The LVDT stands for Linear Variable Differential Transformer. It converts the Linear motion into an electrical signal using an inductive transducer. Due to its superior sensitivity and accuracy over other inductive transducers, the LVDT is extensively used in many different fields. For measuring linear distance, the linear variable differential transformer (LVDT) is a precise and trustworthy tool. Today, LVDTs are used in computerized manufacturing, robotics, avionics, and machine tools, combining research facilities, high-level analysis, and analysis to detect damage caused by massive rock deformation or other movements in the subgrade of old buildings or structures. physical structure. One try. This method is used to try to detect failure in concrete slopes and warn or correct the condition. One of the special problems with historical buildings is that they can easily be damaged by small deformations in the long run.
What is LVDT?
LVDT stands for Linear variable differential transformer. It is one of the major types of Inductive transducers. LVDTs are considered the most accurate inductive sensors that measure displacement according to the polarity and magnitude of the net induced electromotive force (EMF) and are therefore also known as linear variable displacement sensors.
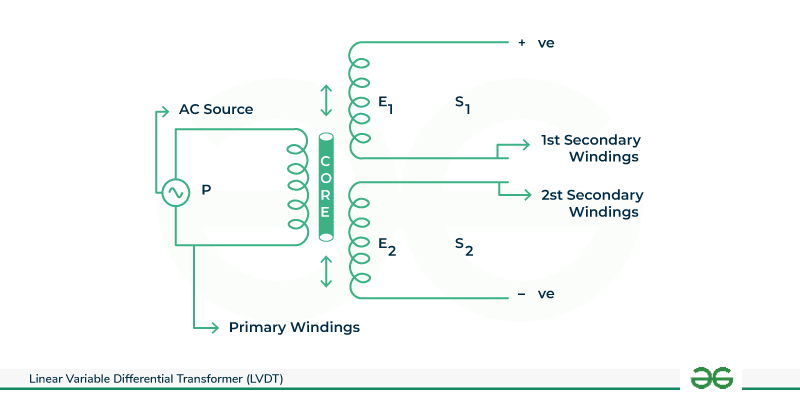
Simple LVDT Diagram
Types of LVDT
Linear Variable Differential Transformers (LVDTs) can be of many types based on their construction, size, and specific applications. Here are some common types:-
- AC LVDT: The AC LVDT is the most common and most used type of LVDT which operates on the principle of electromagnetic induction (EMI) with AC as an input. AC LVDTs are widely used for displacement measurement in various industrial applications.
- DC LVDT: This type of LVDT operates with a DC (direct current) input. These types of LVDTs are used in limited applications where a DC power source is more convenient.
- Miniature LVDT: This type of LVDT is small in size as the name suggests miniature and its stroke length is small but highly precise. There is Subminiature LVDTs also even smaller in size and best for limited-space applications.
There can be many more LVDTs based on the requirement of the application like High-Temperature LVDTs, Digital LVDTs, or Heavy-Duty High-Frequency Response LVDTs.
Construction of LVDT
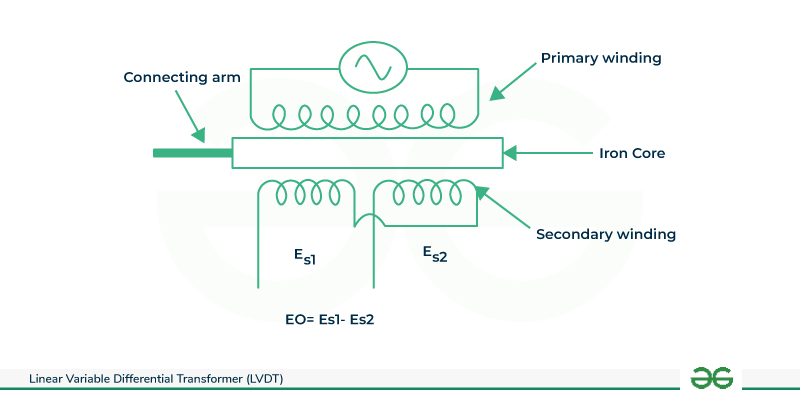
LVDT in the null position
The transformer and LVDT share a similar construction. It consists of one primary winding(P) and two secondary windings (S1 & S2). The primary and secondary windings are bounded by a hollow cylinder, known as the former. The primary winding is at the center and the secondary windings are present on both sides of the primary winding at an equal distance from the center. Both the secondary windings have an equal no. of terms and they are linked with each other in series opposition, i.e. they are wounded in opposite directions, but are connected in series with each other.
The entire coil assembly remains stationary during distance measurement. The moving part of the LVDT is an arm made of magnetic material.
Working Principle of LVDT
The working of LVDT is based on Faraday’s law of electromagnetic induction, which states that “the electrical power in the network induction circuit is proportional to the rate of change of magnetic flux in the circuit.”
As the primary winding of LVDT is connected to the AC power supply, The alternating magnetic field is produced in the primary winding, which results in the induced EMF of secondary windings.
Let’s assume that the induced voltages in the secondary windings S1 & S2 are E1 & E2 respectively. Now according tousing the rate of change of magnetic flux i.e. dΦ/dt is directly proportional to the magnitude of induced EMF i.e E1 and E2.
The total output voltage Eo in the circuit is given by Eo = E1-E2
Depending on the position of the core some cases arise:
Case 1: When The Core is Moving Towards S1
When the core of LVDT moves towards the second winding S1 then the flux linkage S will be more as compared to S2. The EMF induced in S1 will be more than the EMF of S2. Hence E1 is greater than E & net differential voltage Eo(E1-E2) will be +ve. The means output voltage Vo will be in phase with input AC voltage.
Case 2 : When the core is positioned at its null position
When the core is at a null position then the flux generated in both the secondary windings will be the same. The induced EMF E1 & E2, and both the windings will be the same. Hence the net differential output voltage Eo will be 0. It shows 0 displacement of the core.
Case 3 : When The Core Moving Towards S2
When the core of LVDT moves towards secondary winding S2 then the flux linkage with S2 will be more than S1. It means the EMF induced in S2 will be more than the induced EMF of S1
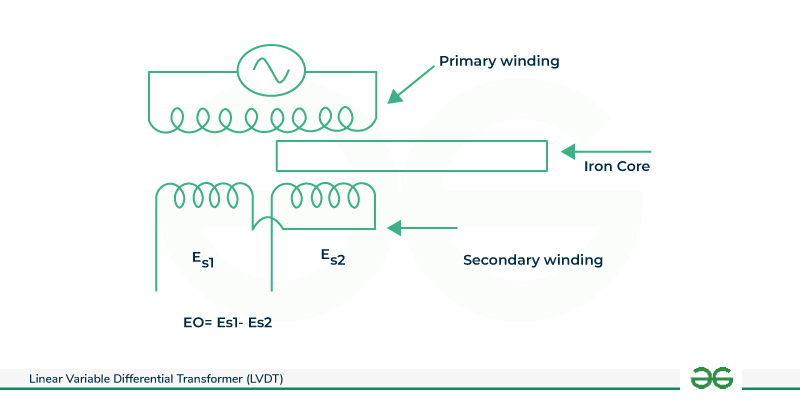
LVDT in displacement
Hence E2 is greater than E1 & net differential voltage Eo (E1-E2) will be negative. It means the output voltage will be out of phase input AC voltage.
Output of LVDT
- The output of a Linear Variable Differential Transformer (LVDT) is an AC voltage that is proportional to the displacement or position of its core.
- A zero-differential output voltage is produced when the core is in the center, or null position, where the induced voltages in the two secondary coils are equal. The induced voltages in the secondary coils become unequal as the core moves away from the null position, and the differential output voltage increases proportionately.
So in a nutshell we can conclude that the output of an LVDT is an AC voltage and the magnitude and other measurements of this output voltage provide insightful information about the direction and amount of displacement which is later inspected and fixed if any problem is detected.
Uses of LVDT
Linear Variable Differential Transformers (LVDT) are mainly used for work or motion or movement in many industries and research, they are also used in medicine and patient monitoring similarly in many applications because of its ability of unique features and advantages. It offers high precision and accuracy as it has non-coated sensors it can also vary with measurement ranges like the miniature or subminiature LVDTs are suitable for applications with extremely limited space or where fine-scale displacement measurements are necessary. its versatile nature, Long term stability, and reliability are what make it useful and make it a preferred choice for displacement and position sensing in numerous applications.
Characteristics of LVDT
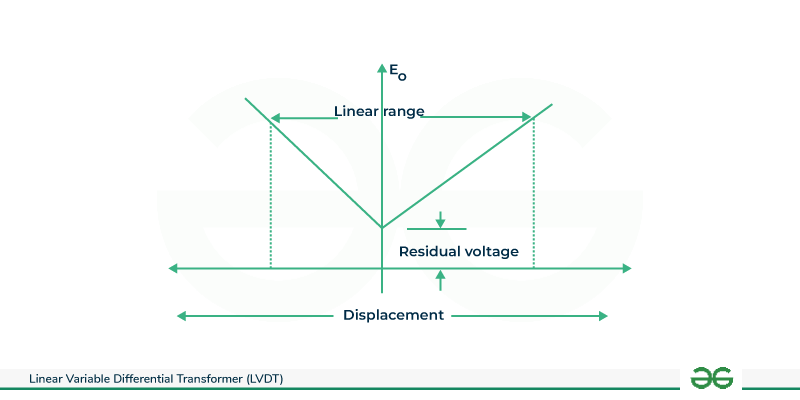
Show the displacement vs output voltage graph for movement in the right and left direction
Display the displacement versus output voltage graph for both left and right movement and how the output voltage varies with linear displacement.
The LVDT is an electromechanical device that generates an AC voltage output in direct proportion to the ferromagnetic core and relative displacement of the transformer. The ability of LVDT sensors to function in harsh environments with high levels of vibration and shock is a crucial feature.
LVDT Specifications
As we can understand the Linear Variable Differential Transformer’s (LVDT) specifications can change based on the model and the requirements of the application. some common specifications of the LVDTs are:
- Linearity
- Sensitivity
- Resolution
- Electrical Output
- Temperature Range etc.
Advantages and Disadvantages of LVDT
Given Below are the Advantages and Disadvantages of LVDT:
Advantages of LVDT
- High output: For minute variations in the magnetic core position, LVDTs provide a high output.
- Low hysteresis: LVDTs are highly repeatable due to their extremely low hysteresis.
- Low electrical noise: Because LVDTs have sensing coils with low impedance, they can produce extremely low electrical noise levels.
- Less power Consumption: LVDT’s consume less power as compared to other Transducer’s
Disadvantages of LVDT
- Since LVDT is an inductive transducer it is sensitive to the stray magnetic field, hence an extra setup is required to protect from stray magnetic field.
- As LVDT is an electromagnetic device, it is also affected by vibrations and temperature.
Applications of LVDT
- It is mostly used in industries in the field of Automation, Aircraft, Turbines, Satellite, Hydraulics etc.
- LVDT is used to measure physical quantity such as force, tension, pressure weight, etc. here LVDT is used as a secondary transducer.
- LVDT plays important role in geotechnical Instrumentations, as it is used for Monitoring Ground Movements, Landslides and Structural Stability
- LVDT plays an important role in the marine and offshore industry by Monitoring the Movements and Positions of ships and Underwater Structures.
- LVDT Plays an important role in Power Generation as it monitors the Critical Components in turbines and generators.
Conclusion
So… in a nutshell, we can conclude that the Linear Variable Differential Transformer (LVDT) is a positional transducer that is widely used for many industrial as well as scientific applications. The model of LVDT is similar to the transformer. It is very precise and stable. The LVDT is more heavy-duty and strong because of its solid and simple design, which removes many possibilities of physical contact between the coils and core. The LVDT is very useful for applications that require accurate position sensing because of its highly linear and sensitive nature despite having a very simple structure. When all things are taken into account, the LVDT is a good option for industries like manufacturing, automotive, and aerospace where precise measurements are essential for flawless control and operation and LVDTs are highly repeatable due to their extremely low hysteresis etc benefits are there.
Solved Examples on LVDT
1. An AC LVDT (Linear Variable Differential Transformer) is characterized by the following parameters: Input = 6.3 V, Output = 3.2 V, and a range of ±0.5 inches. Determine the following:
- Calculate the output voltage concerning core position for a core movement ranging from 0.45 inches to -0.30 inches.
- Find the output voltage when the core is positioned at -0.25 inches from the center.
Given that a 0.5-inch core displacement results in an output voltage of 3.2 V, a 0.45-inch core movement can be calculated as (0.45 * 3.2) / 0.5 = 2.88 V. Similarly, for a -0.30-inch core movement, the output voltage is determined as (-0.30 * -3.2) / (-0.5) = -1.92 V.
To find the output voltage for a -0.25-inch core movement, the calculation is (-0.25 * -3.2) / (-0.5) = -1.6 V.
FAQs of LVDT
1. How it is used for monitoring cracks?
The Linear Variable Differential Transformer (LVDT) sensors, can be used in the monitoring of cracks, for instance, in historical caverns in Israel by Hatzor et al .
2. Can LVDT be programmed?
Linear Variable Differential Transformers (LVDTs) are analog sensors that produce an output voltage based on the linear displacement of their core. Unlike digital devices, LVDTs themselves are not programmable in the traditional sense. They don’t have embedded processors or memory that allows for user programming.
3. Can an LVDT be used in environments with high levels of vibration and electromagnetic interference (EMI)?
Yes, LVDTs are often chosen for applications in harsh environments with high levels of vibration and EMI.
Share your thoughts in the comments
Please Login to comment...