The acronym PWM denotes Pulse Width Modulation. By altering the width of an electrical signal’s pulses, a technique used in electrical and electronic engineering can regulate the amount of power supplied to a system or device. This is frequently utilized in applications including dimming LEDs, managing the electricity supplied to heaters and other appliances, and managing the speed of motors.
Different widths of square-wave pulses are produced using PWM. The magnitude of the input signal usually correlates with the pulse width, alternatively referred to as pulse width offset. PWM is used to power LEDs or regulate motors. PWM is mostly used because it makes it possible to regulate the average power supplied to an output or load. They are also employed in communications for modulation and voltage regulation.
What is PWM?
PWM stands for Pulse Width Modulation. It’s a method used to control the analogue circuits using digital signals. In PWM, the duration of the pulse (known as the pulse width) is modulated to encode a specific analogue signal level. With pulse width modulation (PWM), the duty cycle of the pulse signal is changed to alter the average power delivered to the load. The ratio of the pulse width (on time) to the signal’s overall period is known as the duty cycle. You can effectively manage the amount of power given to the load by varying the duty cycle.
The PWM period, which is the reciprocal of the pulse frequency, the pulse width offset, and the pulse delay time are often among the various tuning parameters of a PWM system. The difference in time from the pulse beginning at 0 s is represented by the pulse delay time. The values may be expressed in seconds or as a % of the PWM duration. The proportion of the PWM time T is represented by the pulse width offset . Offset is occasionally also stated in seconds. PWM signal output
- The electric power inside the motor coil is controlled by a process called pulse width modulation, or PWM.
- Turning the output ON and OFF repeatedly controls the output power.
- The motor is operated by a constant voltage and pulse duration.
- The width of the voltage pulses determines the voltage that is generated in the motor coil.
- It makes use of the property of semiconductors that the intermediate state has the greatest loss while ON/OFF states have the least.
- PWM control’s exceptional controllability and great efficiency make it a popular choice for inverter circuits.
- Additionally, brushed DC motors are controlled by it.
- By varying the ON state (duty) of the inverter circuit on a regular basis, the AC voltage of a sine-wave that is best for powering the motor can be produce .
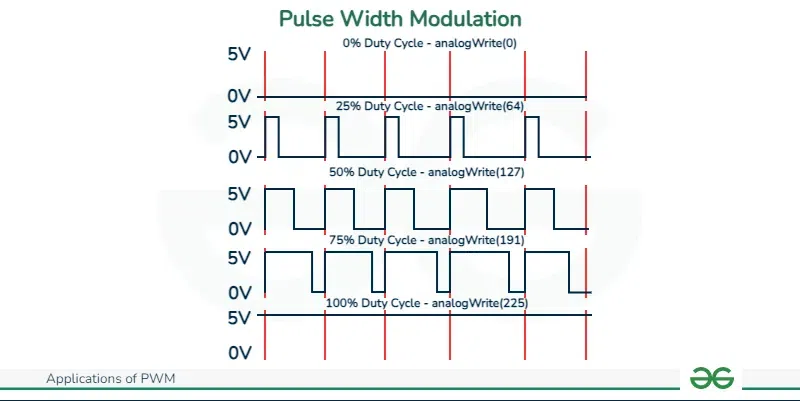
Pulse Width Modulation
The digital outputs of a microcontroller can be used to effectively control analog circuits through the use of pulse-width modulation, or PWM. PWM has a wide range of uses, from power conversion and control to communications. PWM is commonly used in various applications, such as adjusting the brightness of lights, controlling the speed of electric motors, facilitating ultrasonic cleaning processes, and serving numerous other functions.
In essence, a PWM is a digital unipolar square wave signal that allows for the desired modulation (or adjustment) of the ON time length. In this manner, a microcontroller can be used to regulate the amount of power supplied to the load.
The signal’s MARK (or M) and SPACE (or S) times are sometimes used to refer to the ON and OFF times, respectively. Three characteristics are of interest here: the duty cycle of the signal, its frequency (or period), and its amplitude.
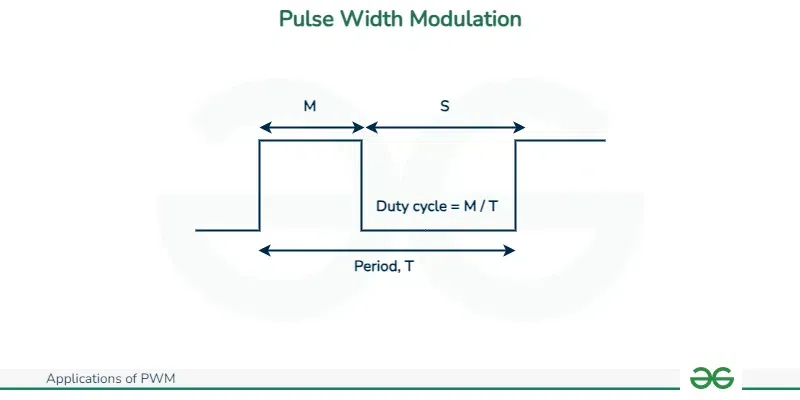
Generating Pulse Width
Working Principle of PWM
Signal Generation: A microcontroller or a separate PWM generator circuit generates a periodic signal, usually a square wave, which is the first step in the PWM process.
- The PWM frequency is the constant frequency of this periodic signal.
Duty Cycle Control: Adjusting this periodic signal’s duty cycle is essential to PWM.
- The duty cycle is a measurement of the percentage of the signal’s total duration that the signal spends in the high state (ON).
- Duty Cycle (%) is equal to (ON Time / Total Time) * 100 in mathematics.
Controlled Output: Next, a device like a motor driver, LED driver, or heating element controller receives the PWM signal.
To calculate how much power or intensity to give the load, the device analyzes the duty cycle.
.webp)
Pulse With Modulation Principle
- The PWM signal depicted in the diagram has a 50% duty cycle, meaning that its ON (high state) and OFF (low state) times are equal.
- The PWM signal’s frequency controls how frequently the cycle repeats.
- You have control over the average power given to the load by adjusting the duty cycle. For instance, a higher duty cycle corresponds to greater power (faster motor, brighter LED, etc.), and a lower duty cycle corresponds to less power.
PWM Management
A modulation technique called pulse width modulation (PWM) produces pulses with varying widths to indicate the magnitude of an analog input signal. When a signal has a large amplitude, the output switching transistor is on more of the time, and when it has a low amplitude, it is off more of the time. An analog circuit that does not drift over time is more expensive to manufacture than a PWM circuit due to its digital nature, which allows it to be fully on or off.
PWM is frequently used in ROV applications to regulate a DC motor’s speed and/or a lightbulb’s brightness. For instance, the target would get 50% of the voltage on average and run at if the line were closed for 1 μs, opened for 1 μs, and then repeatedly repeated.
Let’s we Discuss in Detail about the applications of PWM
Pulse Width Modulation (PWM) Applications
Given Below are the Applications of PWM :
- Changing the Screen’s Brightness By Utilizing PWM
- Switching Power Supplies
- Heating Systems
- Audio Amplifiers
- Battery Charging
- Servo Control
- Inverters and Frequency Control
- Using Arduino to Implement PWM
- Motor Control
1. Changing the Screen’s Brightness By Utilizing PWM
With PWM, the brightness of the screen is adjusted by turning it on and off alternately, rather than depending on power. The PWM dimming screen illuminates and turns off the screen continuously when it is on, however it does not continuously emit light. Our eyes interpret something as always on with varying brightness depending on duty cycles if it changes quickly enough. The screen gets brighter as the duty cycle increases.
- PWM is a brightness control method utilized in phone displays.
- In order to solve issues about screen flicker sensitivity, this technology is essential.
- Headaches or eye strain are brought on by phones with low PWM dimming functionality.
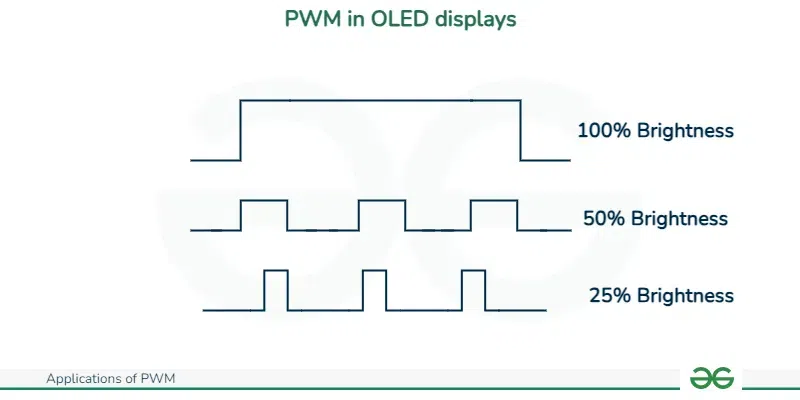
PWM in OLED displays
2. Switching Power Supplies
A key component of switch-mode power supplies (SMPS) is PWM. By adjusting the ON and OFF periods of the switching elements (like transistors or MOSFETs), it aids in managing the output voltage. SMPS are utilized in a wide range of electrical products, including high-power industrial applications and power adapters.
In order to keep output PWM voltage control within the necessary limits under varying load conditions, switch-mode power supplies need to incorporate a feedback control loop. This involves feeding the power supply’s output voltage back via an error amplifier to produce a control signal.
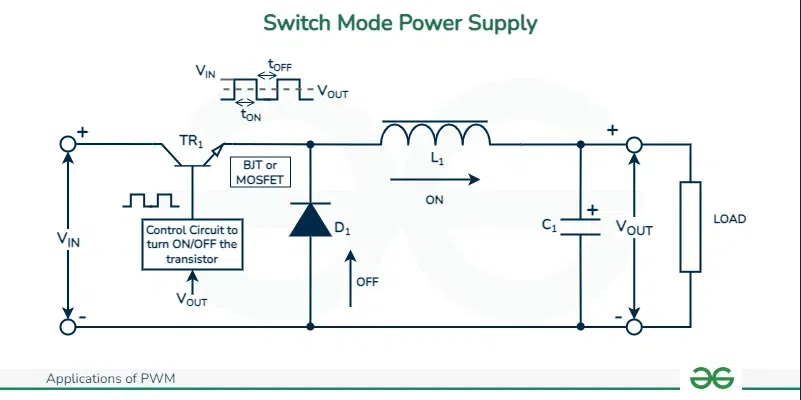
Switch Mode Power Supply
3. Heating Systems
PWM regulates the quantity of heat applied to a load in heating systems, which include soldering stations, electric heaters, and ovens. The average power supplied to the heating element can be precisely regulated by varying the duty cycle, providing accurate temperature control. The electrical pulse to the heater will remain on for a longer period of time the lower the setpoint feedback temperature. As a result, the heater will receive more power on average, raising the temperature until it reaches the intended setpoint.
4. Audio Amplifiers
High-efficiency pulse waveforms that power speakers are created from audio signals by Class-D audio amplifiers using PWM. Portable music players employ PWM amplifiers because they are an energy-efficient option. PWM amplifiers have the primary benefit of having an exceptionally high efficiency (>90%). As a result, just 25% of the heat from prior designs needs to be dissipated, which results in substantially lower amp temperatures and eliminates the need for heat sinks.
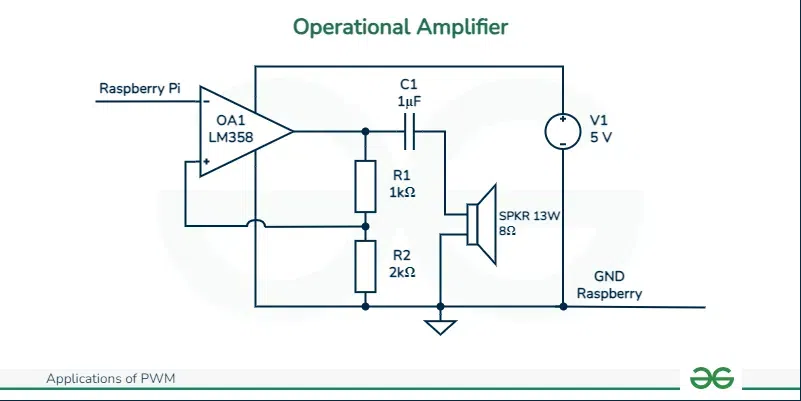
Operational Amplifier
5. Battery Charging
Systems that use sun charge controllers or other PWM charging controllers are used to charge batteries. To ensure that batteries are charged to the best possible degree and increase their lifespan and efficiency, they control the charging voltage and current. The best way to switch the power devices of the solar system controller and achieve consistent voltage battery charging is to use pulse width modulation, or PWM. The solar array’s current tapers in accordance with the battery’s state and recharging requirements when it is in PWM regulation.
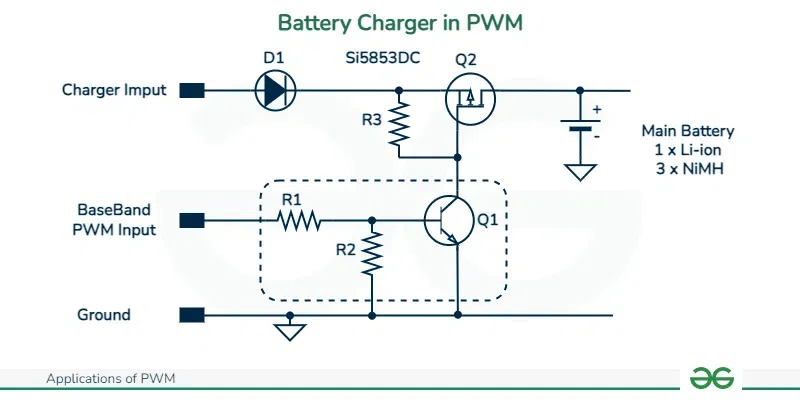
Battery Charger in PWM
6. Servo Control
Automation systems, robotics, and RC (remote control) devices all employ PWM signals to operate servo motors. The servo motor’s position is determined by the duty cycle of the PWM signal, which provides exact control over angular displacement.
A pulse width modulated (PWM) signal is used to drive servo motors. Typically, servo motors consist of three wires: the control signal, ground, and power. The majority of servos rotate fixedly in the range of 0° to 180°, beginning and finishing at fixed locations in relation to the motor.
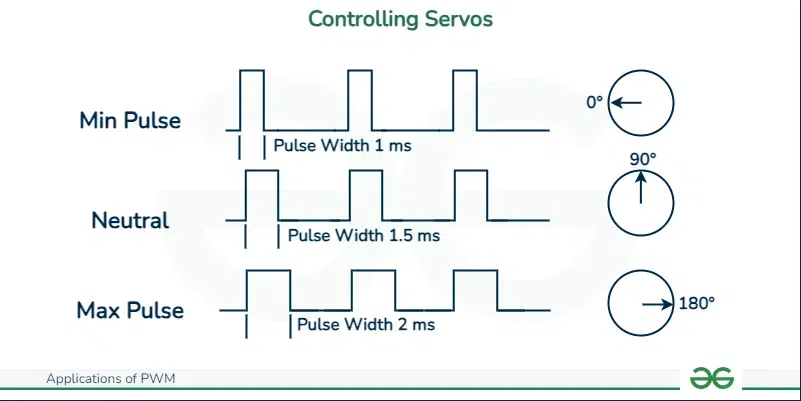
Controlling Servos
7. Inverters and Frequency Control
Inverters use PWM techniques to effectively convert DC power to AC power. Furthermore, PWM modifies the frequency of the output waveform in variable frequency drives (VFDs) to regulate the speed of AC motors.
This approach involves feeding the inverter a fixed dc input voltage, and controlling the on and off times of the inverter’s component parts to produce a regulated ac output voltage. This technique, known as pulse-width modulation (PWM) control, is the most widely used one for adjusting the output voltage.
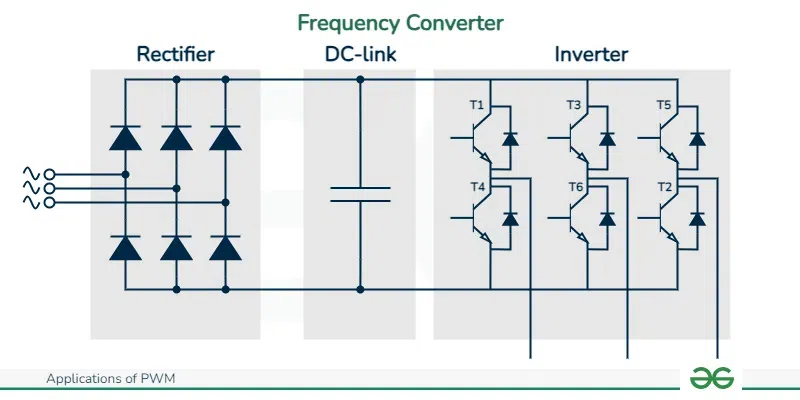
Frequency Converter
8. Using Arduino to Implement PWM
On Arduino, PWM may be done in a number of ways. Six pins on the arduino board—pins 3, 5, 6, 9, 10, and 11—can be used to output a PWM wave using the analogWrite() method. The PWM pins can produce a steady square wave with a given duty cycle by invoking the AnalogWrite() function. These pins typically have frequencies of 490 Hz, but pins 5 and 6 of Seeeduino or boards similar to it have frequencies of 980 Hz.
Arduino pins have a 5V output voltage, and as can be seen below, different duty cycles result in various voltage levels:
Duty Cycle
|
Output Voltage Levels
|
0%
|
0V
|
25%
|
1.25V
|
50%
|
2.5V
|
75%
|
3.75V
|
100%
|
5V
|
9. Motor Control
A DC motor’s speed is proportional to the power supply voltage when its load, or torque, is constant. As was previously said, the duty cycle of the PWM controls the output voltage level, meaning that the motor speed may be adjusted using the PWM.
Hardware Link
- For Motor, the same hardware connection would apply.
- Attach pin 9 to the motor and GND.
- A voltage regulator may be required to connect the motor to the Arduino, as the Arduino can only output a maximum of 5V of voltage.
Advantages of PWM
- Power electronics systems can benefit from pulse-width modulation (PWM) in a number of ways, including less harmonic distortion and noise in the output waveform, which enhances power quality and lowers electromagnetic interference (EMI).
- The power device is either fully on or totally off, decreasing switching losses and thermal stress, it also improves the efficiency and reliability of the converter.
- PWM’s changeable duty cycle, which ranges from zero to one, allows for a wide range of output voltage and current control, enabling the converter to function in a variety of modes and applications.
- PWM also makes the design and implementation of the converter simpler because it eliminates the need for intricate feedback circuits, transformers, and filters.
Disadvantages of PWM
There are certain disadvantages to PWM in power electronics systems.
- It shortens the power device’s lifespan, increases switching losses, and emits more electromagnetic interference by raising the switching frequency and stress of the device.
- To create and apply the PWM signals to the power device, a high-performance controller and driver circuit are also required, which could raise the converter’s cost and complexity.
- It can have negative consequences on the load, especially for nonlinear or sensitive loads like motors, batteries, or LEDs.
- These impacts include torque pulsations, acoustic noise, voltage spikes, and current ripples.
Conclusion
To sum up, pulse width modulation, or PWM, is a flexible method that can be applied to a wide range of situations to effectively control power delivery, modulate signals, and regulate systems. It makes it possible to precisely manage a variety of factors, including heating components, LED brightness, motor speed, and audio output. Due to its capacity to adjust a signal’s duty cycle, PWM is a vital component of contemporary automation, power management, and electronics systems.
Applications of PWM – FAQs
What is PWM, or pulse width modulation?
A method called pulse width modulation (PWM) is used to encode data into a signal’s pulse width. It entails changing the pulses’ width while maintaining a steady frequency. This technique is frequently used to mimic analog signals using digital systems or to regulate the power supplied to electrical equipment.
How does one compute the Poynting vector?
The following formula is used to get the Poynting vector:
S = E * H
where 𝐻 H is the vector of the magnetic field and 𝐸 E is the vector of the electric field. The direction of energy flow is shown by the cross product of these two vectors, and the energy flow per unit area is represented by the magnitude of S.
What connection exists between resolution and PWM frequency?
The PWM signal’s rate of transition between the on and off states is determined by its frequency. Although each cycle is shorter at higher frequencies, smoother transitions may come at the expense of resolution (fine control). Although lower frequencies provide more resolution, in applications like LED dimming, they may cause audible noise or perceptible flicker.
How do PWM signals get produced by microcontrollers?
Microcontrollers use timers or specialized PWM modules to generate PWM signals. With the help of these modules, the microcontroller can produce PWM signals with duty cycle and frequency adjustments. Timers and GPIO (General Purpose Input/Output) pins can also be used to provide software-based PWM, however specialist PWM modules frequently offer more flexible and exact control.
Share your thoughts in the comments
Please Login to comment...