhesive Wear: It is the process by which material is transferred from one surface to another as a result of adhesive forces.
- Erosive Wear: It is commonly seen in applications involving high-velocity liquids or particles and is brought on by the impact of solids, droplets of liquid, or gases on a material’s surface.
- Fretting Wear: Surface damage results from repeated micro-sliding and impacting between two surfaces in localized contacts that are subjected to minor relative motion.
- Corrosive Wear: In environments where materials have been exposed to both mechanical and chemical degradation, corrosive wear combines the effects of both wear and corrosion.
8. Stiffness
A material’s stiffness is determined by its capacity to withstand deformation when stressed. The elasticity modulus serves as a proxy for stiffness. A material has a high degree of stiffness or rigidity if it only deforms slightly when subjected to load. The aluminium beams are less rigid or stiff than steel beams.
9. Ductility
A material’s ductility is its capacity to pull out into a thin wire when subjected to a tensile strain. Plastic and strength are both required for ductile material. Gold, mild steel, copper, aluminium, nickel, zinc, and tin are examples of ductile materials. Ductility is often expressed in terms of percentage elongation and percentage area decrease. Tensile properties are assumed to include ductility. Plasticity and tensile strength are combined in ductile material.
10. Malleability
Material’s malleability refers to its capacity to endure heat or cold working while being rolled, flattened, or hammered into thin sheets. Plastic should be used for malleable materials, although strength is not required. Malleability is regarded as a compressive quality. Examples of malleable metals are soft steel, wrought iron, Al, Cu, Sn, and Pb.
11. Toughness
It refers to a material’s capacity to sustain bending without breaking under heavy impact loads. When a substance is heated, its toughness reduces. The area under the stress-strain curve, which is another way to measure it, shows how much energy a unit volume of the material has absorbed after being stressed all the way to failure. For instance, mild steel will absorb far more energy before failing if a load is rapidly applied to it before being applied to a piece of glass. Mild steel is therefore thought to be far more durable than glass.
12. Resilience
Resilience is the ability of a material to absorb energy while enduring shock and impact loads. The quantity of energy absorbed per unit volume within the elastic limit is typically used to describe it. Maximum energy which can be stored in a body up to elastic limit is called the proof resilience and the Proof resilience per unit volume is called modulus of resilience.
13. Creep
A part is going to experience creep, which is a slow and irreversible deformation, if it is exposed to a steady tension at a high temperature over a protracted length of time. When designing IC engines, boilers, and turbines, property is taken into account. Viscous flow is the most basic type of creep deformation. The image below illustrates the three phases of a standard creep curve. The initial creep begins quickly and then slows down. However, the rate of the secondary creep is quite constant. Tertiary Creep, which began in the third stage but was speeded up, ends when the material ruptures or fractures. It is related to both grain boundary void generation and necking.
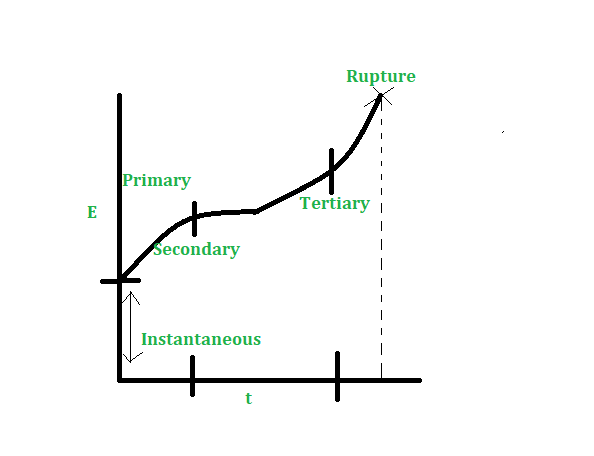
Classic Creep Curve
14. Fatigue
A fracture occurs under a stress whose maximum value is less than the material’s tensile strength when a part is subjected to repetitive or variable loads. These include, for instance, the parts of high-speed aircraft and turbine engines. A material’s ability to endure continuously changing and alternating loads is known as this attribute. A part won’t break if loaded once to a stress close to the yield stress. It will eventually malfunction if loaded to this level repeatedly. This failure is known as fatigue. It is a key goal in the designing of moving machinery.
Testing Methods for Mechanical Properties of Engineering Materials
There are various methods used to study and characterize the mechanical properties of engineering materials. Some of the tests that are used to study the mechanical properties are-
1. Tensile Testing
A steel sample is put through the tensile test. The test device measures the load and the sample’s corresponding dilatation when the load is applied. The stress-strain curve is then made using this data.
Procedure of Tensile Testing
- Sample Creation: The substance turns into a standardized test specimen with a particular geometry (cylindrical or rectangular).
- Installation: Clamps are used to securely mount the specimen in the testing device.
- Loading: The specimen gets subjected to an axial load by the machine, which causes it to elongate. Continuous records of the load and the related elongation are maintained.
- Stress strain curve: Plotting a stress-strain curve using the resultant data will demonstrate how the material responds to increasing loads. This curve aids in identifying important mechanical features.
Important Parameter of Tensile Testing
- Yield Strength: The stress at which a material begins to deform plastically rather than elastically.
- Ultimate Tensile Strength (UTS): The material’s greatest stress that it can endure before breaking.
Applications of Tensile Testing
In a variety of sectors, including automotive, aerospace, construction, and manufacturing, tensile testing is used to characterize a material’s mechanical behavior, choose the best materials for certain applications, and ensure the structural integrity of components.
2. Fatigue Testing
A titanium aerospace part is put through testing for fatigue. The component is put through cyclic loading to mimic the stress it would go through when operating.
Procedures of Fatigue Testing
- Sample Preparation: From the material, samples with defined geometries are created, frequently in the shape of dog bones.
- Load Application: The sample is continuously loaded with change compression and tension, resulting in cyclic stress.
- Stress-Cycle Recording: Throughout the test, the amount of stress and the amount of cycles are recorded.
- Fatigue Life Analysis: The test goes on out until the sample fails, or until a particular amount of cycles have been completed. The material’s fatigue lifespan is calculated based on the number of cycles before failure.
Important Parameters of Fatigue Testing
- Fatigue Life: The number of cycles a material can endure before failing .
- S-N Curve: It is often used to describe fatigue behavior and plots the stress amplitude (S) against the number of cycles to failure (N).
3. Impact Testing
A Charpy impact test is performed on a polymer sample. A swinging pendulum strikes the sample, and the energy absorbed during fracture is measured.
Procedure of Impact Testing
- Sample Preparation: From the material, specimens with standardized geometry are created, frequently in the shape of notched or unnotched bars.
- Pendulum Impact Testing Device: The specimen has been fastened at the tip and struck by a pendulum that is swinging with a predetermined amount of force.
- Fracture Behavior: The specimen fractures as a result of receiving the impact energy. It is calculated how much energy was necessary to break the specimen.
Important Parameters Impact Testing
- Impact Energy: The quantity of energy that the specimen can withstand before it breaks.
- Impact Toughness: The capacity of a substance to withstand impacts without breaking.
Applications of Impact Testing
Impact testing is essential for determining a material’s capacity to bear abrupt loads, ensuring the security of goods, buildings, and machinery used in the manufacturing, aerospace, automotive, and construction sectors.
Key Factors Affecting Mechanical Properties
The factors that follow can have an impact on an engineering material’s mechanical properties:
1. Composition: A material’s mechanical properties are impacted by its chemical composition. The strength, ductility, and other traits of a material can be affected by its presence of defects or alloying elements.
2. Crystal structure: A material’s mechanical characteristics are influenced by the position of atoms in its lattice of crystals. Strength, ductility, and toughness can vary depending on the crystal structure.
3. Microstructure: The arrangement of a material’s atoms and grains inside its crystal structure is commonly referred to as its microstructure. The mechanical properties of a material can be impacted by the size, shape, and orientation of the grains.
4. Loading circumstances: A material’s mechanical characteristics can be impacted by the way it is loaded, especially in tension, compression, flexing, or twisting. The type, length, and pace of the loading can all affect the material’s properties.
5. Processing: A material’s mechanical characteristics may change according to the method of processing used. The qualities of the material can also be altered by the rate of cooling down thermal treatment, and other production factors.
6. Temperature: Different temperatures have a substantial impact on how a material’s mechanical characteristics vary. Materials may become weaker and more susceptible to distortion and failure at high temperatures.
Importance of Mechanical Properties in Material Selection
The right material selection could make the difference between a product or structure being successful or unsuccessful since different uses and circumstances demand for different mechanical qualities. Here are some important factors in choosing a material is impacted by various mechanical properties:
- Strength: The capacity of a material to endure outside forces without breaking or deformation is commonly referred to as it’s strength. When there are large loads or stresses involved, high-strength materials are preferred.
- Ductility: The capacity of a material to bend under pressure without breaking is known as ductility. High ductility materials are advised for applications where deformation without failure is necessary.
- Energy Efficiency: Materials with suitable mechanical qualities may help in lowering energy consumption in situations where energy conservation is important.
- Optimal Design: Choosing materials with the appropriate mechanical properties allows optimal design. While minimizing weight and cost, engineers may achieve desirable levels of rigidity, strength, and other performance characteristics.
- Cost-effectiveness: Selecting materials that are both economical and provide the required mechanical properties helps project budgets be managed without affecting performance.
- Hardness: A material’s capacity to endure scratching or indentation. High hardness materials have been chosen for applications requiring resistance to friction.
- Toughness: The capacity of a substance to resist absorbing energy without breaking is known as toughness. High toughness materials are chosen for applications requiring resistance to shock or impact loads.
Advantages of Mechanical Properties of Engineering Materials
- Understanding mechanical characteristics is important for assuring the security and dependability of buildings and goods. It will help in perfect designing of the infrastructure.
- Mechanical testing is used by producers to check the quality of their resources and goods. They can find any discrepancies and remedy them by comparing test results to the given mechanical qualities.
- Mechanical characteristics can be used to forecast a material’s long-term performance and durability. For applications where materials are subjected to cyclic stress, temperature fluctuations, or harsh conditions, this is essential.
Disadvantages of Mechanical Properties of Engineering Materials
- Temperature Dependence: Many mechanical qualities vary with temperature. Materials can have various characteristics at high and low temperatures. This can make the design process more difficult, especially for applications that are subjected to high-temperature changes.
- Anisotropy: Some materials, such as composites and some metals, can show anisotropic behavior, which means their mechanical characteristics change depending on the direction. Anisotropic materials need more extensive analysis and design procedures.
- Material Ageing: Materials’ mechanical characteristics can vary over time owing to variables such as environmental exposure, fatigue, and wear. Engineers must take these changes into account when designing for long-term endurance.
Applications of Mechanical Properties of Engineering Materials
- Aerospace Industry: Materials with particular mechanical qualities are utilised in aerospace engineering to produce robust yet lightweight components for aeroplanes and spacecraft. Extreme temperature fluctuations, severe stresses, and fatigue must be tolerated by materials.
- Automobile Industry: For numerous components, the automobile industry relies on materials with a range of mechanical qualities. For example, materials with strong heat conductivity are utilised for engine components, whereas high-strength steels are employed for car frames and crash safety.
- Medical Devices: Materials with precise mechanical qualities, corrosion resistance, and biocompatibility are required for medical implants and devices. For orthopaedic implants, for example, materials with excellent fatigue resistance are essential.
FAQs : Mechanical Properties of Engineering Materials
1. What is a stress-strain curve?
A stress-strain curve depicts how a material deforms in response to applied stress (force). It demonstrates how strain and tension are related to loading and unloading.
2. What is yield strength?
The greatest stress that a material can endure without permanently deforming is known as yield strength. It represents the transition from elastic to plastic deformation in a material.
3. How are mechanical qualities taken into account while choosing materials?
According to the precise mechanical characteristics needed for a certain application, engineers select materials. They take into account things like the load, the environment, and the intended performance.
Share your thoughts in the comments
Please Login to comment...