Heat engines are devices that turn heat energy into motion or mechanical work. Heat engines are based on the principles of thermodynamics, specifically the conversion of heat into work according to the first and second laws of thermodynamics. They are found everywhere, from our cars, power plants to even old trains. Despite their wide use, they all share a common limitation that they can’t be 100% efficient.
In this article we will learn in detail about Heat Engines, its working, diagram, efficiency, applications and limitations.
What are Heat Engines?
Heat engines are thermodynamic machines that converts heat energy into mechanical work. It transfers heat from a high-temperature reservoir (hot body) to a lower temperature sink (cold body) and harnesses this thermal energy to perform work, such as moving a piston or rotating a turbine. During this process, the system inevitably loses some energy as waste heat due to the inherent inefficiency in converting heat to work.
Definition of Heat Engines
Heat engines are the devices that convert heat energy into mechanical energy, harnessing thermal energy from a high-temperature source and transferring it to a cooler sink to produce work, often as motion.
It is governed by second law of thermodynamics. They inherently cannot achieve complete efficiency, always losing some energy as waste heat.
Components of a Heat Engine
The parts of heat engine are categorized into two types
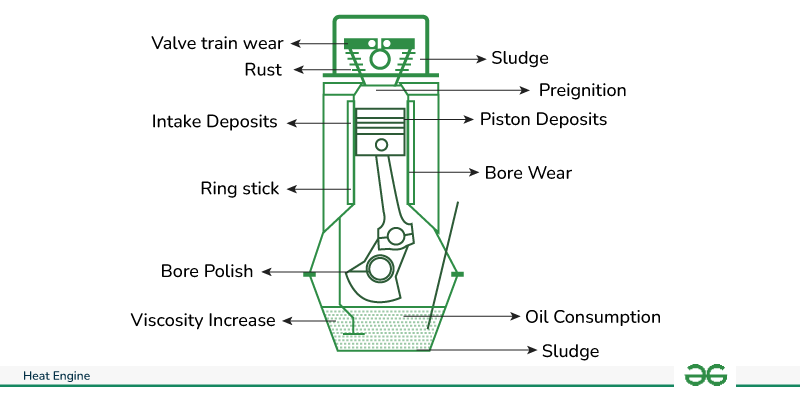
Static Part of Heat Engine
A heat engine’s fixed components are the cylinder head, block, and crankcase.
Cylinder Head
- It Forms the top closure of the cylinder and often contains part of the combustion chamber.
- It houses components such as the intake and exhaust valves, spark plugs (in gasoline engines), and fuel injectors (in direct injection engines).
Block
- It is core structure of the engine, holding the cylinders where the pistons move up and down.
- The engine block also contains passageways for oil and coolant to maintain lubrication and optimal temperature.
Crankcase
- The lower part of the engine block, enclosing the crankshaft.
- It serves as a reservoir for the engine’s oil and supports the lower ends of the cylinders.
Moving Part of Heat Engine
A heat engine’s moving parts include the connecting rod, piston, flywheel, and crankshaft.
Connecting Rod
- It Connects the piston to the crankshaft, transferring the force from the piston’s linear motion to the crankshaft’s rotational motion.
Piston
- A cylindrical component that moves up and down within the cylinder, compressing the fuel-air mixture (in gasoline engines) or air (in diesel engines) and transferring the energy from the combustion process to the connecting rod.
Flywheel
- Attached to the crankshaft, it stores rotational energy to smooth out the engine’s power output, especially during the intervals between power strokes in multi-cylinder engines.
Crankshaft
- Converts the reciprocating motion of the pistons into rotational motion that ultimately powers the vehicle’s drivetrain and accessories.
Some other parts are the bench, the cylinder, tray, oil tank, plunger pin, compression rings, spark plug, valve spring, camshaft, rocker, exhaust valve, suction valve and valve head .
Working Principle of Heat Engines
The core mechanism of a heat engine relies on transferring heat thermodynamically from a high-temperature source to a lower temperature sink, creating a flow of thermal energy that enables the engine to produce work. The laws of thermodynamics, especially the second law, intricately govern this process. This law dictates that converting heat into work requires a temperature differential and faces inherent efficiency limits.
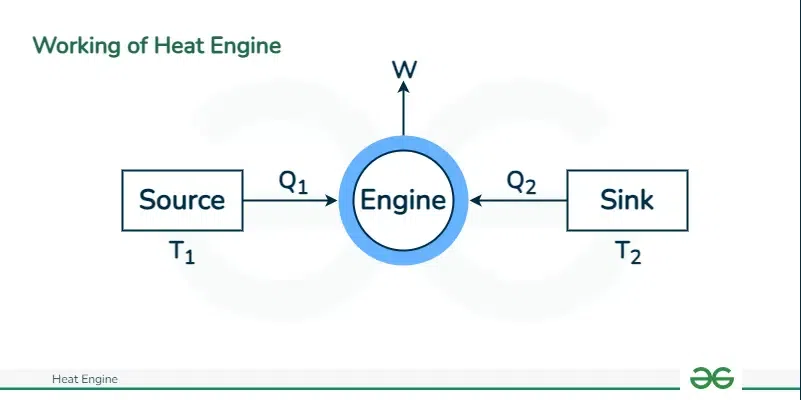
During a heat engine’s operation, introducing heat to the working material from a high-temperature source transforms a portion of this heat into mechanical work, while the engine expels the remaining heat to the cooler sink. This operation follows an important principle: the temperature of the heat sink must always be lower than that of the source.
Throughout their operational cycle, heat engines:
- Absorb heat from a high-temperature source
- Convert part of this heat into work
- Reject the remaining waste heat to a low-temperature sink.
For example, in a power plant scenario:
- A furnace acts as the energy source, transmitting heat (Qin) to the steam within the boiler.
- The steam’s flow through the turbine leads to the generation of work (Wout).
- The steam’s residual waste (Qout) heat is then transferred by a condenser to an energy sink, such as the atmosphere.
- Water cycles back to the boiler from the condenser via a pump, where work (Win) is required to pressurize the water back to boiler pressure.
The net work output of the power plant is calculated as the difference between the work produced and the work input, expressed as Wnet output = Wout-Win. This reveals the cycle’s energy balance to be Wnet output = Qin-Qout , highlighting the efficiency and operation of heat engines in converting thermal energy into usable mechanical work.
Mechanical Work Output
The mechanical work output of a heat engine is the practical result of the engine’s operation, where the converted thermal energy is transformed into mechanical energy. This transformation allows the engine to perform physical tasks, such as moving pistons, driving turbines, rotating wheels, or generating electricity. The work output is essentially the energy that is harnessed to do something useful, beyond merely transferring heat from one place to another.
The mechanical work output is quantified as the difference between the heat energy absorbed from the source (Qin) and the heat energy expelled to the sink (Qout). This net work output (Wnet) can be expressed as Wnet = Qin-Qout , highlighting the efficiency of the heat engine in converting heat into usable work.
Types of Heat Engines
Heat engines manifest in various forms, each utilizing distinct methods to achieve energy transformation:
Internal Combustion Engines(ICEs)
In internal combustion engines, the fuel combustion process occurs inside the engine itself. The combustion of fuel produces high-pressure gases, which directly act on mechanical components of the engine, such as pistons, to produce motion. Car engines and Gas Turbines are very good example of this type of combustion engine.
It is also called 4-stroke because it takes 4 strokes for the piston to complete one combustion cycle. Example of an ICE is Gas Turbine which is discussed below:
Gas Turbines
Gas turbines are internal combustion engines that compress air and mix it with fuel, which is then burned at high temperatures to produce hot, pressurized gas. This gas expands through a turbine, creating powerful rotational energy used to drive generators, airplanes, and ships. Known for their high power-to-weight ratio and efficiency.
Key Features of ICEs
- Fuel Efficiency: Often more fuel-efficient in specific applications compared to external combustion engines.
- Power-to-Weight Ratio: High power-to-weight ratio, making them suitable for vehicles and portable machinery.
- Variety of Fuels: Can run on various fuels, including gasoline, diesel, and natural gas.
- Applications: Widely used in automobiles, motorcycles, small power generators, and aircraft
External Combustion Engines (ECEs)
External combustion engines generate mechanical work from an external heat source. The combustion process takes place outside the engine, and the generated heat is transferred to a working fluid within the engine, causing it to expand and do work.
A very good example of an external combustion engine is a steam engine and Stirling Engines .
Steam Engines
Steam engines are external combustion engines where water is heated to create steam in a boiler. This high-pressure steam then drives a piston or turbine, converting thermal energy into mechanical work. Historically significant, steam engines powered the Industrial Revolution, enabling advancements in transportation and manufacturing.
Stirling Engines
Stirling engines operate on a closed-loop cycle that moves a fixed amount of gas between hot and cold heat exchangers. Unlike steam engines, they can function with minimal noise and are highly efficient, capable of using any external heat source. This versatility allows Stirling engines to be used in various applications, from small generators to solar power systems, showcasing their potential in renewable energy technologies.
Key Features of ECEs:
- Versatility in Heat Sources: Can use a wide range of heat sources, including coal, natural gas, nuclear, solar, and biomass.
- Environmental Adaptability: Potentially less polluting, as the fuel type and combustion process can be optimized to reduce emissions.
- Complexity and Size: Typically larger and more complex than ICEs, making them less suitable for mobile applications.
- Applications: Primarily found in power generation facilities, steam locomotives, and certain marine applications
Heat Energy PV Diagram
Pressure-Volume (PV) diagrams serve as fundamental tools in analyzing the operation of heat engines, especially those utilizing gas as the working medium. In such engines, the PV diagram forms a closed loop that graphically represents the engine cycle. The area enclosed by this loop quantifies the net work produced during one cycle of operation.
Understanding engine efficiency through PV diagrams involves comparing the depicted engine cycle with the Carnot cycle, known for its maximum theoretical efficiency among heat engines.
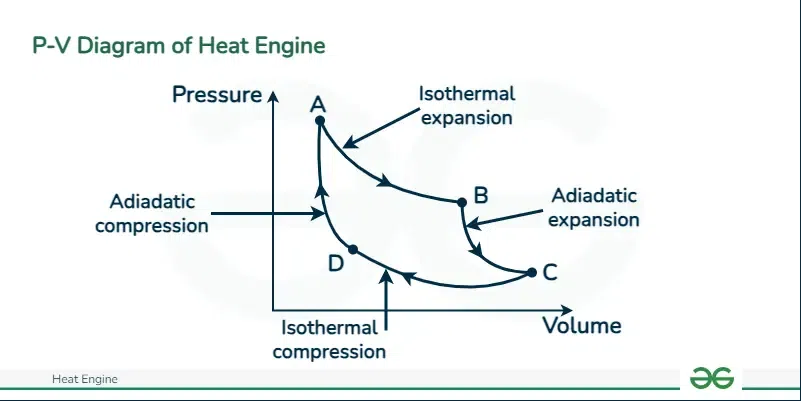
Interpretation of PV Diagrams
- Isothermal Expansion at High Temperature: If the heat source is hot enough, the working fluid transitions from liquid to vapor at a constant temperature. This phase change occurs at constant pressure while the volume increases, indicating vaporization.
- Adiabatic and Reversible Expansion: In the turbine section, the gas undergoes adiabatic (no heat exchange) and reversible expansion, reducing its temperature as it expands. This process follows the specific equation of state governing adiabatic and reversible changes.
- Isothermal Compression at Low Temperature: When exposed to a cooler source, the working fluid shifts from gas back to liquid isothermally. During this phase change, the process maintains constant pressure while the volume decreases, reflecting condensation.
- Adiabatic and Reversible Compression: At the compressor stage, the fluid is adiabatically and reversibly compressed, increasing its pressure back to the starting condition without changing its temperature.
This cyclic process depicted on a PV diagram highlights the sequential thermodynamic transformations the working fluid undergoes, effectively illustrating how heat engines convert thermal energy into mechanical work.
Efficiency of Heat Engines
Efficiency of a heat engine is defined as the ratio of work output to heat input, expressed as a percentage. This metric illustrates how effectively a heat engine converts the thermal energy it receives into mechanical work. According to the second law of thermodynamics, it’s impossible for any engine to achieve complete efficiency, indicating that some energy will always be lost in the conversion process.
Mathematically, efficiency (η) can be calculated as:
Given that the work done (W) is the difference between the heat input (Q1) and the heat rejected (Q2):
W=Q1-Q2
Substituting this into the equation for efficiency yields:
η = (Q1-Q2)/Q1 = 1- (Q2/Q1)
Hence, if Q2 =0, implying no heat is rejected, the efficiency would theoretically reach 100%. However, such a scenario is unattainable in practice due to inevitable energy losses within any real system. Consequently, every engine’s efficiency is inherently capped.
Carnot Efficiency
Carnot engine represents a theoretical model of a perfectly efficient engine that operates on a reversible, closed thermodynamic cycle. Within this cycle, the working fluid undergoes four distinct stages: isothermal expansion, adiabatic (or isentropic) expansion, isothermal compression, and adiabatic compression. This idealized cycle serves as a foundational concept for understanding other thermodynamic cycles widely applied across various industries, notably in Carnot heat engines and refrigeration systems.
While the Carnot engine sets the standard for maximal theoretical efficiency, no practical engine can fully attain this efficiency due to inevitable losses, primarily from friction. The efficiency of a Carnot engine is determined solely by the temperatures of the hot and cold reservoirs it operates between.
In essence, the Carnot engine operates by absorbing heat (Q1) from a high-temperature source, converting part of that heat into work (W) by exploiting the difference in heat content (W=Q1-Q2), and then discharging the remaining heat (Q2) to a low-temperature sink.
Mathematically, Carnot efficiency (η) can be calculated as:
η = 1 – (Q2/Q1)
which is the efficiency of the heat engine.
If Q2 = 0, then efficiency = 100% . Carnot engine is known for this.
Examples of Heat Engine
- Automobile Engines: The most common example of internal combustion engines, where gasoline or diesel is burned.
- Steam Turbines in Power Plants: Utilize steam produced from boiling water to rotate turbines connected to generators, producing electricity.
- Jet Engines: A type of gas turbine where air intake is compressed, mixed with fuel, and ignited.
- Locomotives: Steam locomotives were powered by external combustion steam engines, converting coal-fired steam into motion.
- Stirling Engines: Found in specialized applications where quiet operation or the ability to use heat from renewable sources is advantageous, such as in solar power generation or underwater drones.
- Refrigeration and Heat Pumps: Though technically the reverse of a heat engine, these systems use similar principles to move heat against its natural flow for cooling or heating purposes.
- Marine Engines: Ships often use large diesel engines (internal combustion) or steam turbines for propulsion, depending on the ship’s size and purpose.
Uses of Heat Engines
Heat engines are used in a wide range of applications due to their ability to convert thermal energy into mechanical work. Some common uses include:
- Power Generation: Converting thermal energy from combustion or nuclear reactions into electricity in power plants.
- Transportation: Powering vehicles such as cars, motorcycles, and airplanes with internal combustion engines.
- Industrial Applications: Driving factory machinery and industrial processes, often with steam engines or gas turbines.
- Aerospace: Propelling aircraft with jet engines and gas turbines through rapid exhaust gas expulsion.
- Renewable Energy Systems: Employing Stirling engines in solar and geothermal energy applications to generate electricity.
- Residential Heating and Cooling: Utilizing heat engines in heat pumps for efficient building temperature regulation.
Sample Questions on Heat Engines
Question 1: Given a heat engine with a heat input (Qin) of 500 J and a heat rejection (Qout) of 300 J, calculate its efficiency.
Answer:
The efficiency of the heat engine, given the heat input (Qin) of 500 J and heat rejection (Qout) of 300 J, is 40%.
Question 2: Why is it impossible to achieve 100% efficiency in a real heat engine, and what factors contribute to energy loss?
Answer:
Achieving 100% efficiency in a real heat engine is impossible due to the second law of thermodynamics, which dictates that some energy must always be lost as waste heat to the environment during the conversion process. Factors contributing to energy loss include friction, heat dissipation, and the inherent inefficiency of transferring heat between different temperatures. These irreversible processes ensure that not all input heat can be converted into useful work, limiting the engine’s efficiency.
Question 3: Discuss the role of gas turbines in renewable energy systems. How do they contribute to energy sustainability?
Answer:
Gas turbines play a pivotal role in renewable energy systems by providing flexible, efficient backup power for intermittent renewable sources like solar and wind. They can quickly ramp up to full power, compensating for variability in renewable energy production and ensuring a stable energy supply. Gas turbines also have the potential to run on sustainable fuels, such as hydrogen or biofuels, further contributing to energy sustainability by reducing reliance on fossil fuels and lowering carbon emissions. Their adaptability and efficiency make them crucial in the transition towards more sustainable and resilient energy systems.
Question 4: Explain how the second law of thermodynamics limits the efficiency of a heat engine.
Answer:
The second law of thermodynamics limits the efficiency of heat engines by necessitating that some input heat is always expelled as waste to the sink, preventing the complete conversion of heat into work and underscoring the inherent inefficiencies in energy transformation processes.
Frequently Asked Questions (FAQs) about Heat Engines
What is a heat engine?
A heat engine is a device that converts heat energy to mechanical energy
Why can’t heat engines be 100% efficient?
Due to the second law of thermodynamics, some energy in a heat engine must always be lost as waste heat, preventing 100% efficiency.
What are the factors on which the efficiency of Carnot’s engine depends?
The efficiency of Carnot’s engine depends on the absolute temperature of the source and sink.
Can heat engines only use fossil fuels as a heat source?
No, heat engines can utilize a variety of heat sources, including renewable energy sources like solar thermal energy and biofuels, in addition to fossil fuels.
Heat energy is converted into what form of energy in a heat engine?
Heat energy gets converted into mechanical energy in a heat engine.
What are few examples of heat engines?
Petrol Engine, Steam Engine, Diesel Engine , etc. are few examples of heat engines
Share your thoughts in the comments
Please Login to comment...