In our everyday lives, we go over different circumstances where we need to quantify physical quantities like mechanical pressure applied on metal, temperature levels, Tension levels, and so on… For this multitude of utilizations, we really want a device that could gauge these obscure amounts in units and alignments natural to us. One such device which is generally helpful to us is the transducer. The transducer is an electrical gadget that can change over an actual amount as a corresponding electrical amount either as voltage or electrical current. From the huge pool of different types of transducers, this article means to make sense of piezoelectric transducers. They are used for the conversion of electrical charge into energy with the help of some solid material.
What is Piezoelectric Transducer?
The meaning of a Piezoelectric transducer is an electrical transducer which can change over any type of physical quantity into an electrical signal, which can be utilized for measurement. An electrical transducer which involves properties of piezoelectric materials for transformation of actual amounts into electrical signals is known as a piezoelectric transducer. It uses piezoelectric effect for the measurement of the changes in any quantity by conversion of the energy to electric charge.
-300.png)
Piezoelectric Transducer
Piezoelectric materials show the property of piezoelectricity, as per which on the application of a mechanical pressure or strain prompts the generations of an electric voltage relative to the applied pressure. This produced electric voltage can be measured using voltage measuring instruments to compute the value of stress or strain applied to the material.
What is Transducer?
A transducer is a device or instrument that changes one type of energy into another. With regards to electrical designing and physical science, a transducer is much of the time used to change over an actual amount, like power, strain, temperature, or light, into an electrical sign or the other way around. The objective is to work with the measurement, observation, or control of the physical quantity. Basically, it is used to convert the energy from one form to another, for example – a microphone, that converts one form of energy to another form i.e. sound waves ( as input energy ) converted to impulse ( as output energy ).
Piezoelectric Effect
The piezoelectric effect is a peculiarity wherein certain materials produce an electric charge in light of mechanical pressure or twisting. On the other hand, these materials can likewise go through a mechanical deformity when exposed to an electric field. This bidirectional connection between mechanical pressure and electric charge is normal for piezoelectric materials.
Piezoelectric materials are many times translucent in nature and display a non-centrosymmetric gem structure. The most widely recognized normal piezoelectric material is quartz, yet there are additionally different engineered materials with piezoelectric properties, for example, lead zirconate titanate (PZT) and polyvinylidene fluoride (PVDF).
The piezoelectric effect can be grasped in two principal modes:
- Direct Piezoelectric Impact: At the point when mechanical pressure is applied to a piezoelectric material, it causes a removal of charge inside the material, prompting the age of an electric voltage across the material. This impact is taken advantage of in different applications like piezoelectric sensors and actuators.
- Opposite Piezoelectric Impact: For this situation, when an electric field is applied across a piezoelectric material, it goes through an adjustment of shape or mechanical deformation. This is normally used in piezoelectric transducers and actuators.
How to Measure Piezoelectric Transducer Efficiency ?
Measuring the productivity of a piezoelectric transducer includes evaluating its capacity to change over mechanical energy into electrical energy or the other way around. The proficiency is normally communicated as the proportion of valuable result energy to the information energy. The estimation cycle can shift contingent upon whether you are zeroing in on the piezoelectric transducer as a sensor or an actuator. Here are common rules for estimating the proficiency:
For Piezoelectric Sensors
- Calibration: Prior to proficiency estimation, adjust the piezoelectric sensor to guarantee exact and steady readings. Apply known mechanical improvements and record the relating electrical reactions.
- Input Mechanical Energy: Apply a controlled mechanical boost to the piezoelectric sensor. This could be as power, tension, or speed increase, contingent upon the sensor type and application.
- Measure Electrical Output: Record the electrical result produced by the sensor because of the mechanical upgrade. This could be as voltage or charge.
- Calculate Efficiency: Ascertain the efficiency by contrasting the electrical output with the information mechanical energy. The productivity (η) can be expressed as:
Efficiency (%)=(Useful Output Energy / Input Energy)×100
Efficiency (%)=( Input Energy / useful Output Energy)×100
For Piezoelectric Actuators
- Mechanical Input: Apply an electrical contribution to the piezoelectric actuator. This could be a voltage or charge input, contingent upon the actuator type.
- Measure Mechanical Output: Record the mechanical result created by the actuator in light of the electrical information. This could be as dislodging or force.
- Calculate Efficiency: Work out the effectiveness by contrasting the mechanical result with the electrical info. The productivity (η) can be communicated as:
Efficiency (%)=(Useful Mechanical Output Energy/Electrical Input Energy)×100
Efficiency (%)=( Electrical Input Energy / Useful Mechanical Output Energy )×100
- Consider Losses: Consider any losses in the system, like electrical losses, hysteresis, or mechanical losses. These losses can affect the overall efficiency of the system.
Types of Piezoelectric Materials
- Normally Available Ones are the Quartz, Rochelle salt, Topaz, Tourmaline-bunch minerals. Falsely makes piezoelectric materials are Polyvinylidene difluoride, PVDF or PVF2, Barium titanate, Lead titanate, Lead zirconate titanate (PZT), Potassium niobate, Lithium niobate, Lithium tantalate, and other without lead piezoelectric ceramics.
- Unfortunately ,there is no piezoelectric material which has this large number of properties. Quartz is an exceptionally steady precious stone which is normally accessible yet it has little result levels. Rochelle salt also gives the most noteworthy result esteems however it is delicate to natural circumstances and can’t be worked above 1150F.
- All piezoelectric materials can not be utilized in the piezoelectric transducers- some conditions needs to be follow for this i.e. material should have the high output value , accessible in different types of shapes and adapt the shape without adapting their properties.
Working of Piezoelectric Transducer
Piezoelectric Transducer works with the guideline of piezoelectricity. The essences of piezoelectric material, normal quartz, is covered with a thin layer of conducting material like silver. At the point when stress has applied the particles in the material move towards one of the leading surface while getting away from the other. This outcomes in the age of charge. This charge is utilized for adjustment of stress. The extremity of the delivered charge relies on the heading of the applied pressure. Stress can be applied in two structures as Compressive pressure and Ductile pressure as shown in figure.
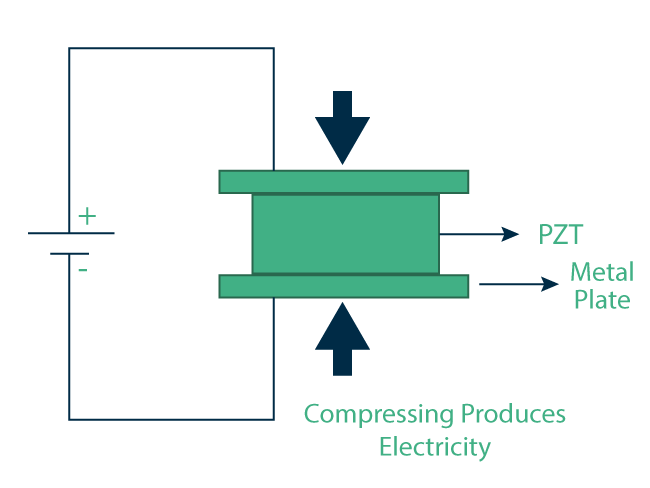
Working-of-Piezoelectric-Transducer
The direction of the crystal likewise effects the amount of voltage generated. Crystal in a transducer can be set up in longitudinal position or cross over position.
-660.png)
Piezoelectric Transducer Formula
Longitudinal and Transverse Effect
In the longitudinal effect, the Charge generated is given by
Q = F * d
Where F is the applied force, D is the piezoelectric coefficient of the crystal.
Piezoelectric coefficient d of quartz gem is around 2.3 * 10-12 C/N.
In the cross over impact, the charge created is given by
Q = F * d * (b/a)
At the point when the proportion b/a is greater than 1 the charge delivered by cross over plan will be more prominent than the sum produced by longitudinal plan.
Piezoelectric Transducer Circuit
The working of a fundamental piezoelectric transducer can be explained by the below figure.
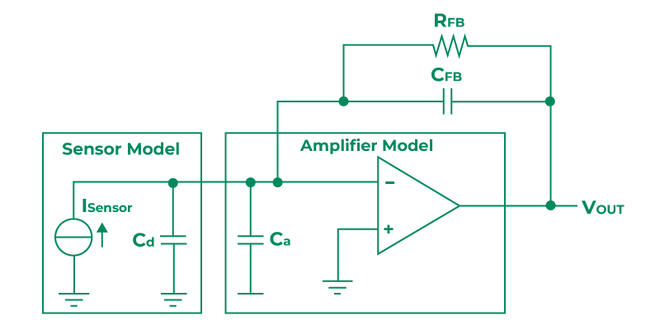
Piezoelectric-Transducer-Circuit
Here quartz crystal coated with silver is utilized as a sensor to generate a voltage when stress is applied on it. A charge enhancer is utilized to gauge the delivered charge without dissemination. To draw exceptionally low current the obstruction R1 is extremely high. The capacitance of the lead wire that associates the transducer and piezoelectric sensor additionally influences the alignment. So the charge intensifier is typically positioned extremely close to the sensor.
So in a piezoelectric transducer when mechanical pressure is applied a corresponding electric voltage is produced which is enhanced utilizing charge speaker and utilized for adjustment of applied pressure.
Piezoelectric Ultrasonic Transducer
The basic principle of its working is the converse piezoelectric effect. It produces the sound of that frequency which normally cannot be heard by the human. This sound is typically used in the vacuum cleaners. In this impact when power is applied to a piezoelectric material, it goes through actual disfigurements relative to applied charge. The circuit of the ultrasonic transducer is given below:
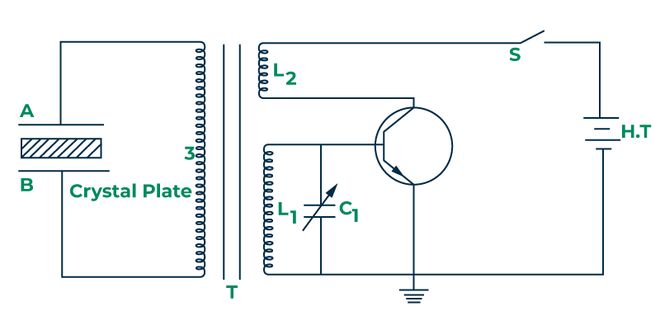
Piezoelectric Ultrasonic Transducer
Quartz crystal is set between the two metal plates A and B that are connected through L3 of the transformer. The essential of the transformer is inductively coupled to the electronic oscillator. The coils L1 and L2, which structures auxiliary of the transformer, are associated with the electronic oscillator.
At the point when the battery is turned ON the oscillator creates high-recurrence substituting voltage beats with a frequency f=1÷(2π√L1C1). Because of this, an e.m.f is prompted in L3 which is moved to the quartz precious stone through plates An and B. Because of banter piezoelectric impact the precious stone beginnings contracting and growing on the other hand accordingly making mechanical vibrations. Resonance happens when the frequency of the electronic oscillator is equivalent to the regular frequency of the quartz. Right now, quartz produces longitudinal ultrasonic waves of large amplitude.
Piezoelectric Actuator
A piezoelectric actuator is a transducer, used to change an electrical sign into a precisely controlled physical dislodging or stroke by utilizing piezoelectric effect in light of electromechanical coupling as opposed to electromagnetic induction. In the event that the stroke is stayed away from, useable energy will create. The specific development control managed the cost of by these actuators is basically used to change machining instruments, mirrors, focal points, or other contraption finely.
A piezo actuator is utilized to control water driven valves which work like a particular reason engine, little volume siphon and in different applications which utilizations power or development. The piezoelectric actuator diagram was shown in below. When contrasted with electromagnetic actuators, piezoelectric actuators have a few highlights like adaptable plan, reduced size and give sub-micrometer or nanometer positioning.
Advantages and Disadvantages of Piezoelectric Transducer
There are some list of Advantages and Disadvantages of Piezoelectric Transducer given below :
Advantages
- Low Power Utilization: In specific applications, piezoelectric transducers can offer low power utilization. This is invaluable for battery-fueled gadgets or circumstances where energy productivity is vital.
- Quick Reaction Time: Piezoelectric transducers have a fast reaction time, permitting them to respond rapidly to changes in the information signal. This trademark is favorable in applications that call for ongoing responsiveness, like in sensors for dynamic estimations.
- Strength and Long Life expectancy: Piezoelectric materials are known for their sturdiness and strength, prompting a more drawn out life expectancy contrasted with a few different sorts of transducers. This makes them appropriate for applications requiring dependability and life span.
- Lightweight and Compact: Piezoelectric materials are ordinarily conservative and lightweight, making them reasonable for applications where space and weight contemplations are basic. This is particularly significant in fields like clinical gadgets, aviation, and versatile hardware.
- Wide Operating Temperature Range: Piezoelectric transducers can work successfully over a wide temperature range. This flexibility makes them appropriate for applications in outrageous conditions, incorporating those with high or low temperatures.
- High Sensitivity: Piezoelectric materials display high aversion to changes in mechanical pressure or disfigurement. This property makes them amazing for detecting applications, where little changes in power, tension, or speed increase should be identified and changed over into electrical signs.
Disadvantages
- Brittleness: Piezoelectric materials can be weak, and mechanical pressure past their cutoff points can prompt crack or disappointment. This weakness can be a worry in applications with high mechanical powers or effects.
- Temperature Sensitivity: The piezoelectric impact can be affected by temperature changes. Outrageous temperatures might influence the exhibition of piezoelectric transducers, restricting their viability in specific conditions.
- Frequency Dependence: The presentation of piezoelectric transducers is in many cases recurrence subordinate. While they succeed in specific recurrence runs, their viability might decrease at very low or high frequencies.
- Cost: Great piezoelectric materials can be moderately costly. This cost element might be a thought, particularly in applications where cost-viability is an essential concern.
- Limited Power Output: While piezoelectric transducers are proficient in switching mechanical energy over completely to electrical energy, their power result might be restricted contrasted with some other energy transformation advancements. This can be an imperative in applications requiring higher power levels.
- Voltage Necessities: Creating adequate voltage can be a test in specific applications, particularly while managing low-sufficiency mechanical vibrations. This can require extra intensification hardware, affecting the general framework intricacy.
Applications of Piezoelectric Transducer
Some of the uses of Piezoelectric transducer in some domains are as follows:
- Sensors: Piezoelectric transducers are generally utilized in accelerometers to quantify speed increase in different gadgets, including cell phones, auto frameworks, and modern gear. Piezoelectric materials can be utilized in pressure sensors for applications like observing liquid strain in pipelines and clinical gadgets.
- Actuators: Piezoelectric actuators are utilized in accuracy situating frameworks in fields like microscopy and optics, where precise and fast development is required. Piezoelectric transducers are utilized in inkjet printers to create pressure waves that launch minuscule beads of ink onto paper.
- Medical Devices: Piezoelectric transducers are a critical part in clinical ultrasound devices, where they create and get ultrasonic waves for imaging inner designs in the body. Ultrasonic vibrations created by piezoelectric materials are utilized in careful devices for accuracy cutting and expulsion of tissues.
- Energy Harvesting: Piezoelectric transducers can change over encompassing mechanical vibrations, like those from strides or vehicle development, into electrical energy for driving little electronic gadgets or sensors.
- Sonar Systems: In submerged applications, piezoelectric transducers are utilized in sonar frameworks to produce and get acoustic waves for route, correspondence, and identification of submerged objects.
- Modern Applications: Piezoelectric transducers are utilized in NDT applications to create ultrasonic waves for reviewing materials and designs without causing harm. Piezoelectric sensors are utilized for observing vibrations in apparatus and designs, assisting with recognizing possible issues or glitches.
- Customer Electronics : These transducers are utilized in electronic gadgets, cautions, and clocks to create perceptible signs. A few touchscreens utilize piezoelectric innovation to give haptic criticism, causing a material situation when a touch is enrolled.
Properties of Piezo Electric-Crystal
Piezoelectric crystals display a few properties that make them significant in different mechanical applications. Here are a few vital properties of piezoelectric crystals:
- Piezoelectric effect: The most principal property of piezoelectric gems is their capacity to produce an electric charge because of mechanical pressure. Alternately, they can go through mechanical deformation when exposed to an electric field. This bidirectional relationship is known as the piezoelectric impact.
- Direct and Inverse Piezoelectric effects: The direct piezoelectric impact alludes to the age of electric charge in light of mechanical pressure, while the opposite piezoelectric impact is the mechanical distortion that happens because of an applied electric field.
- Anisotropy: Piezoelectric crystals frequently display anisotropic way of behaving, meaning their properties can fluctuate with course. The piezoelectric coefficients might contrast along various crystallographic tomahawks, impacting the precious stone’s exhibition in unambiguous applications.
- Crystalline Design: Piezoelectric crystals stones have a non-centrosymmetric glasslike structure, which is a vital prerequisite for the piezoelectric impact. Quartz, for instance, has a three-sided precious stone construction that adds to its piezoelectric properties.
- Resonance: Piezoelectric crystals stones can reverberate at explicit frequencies, making them valuable in applications like oscillators, channels, and sensors. The reverberation recurrence can be impacted by the gem’s aspects and cut.
- Dielectric Properties: Piezoelectric crystals display dielectric conduct, meaning they can store and delivery electrical energy. This property is used in capacitive parts and energy stockpiling applications.
- Frequency Response: The piezoelectric effect is many times more articulated at higher frequencies, and piezoelectric gems can be planned and slice to advance execution inside unambiguous frequency ranges.
Conclusion
In conclusion, piezoelectric transducers assume a significant part in a wide exhibit of uses across different industries. Their capacity to change over electrical energy into mechanical vibrations as well as the other way around, in light of the piezoelectric impact, makes them fundamental in different mechanical progressions. The benefits of piezoelectric transducers, including their wide recurrence range, high responsiveness, and conservative plan, add to their far and wide use in applications going from sensors and actuators to clinical gadgets and energy gathering.
In spite of their various benefits, it’s fundamental to recognize the hindrances of piezoelectric transducers, like restricted removal, temperature responsiveness, and reliance on material properties. Specialists and scientists keep on tending to these difficulties, attempting to improve the presentation and appropriateness of piezoelectric gadgets.
As innovation advances, piezoelectric transducers are probably going to track down new and creative applications, driven by continuous innovative work. Their flexibility, strength, and responsiveness make them significant parts in frameworks requiring accuracy, awareness, and versatility.
The different and extending scope of uses for piezoelectric transducers highlights their significance in propelling fields as shifted as medical services, aviation, modern observing, and energy collecting. Their remarkable capacities keep on adding to the improvement of state of the art advancements, making piezoelectric transducers a central participant in the scene of current designing and development.
FAQs on Piezoelectric Transducer
What is a piezoelectric transducer?
A piezoelectric transducer is a gadget that changes over electrical energy into mechanical vibrations (as well as the other way around) in light of the piezoelectric impact. This impact includes the age of an electric charge in light of mechanical pressure or distortion.
What is mean by piezoelectric effect?
The piezoelectric impact is the capacity of specific materials to produce an electric charge in light of mechanical pressure or deformity. On the other hand, when an electric field is applied, these materials go through mechanical distortion.
What materials are usually utilized in piezoelectric transducers?
Normal materials incorporate quartz gems, lead zirconate titanate (PZT), and certain earthenware production. These materials show the piezoelectric impact and are appropriate for different applications.
What are the principal uses of piezoelectric transducers?
Piezoelectric transducers are utilized in various applications, including sensors (accelerometers, pressure sensors), actuators (accuracy situating frameworks, inkjet printers), clinical gadgets (ultrasound imaging), energy reaping, from there, the sky is the limit.
Are piezoelectric transducers utilized in clinical imaging?
Indeed, piezoelectric transducers are generally utilized in clinical ultrasound imaging gadgets. They produce and get ultrasonic waves to make pictures of interior designs in the body.
How do piezoelectric transducers function in sensors?
In sensors, piezoelectric transducers convert mechanical varieties (e.g., pressure, force, speed increase) into electrical signs. At the point when stress is applied, the transducer creates an electric voltage relative to the mechanical pressure.
Share your thoughts in the comments
Please Login to comment...