What is Quality Control?
Quality Control (QC) is a systematic process that plays a crucial role in ensuring the consistent delivery of high-quality products or services. At its core, Quality Control involves a set of activities and techniques designed to monitor, assess, and regulate various elements of the production process, with the ultimate goal of meeting predetermined standards and specifications. This comprehensive approach covers every stage, from the initial phases of production to the final delivery of goods or services. By implementing Quality Control measures, organizations can identify and rectify defects, errors, or deviations from established standards, thereby guaranteeing the reliability and conformity of their offerings. In essence, Quality Control encompasses a range of methodologies and tools, including inspections, tests, and statistical analyses, aimed at validating that products or services meet predefined quality benchmarks. This process is not only reactive, addressing issues after they arise, but also proactive, incorporating preventive measures to minimize the occurrence of defects. The effectiveness of QC lies in its ability to ensure that every output aligns with the specified quality criteria, fostering customer satisfaction, regulatory compliance, and the overall success of an organization in a competitive market.
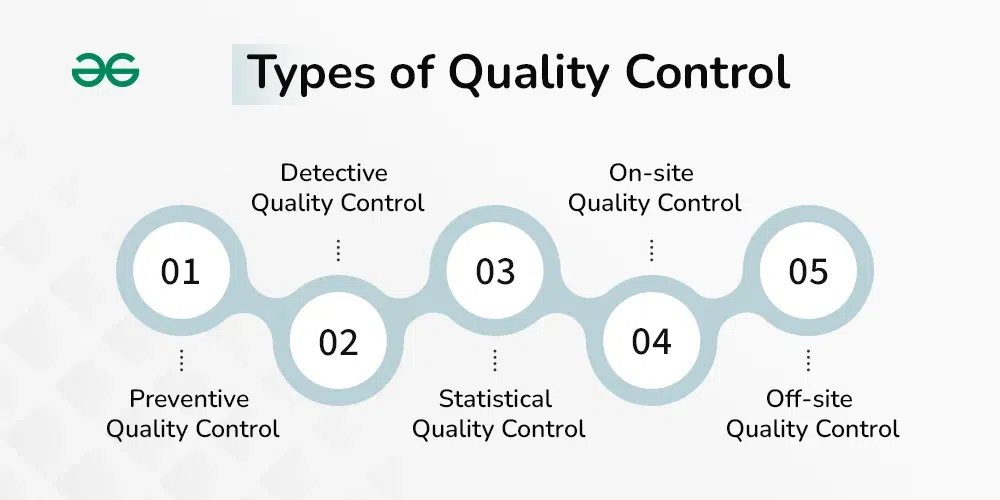
Geeky Takeaways:
- Quality Control is a process through which a business seeks to ensure that product quality is not compromised.
- Quality Control helps in determining whether they are within the specifications for the final product.
- It is highly dependent on the product or industry for measuring quality.
- The food industry uses quality control measures to make sure customers do not get sick from their products.
- Quality control provides safeguards to make sure damaged products do not end up with customers.
Why is Quality Control Needed?
1. Customer Satisfaction: Quality Control is indispensable for ensuring that the final products or services meet or exceed customer expectations. By maintaining high quality, organizations can enhance customer satisfaction, build trust, and foster long-term relationships. Satisfied customers are more likely to be repeat buyers and advocates for the brand.
2. Compliance with Standards: Quality Control is needed to ensure that products or services adhere to industry-specific standards and regulations. Meeting these standards not only reflects a commitment to quality but also helps in avoiding legal issues and regulatory penalties, ensuring ethical business practices.
3. Risk Mitigation: Another crucial is the role of Quality Control in risk reduction. It helps in identifying and rectifying defects early in the production process, minimizing the probability of costly recalls, product failures, and customer complaints. This, in turn, safeguards the reputation of the company.
4. Cost Control: Quality Control is essential for controlling costs associated with defects and errors. By detecting and addressing issues early on, organizations can avoid expensive rework, minimize waste, and optimize resource utilization, contributing to overall operational efficiency.
5. Continuous Improvement: Quality Control is necessary to instill a culture of continuous improvement within an organization. Through the identification of areas for enhancement in processes and products, Quality Control promotes ongoing learning and adaptation, fostering innovation and competitiveness.
Why is Quality Control Important?
1. Brand Reputation: Maintaining a high level of quality through Quality Control practices contributes significantly to building and sustaining a positive brand reputation. Consistency in delivering reliable products or services enhances consumer trust, leading to brand loyalty and positive word-of-mouth.
2. Customer Loyalty: Quality Control is important for fostering customer loyalty. When customers experience consistent quality, they are more likely to remain loyal to a brand. Loyalty, in turn, results in repeat business and increased customer lifetime value.
3. Competitive Advantage: Quality Control provides a distinct competitive advantage in the market. Organizations that prioritize and achieve superior quality stand out from their competitors, attracting discerning customers who are willing to pay a premium for reliability and excellence.
4. Risk Mitigation: Quality Control is essential for risk mitigation. By identifying and addressing potential issues before they escalate, organizations can prevent reputational damage, legal complications, and financial losses. A robust Quality Control system acts as a safety net against uncertainties.
5. Continuous Improvement: Quality Control contributes to a culture of continuous improvement by systematically analyzing processes and outputs. This ongoing evaluation and refinement result in increased efficiency, reduced waste, and the ability to adapt to changing market conditions.
Types of Quality Control
1. Preventive Quality Control: Preventive QC focuses on identifying and addressing potential issues before they occur in the production process. This involves implementing measures such as employee training, proper equipment maintenance, and process optimization to minimize the likelihood of defects.
2. Detective Quality Control: Detective QC involves identifying and correcting issues during or after the production process. This may include inspections, testing, and monitoring to catch defects that may have occurred despite preventive measures. The goal is to detect and address problems promptly.
3. Statistical Quality Control: Statistical QC utilizes statistical methods to monitor and control processes. This involves collecting and analyzing data to identify variations and trends, allowing organizations to make informed decisions and adjustments to maintain consistent quality.
4. On-site Quality Control: On-site QC involves conducting inspections and tests at the production site. This ensures that products meet quality standards before they are released to the market. On-site QC is particularly crucial in industries where variations in production conditions can impact quality.
5. Off-site Quality Control: Off-site QC refers to inspections and tests conducted away from the production site. This could involve sending samples to a third-party laboratory for testing, and providing an independent assessment of product quality to ensure objectivity and transparency.
Quality Control Process
1. Define Standards: Establishing clear and detailed quality standards is the initial step in the Quality Control (QC) process. These standards serve as benchmarks against which products or services are mostly evaluated. Defining precise criteria ensures a common understanding within the organization and provides a basis for consistent quality assessment.
2. Plan Quality Control Activities: Once standards are in place, a comprehensive plan is developed to outline the specific QC activities that need to be conducted. This plan includes the frequency of inspections, testing protocols, and the responsibilities of various team members. Planning ensures that QC efforts are systematic, thorough, and aligned with organizational goals.
3. Execute Quality Control Activities: The planned QC activities are implemented during the production process. This involves inspections, tests, and measurements conducted according to the predetermined plan. Regular and systematic execution of these activities helps in identifying deviations from established standards and ensures that quality is monitored throughout the entire production cycle.
4. Evaluate Results: Data collected from inspections and tests are thoroughly evaluated to determine whether the products or services meet the defined quality standards. This evaluation may involve statistical analysis, trend identification, and comparison against benchmarks. Understanding the results allows for informed decision-making regarding the acceptability of the output.
5. Take Corrective Action: Based on the evaluation, any identified deviations or non-conformities trigger corrective actions. These actions can range from immediate adjustments in the production process to long-term process improvements. The goal is not only to address current issues but also to prevent their recurrence in future productions.
What are the Benefits of Quality Control?
1. Consistency: One of the primary benefits of QC is the establishment and maintenance of consistency in the quality of products or services. By adhering to predefined standards, organizations ensure that each output meets the same level of excellence, fostering reliability and predictability.
2. Cost Savings: QC contributes to cost savings by identifying and addressing defects early in the production process. Early detection minimizes the need for expensive rework, reduces waste, and optimizes resource utilization. As a result, operational costs associated with poor quality are significantly lowered.
3. Customer Satisfaction: QC plays a pivotal role in enhancing customer satisfaction. Products or services that consistently meet or exceed quality standards lead to satisfied customers. This satisfaction not only ensures repeat business but also contributes to positive word-of-mouth, attracting new customers.
4. Market Credibility: The consistent delivery of high-quality products or services enhances the market credibility of an organization. A positive reputation for quality builds trust among consumers, partners, and stakeholders. This credibility can be a powerful differentiator in a competitive business landscape.
5. Continuous Improvement: QC fosters a culture of continuous improvement within an organization. By regularly evaluating results and implementing corrective actions, companies can identify areas for enhancement in processes and products. This commitment to ongoing improvement ensures adaptability and competitiveness in the market.
Quality Control Roles and Responsibilities
1. Quality Control Manager: The Quality Control Manager oversees the entire QC process. Responsibilities include defining quality standards, developing QC plans, and ensuring the effective execution of QC activities. The manager also plays a crucial role in communicating quality expectations across the organization.
2. Inspector/Tester: Inspectors and testers are responsible for conducting on-site inspections and tests. They closely examine products or services to ensure they meet established standards. These individuals play a hands-on role in identifying any deviations and contribute to the overall quality assurance process.
3. Quality Analyst: Quality analysts are involved in analyzing data and results obtained from QC activities. They use statistical methods and data analysis tools to identify trends, patterns, and areas for improvement. Their insights contribute to informed decision-making and long-term quality enhancement.
4. Process Improvement Specialist: This role focuses on identifying opportunities for process improvement based on QC data. Process improvement specialists collaborate with various teams to implement changes that enhance efficiency, reduce defects, and contribute to overall quality optimization.
5. Training Coordination: Training coordinators are responsible for developing and implementing training programs related to QC. They ensure that team members are adequately trained in QC procedures, standards, and methodologies. Continuous training contributes to a skilled and knowledgeable workforce.
Quality Control Methods
1. Inspection: Inspection involves a visual examination of products or services to ensure they meet predefined quality standards. This method is commonly used in manufacturing, construction, and various industries where the physical attributes of the product are critical.
2. Testing: Testing involves subjecting products or services to various tests to assess their performance, durability, or functionality. This method is prevalent in industries such as electronics, automotive, and software development, where the functionality and reliability of products are paramount.
3. Statistical Sampling: Statistical sampling involves selecting a representative sample from a larger population for testing. This method is widely used to conclude the entire production batch based on the analysis of a smaller, statistically significant sample.
4. On-site Quality Control: On-site QC involves conducting inspections and tests directly at the production site. This method ensures real-time monitoring of the production process, allowing for immediate corrective actions if deviations from quality standards are identified.
5. Off-site Quality Control: Off-site QC involves sending samples or products to external laboratories or third-party quality assurance providers for testing. This method provides an independent assessment of quality and is often used when objectivity and impartiality are crucial.
Quality Control Careers
1. Quality Control Engineer: Quality Control Engineers are professionals responsible for designing, implementing, and managing quality control systems. They ensure adherence to quality standards, analyze data, and identify areas for improvement in production processes.
2. Quality Inspector: Quality Inspectors play a hands-on role in conducting inspections and tests on products during or after the production process. They are responsible for identifying defects, ensuring compliance with standards, and maintaining quality records.
3. Data Analyst in Quality Control: Data Analysts in Quality Control focus on analyzing data collected from QC activities. They use statistical methods and data analysis tools to identify trends, patterns, and areas for improvement, contributing valuable insights to the decision-making process.
4. Quality Assurance Coordinator: While related to Quality Control, Quality Assurance Coordinators focus on developing and implementing overall quality assurance processes. They work to prevent defects and ensure that processes are designed to produce consistent and high-quality outputs.
5. Quality Control Manager: Quality Control Managers oversee the entire QC process within an organization. They define quality standards, develop QC plans, and ensure effective execution. Managers also play a key role in communicating quality expectations across the organization.
Examples of Quality Control
1. Manufacturing: In manufacturing, quality control involves inspecting products on the production line to ensure they meet specific standards. This may include visual inspections, measurements, and testing to identify and address defects before products are released.
2. Software Development: In software development, quality control is achieved through code reviews, testing, and validation processes. Software testers ensure that the software meets functional and performance requirements, identifying and fixing bugs before deployment.
3. Food Industry: The food industry employs quality control to ensure the safety and quality of food products. This includes inspections, testing for contaminants, and adherence to hygiene standards to guarantee that food items meet regulatory requirements.
4. Construction: In construction, quality control involves inspecting materials, monitoring construction processes, and conducting tests on structures. This ensures that buildings and infrastructure projects meet safety standards and adhere to design specifications.
5. Healthcare: In healthcare, quality control is vital in maintaining the accuracy of medical diagnoses and treatments. Laboratories employ quality control measures in testing procedures, ensuring the reliability and precision of medical test results.
Quality Control Vs. Quality Assurance
Basis
|
Quality Control (QC)
|
Quality Assurance (QA)
|
Focus |
Emphasizes detecting and correcting defects. |
Emphasizes preventing defects and improving processes. |
Stage of Process |
Applied during or after the production process. |
Applied before or during the development process. |
Responsibility |
Involves checking products or services. |
Involves setting standards and creating processes. |
Goal |
Ensures the end product meets quality standards. |
Ensures processes are designed for quality outcomes. |
Scope |
Narrow focus on specific outputs. |
Broad focus on overall process improvement. |
Frequently Asked Questions (FAQs)
1. Is Quality Control the same as Quality Assurance?
Answer:
No, QC and QA are distinct but related processes. QC focuses on detecting and correcting defects in the final product, while QA focuses on preventing defects by establishing and improving processes.
2. How does Quality Control contribute to profitability?
Answer:
QC contributes to profitability by reducing defects and rework, minimizing operational costs, and enhancing customer satisfaction. High-quality products often lead to increased sales and customer loyalty.
3. Can Quality Control be automated?
Answer:
Yes, certain QC processes can be automated using technologies such as machine vision, sensors, and artificial intelligence. Automation helps improve efficiency and accuracy in quality control.
4. What is the role of statistical methods in Quality Control?
Answer:
Statistical methods in QC, such as Six Sigma, help analyze data to identify patterns, variations, and areas for improvement. These methods provide a quantitative approach to ensuring consistent quality.
5. How does Quality Control benefit customer satisfaction?
Answer:
QC ensures that products or services consistently meet or exceed quality standards, leading to higher customer satisfaction. Satisfied customers are more likely to be loyal and recommend the brand to others.
Share your thoughts in the comments
Please Login to comment...