Variable Frequency Drive
Last Updated :
19 Apr, 2024
Variable Frequency Drive (VFD) is the type of AC motor drive that controls the speed and the torque. It can control the speed by changing the frequency of the current. They can also control the speed and torque of the motor by changing the voltage. They are the motors of the modern world. Most industries are now shifting to use VFD as they are easy to use and can be controlled by software. VFDs are not only used in large-scale industries but also used in small-scale industries as well.
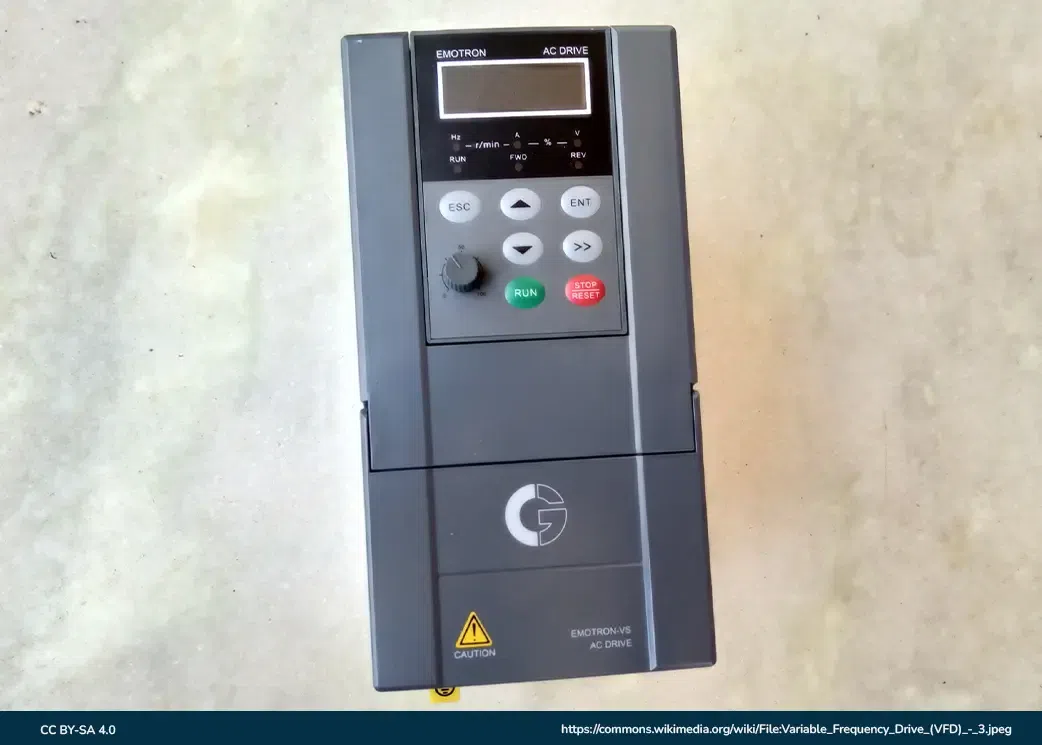
Variable Frequency Drive
What is a Variable Frequency Drive?
A Variable Frequency Drive (VFD) is a device which is used in a system that has an AC motor, Operator Interface and Controller Assembly. It is also called as Adjustable Speed Drive (ASD) or Inverter Drive.
In other words we can say that a Variable Frequency Drive is a device that controls the speed and also the torque of the AC motor by changing the frequency and voltage of the supply. We can also use VFD to Start, Stop and also control the motors speed.
The usage of VFDs has increased the performance of the work in many industries. It works on the principle of a three-phase induction motor. The benefits of using VFD are
- It improves the in controlling the process in a good manner.
- As we can control the speed, so we can save energy and power.
- We can save the resources that are being used.
Types of VFD
The VFD is of two types based on its topologies
- Voltage Source Inverter (VSI)
- Current Source Inverter (CSI)
Voltage Source Inverter (VSI)
A voltage source inverter is a device that converts DC to AC voltage. The voltage source inverter maintains a constant DC voltage at the input as it also produces AC output of which we can adjust the frequency. Voltage source inverter consists of components like transistors, thyristors, etc.
Applications Of VSI
- Used in Renewable Energy Systems like Solar Farms and Wind Farms, as they convert DC to AC output.
- Used in Electrical Vehicle Drive System as they can be used to control the speed of the vehicle by regulating AC voltage.
- Used in Uninterruptible Power Supplies (UPS) as they generate and regulate flow of AC voltage by which we do not get power outage.
Current Source Inverter (CSI)
A Current Source Inverter is a device that gives us constant current output as we get controllable AC voltage output. CSI takes the DC current from sources like batteries and converts them into three phase or single phase AC current which is controllable. The main work of CSI is to maintain the steady flow of current in the circuit. The components like IGBT, MOSFETS, etc. are used in CSI to regulate the flow of current. We can also control the direction of the current and also the magnitude.
Applications of CSI
- CSI can be used in high power AC drives as they are mostly good for industries.
- We can use CSI in single stage solar inverters like system which require conversion of DC to AC.
Components and Operation of Variable Frequency Drive
It works in four main stages
- Rectifier: In this stage the incoming frequency AC power is converted in DC by using silicon controlled rectifiers (SCR’s), Diodes, Transistors.
- DC link: As the converted DC has some fluctuations, the DC link helps and removes them. It is used to reduce the ripple.
- Inverter: This is the heart of the VFD. This coverts the fixed DC into AC by using Insulated Gate Bipolar Transition (IGBT). It forms a Variable Frequency Waveform of AC. The inverter controls the output frequency.
- Control Circuit: This is the main part of Variable Frequency Drive (VFD). Here it will receive all the input from the user and control everything. It will act as the control center and monitors voltage and the current.
Operation of Variable Frequency Drive
- Ac input: The VFD has input of AC from the mains.
- Rectification: It will convert the AC input to DC.
- DC link: Here the DC voltage is stabilized using capacitors.
- Inverter: The control system will instruct the inverter to convert the DC voltage to AC with Variable Frequency.
- AC output: The output of the Variable frequency is supplied to the motor.
- Motor Speed Control: The speed of the motor is directly connected to the frequency. So if the frequency is increased the speed is increased and if it is decreased, then it is slow speed.

Operation Of VFD
How Does a Variable Frequency Drive Work?
The Variable Frequency Drive is a motor that can control a motor by changing its frequency and the voltage that is supplied. By this we can easily control the speed, acceleration and torque of the motor. This will help us to run the motor in more efficient way and not harming the motor.
- AC to DC conversions :By using a rectifier circuit the AC power of fixed frequency is converted into DC power by the VFD. we can take an example of electric iron straightening out curved waveform of AC into flat straight line of DC voltage.
- Making the DC smooth :As the DC voltage is not proper in the start, so the VFD will use capacitor and inductors to smoothen the DC which will help us in next process.
- DC to AC conversion :In VFD we can use fast switching devices like transistor to make the DC smooth and convert them in pulses. By this we create a sine wave which is good for the motor.
- Frequency Control :In VFD we can control the frequency of the chopped up AC output, as the motor’s speed is related to the frequency of the power it receives. Now by changing the output frequency we can control the motor’s speed.
- Operation of the Brain :The brain of the main drive is digital signal processor (DSP). Here, it will receive the user commands and then it will monitor the main performance of the motor by which we can get the required frequency.
Another way of explaining the working of Variable Frequency Drive is –
- Input Power: We take the input power by connecting VFD to a AC power source. Which means we connect VFD to a three-phase power supply.
- Rectification: Now in rectification the power that is AC is converted into DC by rectifier circuit.
- DC bus: Now as the AC is converted into DC it is stored in the DC bus capacitor bank. By using a storage medium the process is smoothened.
- Inverter Section: In this section the DC power from the bus is converted into AC power that is of variable frequency.
- Pulse Width Modulation (PWM): This is the most common method we use in VFD which is used to generate variable frequency AC power. In this method power electronic devices like MOSFETS and IGBT’s are included in the process. As the width of the pulses changes the voltage and frequency can be controlled.
- Output to Motor: Now the AC power is supplied to the motor. Now we can control the speed of the motor by changing the frequency and voltage.
- Control Interface: We can set the controls as per our needs of speed, acceleration and torque. VFD also has communication protocols which is very helpful to us.
As we know that the speed of the AC motor is 
Now here we take
as synchronous speed which is in rpm.
f is the frequency in hertz.
P is the number of poles.
Now, we change the frequency and we get

We know torque of AC is –

Here, T= torque in NM ,
is the flux in weber , I is the current in Ampere.
By Changing the V/f, the flux is changed and we can Control the torque of the motor
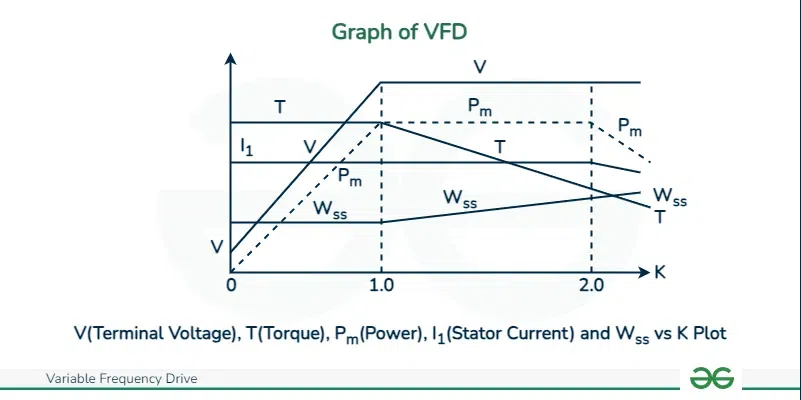
Graph Of VFD
Advantages of Variable Frequency Drive
- Energy Savings: The best advantages of Variable Frequency Drive (VFD) is that we can save a lot of energy by using them. As they can control the speed of the motor as per our needs, which helps us.
- Speed Variations: As we know by using VFD we can control the speed and also can vary it according to us, by this we can control the motor according to our means and also not harm the motor by heavy use.
- Soft Starting: As we know that by the help of slow starting the mechanical stress is reduced on the motor which helps the motor to work efficiently which increases the life span of the motor.
- Extended Machine Life and Less Maintenance: As the motor starts softly and properly the machines life is increased due to which we get benefit that we don’t have to maintain the machine on daily basis. This reduces the workload of the operator.
- High Power Factor: The power factor is the measure of how we can deliver the electrical power efficiently. By using VFD the power factor is increased and by adjusting the phase between the voltage and current the unity is 1. Which increases the machines efficiency.
Disadvantages of Variable Frequency Drive
- Higher Cost: VFD have much more cost as compared to normal motor control methods.
- Complexity : Using VFD is not as simple as to control normal methods, it requires some knowledge in programming field.
- Heat Generation: VFD generate a large amount of heat when they are in use, so we need proper ventilation system.
- Motor Compatibility : As we know VFD is a new technology, so older generation motors are not suitable for them, we need motors which are suitable for them.
- Maintenance Requirements : VFD’s require regular maintenance so that they could work properly.
- Voltage Transients : As the speed changes in an instant due to which the load on motor can increase and which can cause transients inside the system, by this the performance will be decreasing and life of the motor will shorten.
Applications of Variable Frequency Drive
VFD have many wide range of applications like
- Fans and Pumps :They are mostly used to control the speed of fans and pumps which helps in proper efficiency and reduction in energy usage. This helps in saving energy and improve the comfort.
- Conveyor Belts :VFD’s are used in conveyor belts in major and minor industries, as they provide smooth functioning. They provide smooth process in food factories and paper mills.
- Machines: VFD’s are used in many machineries which are used for speed. Many industrial machinery require VFD for smooth and nice process.
- HVAC systems: VFD’s are majorly used in HVAC systems where we require to cool down, ventilate and air condition the system. It is very useful in large scale industries.
- Textile Industry: VFD’s are used in spinning, weaving, etc in textile industries. It is very helpful as by this the process of the work is smoothened.
- Oil and Gas industries: We can use VFD in oiling and gas pumps. By this we get a nice boost in the work as it works properly.
- Agriculture: We can make good use of VFD in irrigation system, helping the agricultural sector. This will help the farmers to modernize and understand the use of machinery.
Conclusion
Now we can conclude that VFDs are very powerful technology in new world which we can use for controlling the speed of AC motors. We can get advantage in various ways like Energy Savings, Nice motor life, more flexibility in motors and advanced method to control speed of motors. VFDs are the long time answer to control the speed of the motor which needs proper maintenance and planning to get proper execution of the task.
Variable Frequency Drive – FAQs
What are the additional features of VFD?
Additional features of VFD’s are soft start/stop, braking, and motor protection.
What are Harmonics?
They are the distortions in the AC waveform that is produced by the VFD.
What are the types of motors we can use in VFD?
Motors like AC, Permanent Magnet Synchronous Motors (PMSM’s), and brushless DC motor can be used.
What are the safety considerations?
We should take Precautions like training on safety practices and knowing all the standard protocols.
Share your thoughts in the comments
Please Login to comment...