What is Industrial Control System (ICS)?
Last Updated :
12 Apr, 2024
Industrial control systems (ICS) are a broad word used in manufacturing to refer to integrating network connections, hardware, and software to support vital infrastructure. In the context of critical infrastructure, ICS assets facilitate the efficient administration and operation of crucial services.
Devices for monitoring energy production, distribution, and transmission are among these assets in the power grid. An industrial control system manages production, distribution, handling of products, and manufacturing in the industrial sector.
What is an Industrial Control System (ICS)?
An industrial control system is an electronic control system and industrial process control is mostly used in instrumentation. Small modular panel-mounted controllers and massive interactive distributed control systems with hundreds of field connections are examples of different-sized control systems. This is designed to efficiently handle duties electronically and operates differently based on the industry. The manufacturing, transportation, energy, and water treatment sectors are just a few of the key infrastructure and industrial sectors that employ the devices and protocols found in an ICS today.
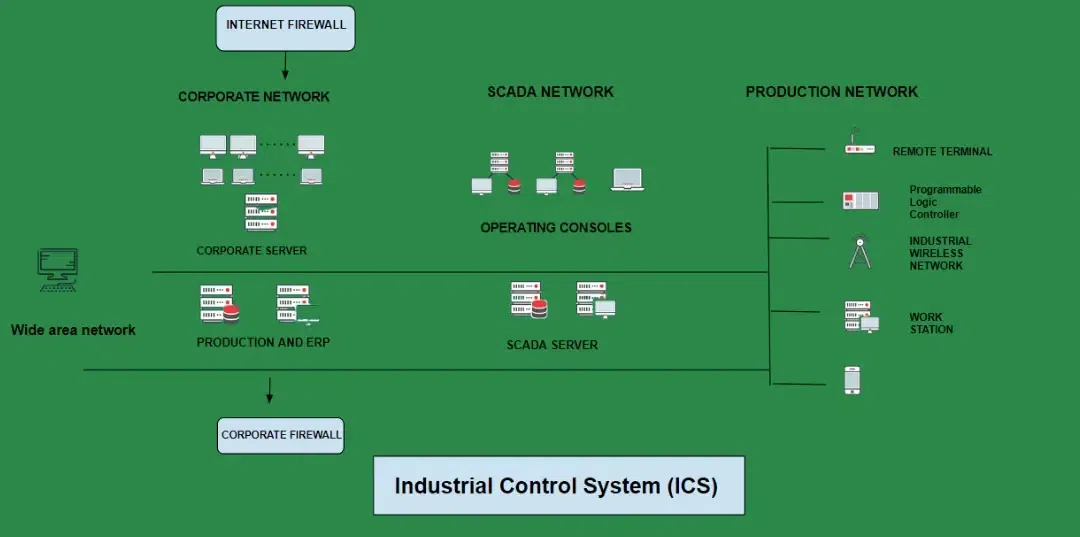
Industrial Control System (ICS)
Types of Industrial Control System (ICS)
- Distributed Control System (DCS): This is a solution for managing production systems located in one place. A DCS uses a controller that receives a setpoint and may tell valves or even an actuator how to function to maintain the intended setpoint. Field data can be utilized in complex control schemes including data from other regions of the plant, retained for later use, or used for simple process control. The primary function of SCADA systems is to monitor and control field sites remotely from a centralized control system.
- Supervisory Control and Data Acquisition (SCADA): A SCADA system cannot offer total control. Rather, its functionalities center around granting authority at the supervisory level. Generally speaking, SCADA systems consist of dispersed devices (commercial hardware modules or Programmable Logic Controllers, or PLCs) at different places.
- Actual ICS implementation: Integrating capabilities from both DCS and SCADA into an ICS environment typically results in a hybrid system. This makes it feasible to integrate features and functions from the two systems to fulfill specific operational requirements.
Key Industrial Control System (ICS) Components
- IT and OT: The hardware and software solutions used to monitor and manage physical equipment in the field are examples of IT and OT variables. OT duties differ for every industry.
- Human-Machine Interface (HMI): This facilitates the control, visualization, and management of a variety of device operations.
- Programmable Automation Controllers (PAC): Compared to other systems, PACs frequently provide additional connectivity choices and a greater range of control systems capabilities.
- Field Devices: Instruments, actuators, and sensors are some of the examples of field devices, which are essential parts of an ICS.
- Data Historian: A data historian is a centralized database used to transfer data to the corporate IS after capturing all process information in an ICS context.
- Remote Terminal Unit (RTU): An RTU is a field device with a microprocessor that can accept orders and return data to the MTU.
- Remote Diagnostics and Maintenanceto: This phrase refers to recognizing, averting, and recovering from anomalous actions or malfunctions.
- Control Server: In addition to communicating with lower-level control devices, a control server houses the supervisory control software for DCS or PLC.
- Programmable Logic Controller (PLC): A form of hardware known as a programmable logic controller (PLC) is utilized as a control element of a larger system in both DCS and SCADA systems. Additionally, it offers local process management using feedback control hardware, including actuators and sensors.
Threats to Industrial Control Systems
- To enhance the system operations and productivity, every ICS regularly adopts new and updated technologies and applications in both IT and OT.
- The combination of IT and OT makes them more appealing to hackers and also can not protect SCADA and other legacy.
- When ICS equipment is immediately accessible over the internet, hackers may exploit security flaws or inadequate authentication processes to get access and compromise it.
- Phishing tactics might be used by attackers to fool staff members into disclosing their login credentials, giving them legal entry into the ICS environment.
Best Practices of Industrial Control Systems Security
- Monitor Networks: Since linked devices on ICS networks tend to be static and change infrequently, it is imperative to monitor these networks. Setting up a baseline for typical network behavior through ongoing monitoring is essential to improving security.
- Least Privilege: Many ICS protocols don’t have enough access constraints, which might allow unauthorized users to access vital and sometimes dangerous functions. To use ICS protocol-aware firewalls to mitigate this risk, it’s most critical.
- Network Segmentation: Air gaps were formerly a sufficient means of providing security for ICS networks, but they are no longer so. To guarantee the security of equipment not meant for internet access, network segmentation is becoming more and more important.
- Secure Remote Access: To monitor and operate globally dispersed ICS assets, remote access is often necessary. But it’s crucial to make sure that strong encryption, access control, and authentication procedures are in place when establishing this access.
Conclusion
In this article, we have learned about industrial control systems (ICS). Industrial control system refers to a group of terms used to characterize various kinds of control systems, to run and/or automate industrial processes this comprises the machinery, networks, systems, and controls needed.
Frequently Asked Questions on Industrial Control Systems – FAQs
What is the most common industrial control system?
The most common industrial control system are Supervisory Control and Data Acquisition and Distributed Control Systems, popular forms of Industrial Control Systems (ICSs).
Why control systems are important?
You can utilise this crucial information to influence future production decisions with the help of an efficient control system. It is possible to identify system flaws, which gives management the ability to decide on production and manufacturing processes more effectively.
Which type of control system is commonly used in industrial applications?
Distributed Control System is commonly used in industrial applications. It is often utilized in sectors like manufacturing, electricity production, chemical synthesis, oil refineries, and the treatment of water and wastewater.
Share your thoughts in the comments
Please Login to comment...