What is Total Quality Management (TQM), and Just in Time (JIT) & KANBAN ?
Last Updated :
18 Oct, 2023
Total Quality Management (TQM)
Total Quality Management (TQM) is a management philosophy that fosters a culture of excellence, emphasizing continual improvement, customer satisfaction, and active employee involvement. TQM places a strong emphasis on understanding and meeting the needs and expectations of customers through effective communication and feedback mechanisms. By integrating quality principles into the very fabric of an organisation, TQM seeks to optimize processes, enhance products and services, and drive overall customer satisfaction. A key component of TQM is the unwavering commitment to ongoing improvement, where all employees are encouraged to identify areas for enhancement, eliminate waste, and work collaboratively toward achieving incremental gains. Moreover, TQM recognizes the invaluable contribution of employees and empowers them to actively participate, make decisions, and take ownership of quality initiatives.
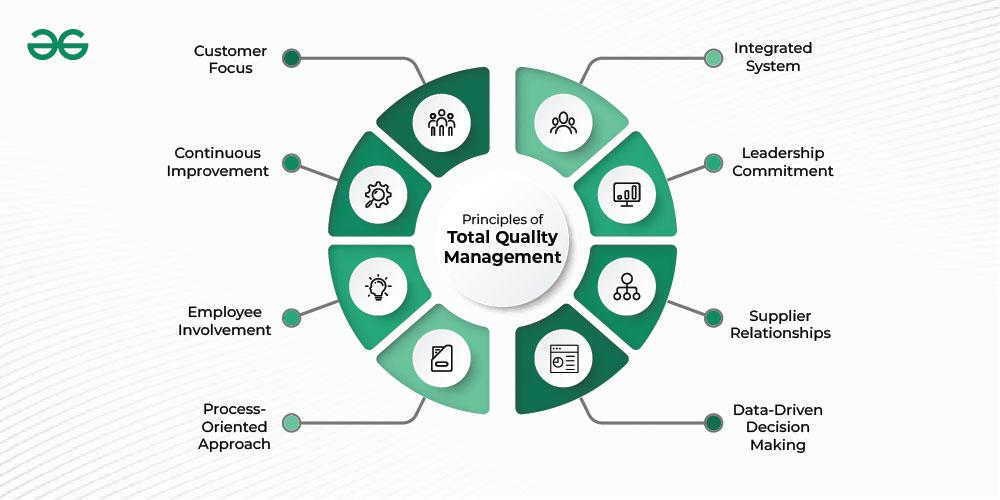
Principles of Total Quality Management (TQM)
The principles of Total Quality Management (TQM) encompass the following:
- Customer Focus: TQM places a strong emphasis on understanding and meeting customer needs and expectations. It involves gathering customer feedback, conducting market research, and using that information to improve products, services, and overall customer satisfaction.
- Continuous Improvement: TQM promotes a culture of continual improvement throughout the organisation. It encourages all employees to actively participate in identifying opportunities for enhancement, eliminating waste, and implementing incremental improvements in processes, products, and services.
- Employee Involvement: TQM recognizes the importance of involving employees at all levels in quality improvement initiatives. It fosters a collaborative and empowered work environment, where employees are encouraged to contribute ideas, make decisions, and take ownership of quality-related activities.
- Process-Oriented Approach: TQM focuses on managing and improving processes rather than individual tasks or departments. It involves mapping, analyzing, and optimizing workflows to enhance efficiency, effectiveness, and consistency.
- Data-Driven Decision-Making: TQM relies on the collection and analysis of relevant data to support decision-making. It emphasizes the use of facts and figures to identify areas for improvement, measure performance, and monitor progress toward quality objectives.
- Supplier Relationships: TQM recognizes the significance of strong relationships with suppliers. It emphasizes collaboration, communication, and mutually beneficial partnerships with suppliers to ensure the quality of inputs and optimize the overall value chain.
- Leadership Commitment: TQM requires committed leadership that actively supports and promotes quality principles throughout the organisation. Leaders serve as role models, set clear quality goals, provide necessary resources, and foster a culture that prioritizes continuous improvement and customer satisfaction.
Just in Time (JIT) and KANBAN
-and-KANBAN-copy.webp)
Just-in-Time (JIT) is a production and inventory management philosophy that aims to minimize waste and maximize efficiency by producing and delivering products or services exactly when they are needed. The core concept of JIT is to eliminate any form of waste, including excess inventory, overproduction, waiting time, unnecessary movement, and defects. By synchronizing production processes with customer demand, JIT reduces inventory carrying costs, minimizes lead times, and improves overall responsiveness. It emphasizes a pull-based system, where production is triggered by actual customer orders, rather than pushing products into the market. JIT requires close coordination and collaboration between suppliers and manufacturers to ensure timely delivery of raw materials and components.
KANBAN, on the other hand, is a visual scheduling system that supports the principles of JIT. It uses visual cues, such as cards or signals, to control the flow of work and materials within a production system. KANBAN provides real-time information about the status of inventory, production, and customer demand. Each work centre or production stage has a designated KANBAN card that represents a specific quantity of work or material. As work or materials are consumed, the KANBAN card is returned to the previous stage to trigger replenishment. This pull-based system helps to avoid overproduction, reduces excess inventory, and improves production flexibility. KANBAN allows for better visibility, smoother workflow, and efficient resource allocation throughout the production process.
Techniques of Just in Time (JIT) and KANBAN
Just-in-Time (JIT) and KANBAN are two powerful techniques that work hand in hand to optimize production and inventory management:
The techniques associated with Just-in-Time (JIT):
- Demand-Driven Production: JIT emphasizes producing goods or services based on actual customer demand rather than relying on forecasts. This approach allows companies to avoid overproduction and minimize inventory holding costs by closely monitoring customer orders and adjusting production accordingly.
- Lean Manufacturing: JIT incorporates lean manufacturing principles to eliminate waste and improve efficiency. Techniques such as Value Stream Mapping (VSM) help identify and eliminate non-value-added activities, streamline processes, and optimize resource utilization.
- Quick Changeover (SMED): JIT focuses on reducing setup or changeover times between different product runs or production processes. Techniques like Single-Minute Exchange of Die (SMED) enable companies to minimize downtime and enhance flexibility by standardizing setups, utilizing tooling techniques, and implementing parallel operations.
- Continuous Improvement: JIT fosters a culture of continuous improvement, empowering employees to identify and address inefficiencies. Techniques like Kaizen (continuous improvement through small incremental changes) and Poka-Yoke (error-proofing) are applied to enhance processes, quality, and productivity.
The techniques associated with KANBAN:
- Visual Boards: KANBAN utilizes visual boards or cards to provide a clear representation of work progress and status. These visual tools enable teams to easily track and manage workflow, displaying essential information such as task or product details, quantity, and location.
- Pull System: KANBAN operates on a pull-based system, where work or materials are pulled through the production process based on actual demand. As one stage completes its work, it signals the previous stage to produce and supply the required quantity, ensuring a smooth flow and avoiding overproduction.
- Limited Work in Progress (WIP): KANBAN sets limits on the number of tasks or items in progress at any given time. By implementing WIP limits, teams prioritize completing existing work before starting new tasks, reducing bottlenecks, and improving overall throughput.
- Continuous Flow: KANBAN strives to establish a continuous flow of work by maintaining a balanced workload across different stages or teams. This technique prevents work from accumulating and promotes a steady and efficient production rhythm.
Share your thoughts in the comments
Please Login to comment...