In the electronics industry, we often need to deal with measuring certain quantities with precision and accuracy. One such quantity is temperature. There are different methods that can be used for measuring temperature depending on the operation range, sensitivity, frequency response, ruggedness, and other electrical parameters. In this article we will study what is an RTD, and how it works. We will also study the characteristics of an RTD.
In addition to that, we will study the advantages and disadvantages of an RTD. To study the real-life use of RTDs, we will study the applications of an RTD. In the end, some solved examples and some practice questions are provided for a better understanding of concepts. The article concludes with a summary in the end and some frequently asked questions.
What is an RTD?
An RTD or resistance thermometer stands for resistance temperature detector that is used for measuring the change in temperature by measuring the variation in resistance over the temperature range. It can be described as a temperature transducer that converts heat energy into some other form of energy.
Resistance temperature detectors are usually detectors of wire resistance temperature that are made up of platinum, nickel, or resistance wire elements. The flexibility of choosing their configuration and shape makes them an easy-to-use device. It shows good linear characteristics over a range of temperatures which makes it predictable and useful. There are some other transducers as well like a thermocouple or a thermistor. Each can be used depending on the need.
Construction of Resistance Temperature Detector
The construction of RTD involves wrapping the resistance wire on mica base. The wire is wrapped in a way to minimize the inductance between each turn of the coil. The whole coil is encased by a stainless steel case in order to protect the wiring. The ending of the wire terminate into leads
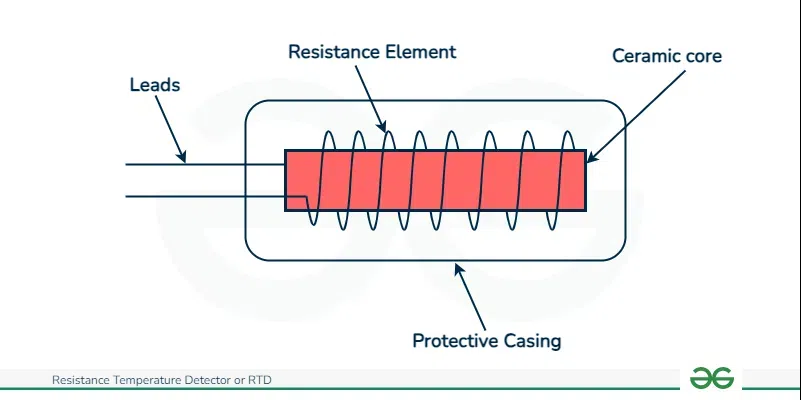
RTD construction
Usually the material that are employed to make RTDs should have positive temperature coefficient meaning their resistance should rise with increase in temperature. This means that metals that show linear characteristics should be used some of these materials are Copper, Nickel and Platinum.
Working of an RTD
Let us understand how an RTD works.
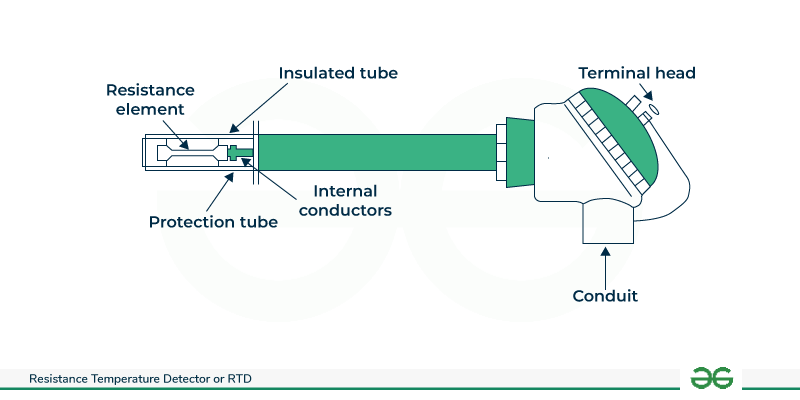
Diagram of an RTD
As we can see that RTD consist of a resistance elements which is fragile and therefore needs a protection which is done by providing insulation as shown by the protection tube. The insulated tube is connected to the element. Usually a metal alloy is used as protective tube because of its chemically inert behaviour.
The temperature begins from 00 C and can vary up-to the temperature range where metal shows linear change in characteristics. This range is dependant on the type of metal or resistance element being used like the range is till 6500C for platinum and can be around 3000C for nickel.
The linear characteristic of resistive element now comes into picture and the temperature coefficient of resistance can be given by
α =(R100–R0)/ (1000C.R0)
R0: resistance of the sensor at temperature 00C R100: resistance of the sensor at temperature 1000 C
This is how we can predict the temperature of device by using the linear nature of resistance element. Note that the electric current through the RTD resistance must be kept sufficiently low and constant to avoid self-heating. and also the temperature coefficient will differ from metal to metal.
Signal Conditioning of RTD
Since RTDs are passive devices, there is some signal conditioning requirement of RTDs .Let us see the circuit diagram for the same.
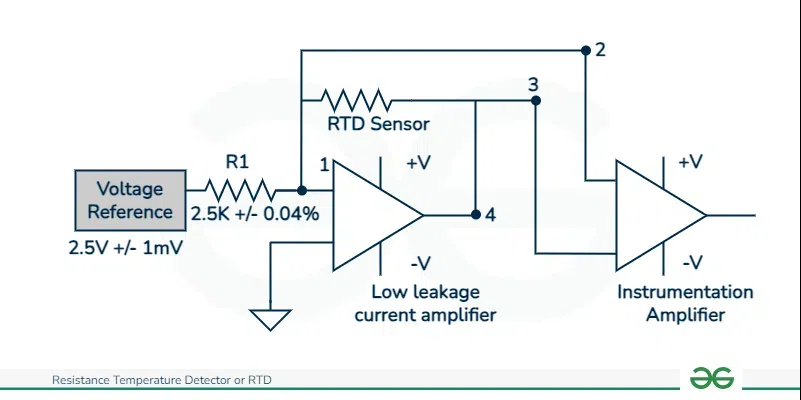
Circuit for signal conditioning
RTDs require a current excitation source. This is necessary so that RTDs can measure voltage across the device. It is important that the current given is stable and in required range. Another important thing is linearization of the output. We know that the output of RTDs is not completely linear over all temperature ranges therefore it is necessary to perform linearization using some hardware like ground and a trigger system or maybe a software.
Another important thing for Signal Conditioning is wire configuration. RTDs can be used in 2, 3, and 4 wire configurations and before installing RTDs one must ensure a compatible system that can support the RTD. Above circuit is a sample configuration that performs signal conditioning of RTD sensor.
Mathematical Equations
It is known that RTD shows linear behaviour over a large range of temperature . The linear relation between resistance and temperature can be shown by
RT=R0[1+α(t-t0) +β(t-t0)2+…………….]
RT : resistance values at t0C temperature
R0: resistance values at t00C temperature.
α and β are the constants depends on the metals.
For small range of temperature, we can simplify the above expression as
RT=R0[1+α(t-t0)]
From this nature it is evident that resistance of resistance thermometers at a temperature t varies linearly from original temperature at t0 C.
Expressions for a Three Wires RTD Circuit
RTD can be combined with a circuit which helps to calculate voltage drop across RTD. In 3 wire configuration, two wires connect the sensor element to a device like voltmeter on one side of the sensory element, and one connects it to the other side. Note that the all the wires should be made up of same material.
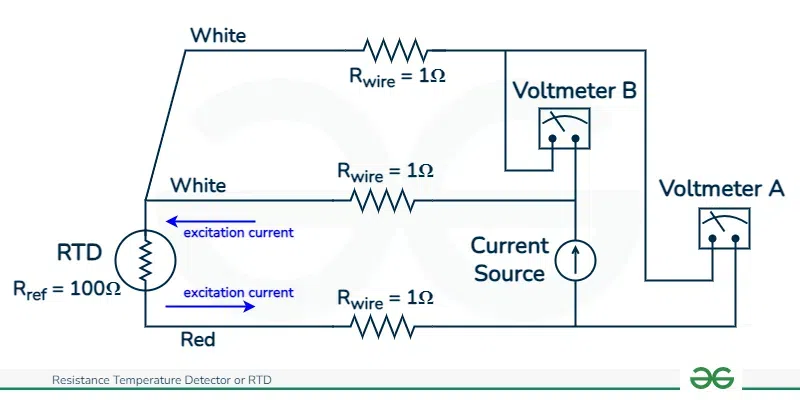
Three wires RTD
Three lead wires L1, L2, and L3. Here note that there will be individual resistances of the wires and different voltages across corresponding resistances.
R1 R2 R3 : Resistances of the three wires
V1 V2 V3 : Voltages measured across the corresponding resistances
E: Excitation voltage
The voltage is then measured across R1 and R2. The voltage drop in the lead wires is compensated by the use of the third wire. Therefore ,we can write the voltage as
VRTD = Vmeter(A) − Vmeter(B)
Graph of Behaviour of RTD
Let us now study how will the graph of various metals that make RTD look like when draw. Here we will plot a graph with resistance on y axis and temperature on x axis for metals like Copper, Nickel and Platinum. This graph is called resistance-temperature characteristics graph.
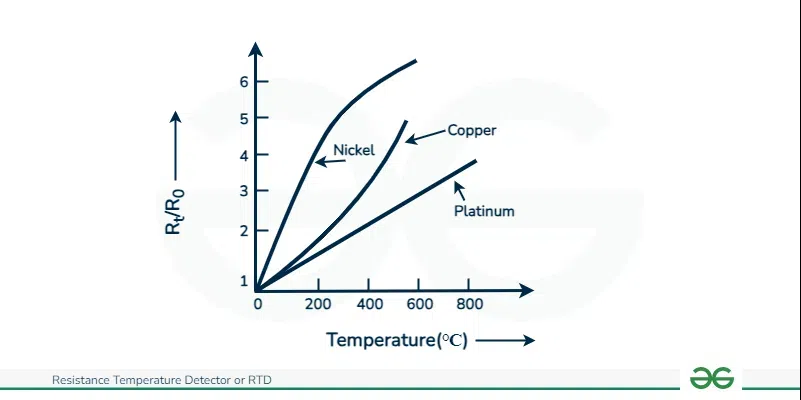
Resistance-temperature characteristics
From the above graph, we can see that platinum has a range that goes till 6500C whereas the range for copper is 1200C and nickel is 3000C. We can derive at the result after calculating some slopes of the graph that for every degree change in temperature (in Celsius) , the resistance of platinum shows and increase of 0.4 ohm. It is also important to notice that the shape of graph will change depending on the metal as it will change the value of constant α in equation ( α is metal-dependant).
This is how we can assess the linear nature of various metals that make an RTD over a range of temperature.
Characteristics of an RTD
Let us now see some of the characteristics of an RTD
- Intrinsic Accuracy: Out of the all three transducers, thermistor, thermocouple and RTDs, the resistance temperature detectors have the highest accuracy for temperature prediction which makes them the best choice.
- Linear Nature: RTDs have a good linear characteristics over a large range of temperature. This means that they follow a general linear equation and therefore their graph can be plotted easily predicting the future resistance values.
- Different Shapes: RTDs come in various shapes and sizes . This means we are free to choose their configurations depending on our need. They can be shielded or open units for both immersion and surface applications.
- Passive Device: an RTD is a passive device meaning it doesn’t produce an output on its own. In order to measure the current an external supply of current is required to be passed through it which inflicts a temperature change and then measurement can be made.
- Stable: It has great stability due to small drift. It is stable over a range of 260-8500C.
Advantages of an RTD
Let us now some advantages of RTDs
- Resistance temperature detectors have high intrinsic accuracy. This means that their electric resistance varies predictably in a range of temperature eliminating any cause of potential error. For example Pt used in RTDs is known for its stable and repeatable characteristics.
- It is known that the metals used in RTDs show linear nature i.e. the variation in their resistance values follows a linear curve with respect to the temperature values. This is useful for predicting any future values.
- Due to high accuracy, RTDs are suitable for precise measurements. It means that the values predicted by RTDs are almost very closely related giving precise results.
- RTDs can be made in any configuration which makes it easier to design an RTD . There is no rule on the shape of RTDs or whether they should be shielded or not.
- They also provide the feature of temperature averaging which is not seen in case of thermocouples and thermistor.
Disadvantages of an RTD
Let us now some disadvantages of RTDs
- One major disadvantage of RTDS is their long response time. Response time is how quickly can a device respond to the given input or stimuli and RTDs have longer response time as compared to thermocouple.
- Another disadvantage of RTDs is they are expensive. Due to the features it offers its cost is generally high as compared to thermistor and thermocouple which increases average cost of purchase.
- They can often cause self-heating in-case current value exceeds slightly than the limit. The resistance is measured by passing current through the wire therefore it can cause heating in the wire.
- The overall temperature range in which RTDs work is often small . Quantitively the range is around 260-8500C which is less as compared to the range over which other devices work.
- RTDs have low sensitivity meaning that they can’t detect small changes very well but thermocouples can do so. Due to low sensitivity, point sensing is not possible inn case of RTDs.
Applications of an RTD
Let us now some applications of RTDs
- Automotive industry uses RTDs largely for measuring the temperature change in case of engines and oil level sensors to ensure accurate functioning of these devices.
- Food processing industry uses RTDs for the purpose of temperature change in various food processing devices like containers and instruments.
- RTDs also find their application in electronics industry where they are used for sensing the temperature range of various amplifiers, transistors and stabilizers to ensure that they don’t exceed the limit and burn-out.
- RTDs are also used in medical industry where it is used in medical surgical devices for measuring temperature of heated surgical trays to ensure accurate temperature is set.
- Other places that use RTDs are power electronics industry, computer industry, consumer electronics, food handling industry and even military and aerospace.
Conclusion
We have seen how resistance temperature detectors are an important kind of transducers that can help to predict the temperature variation by simply measuring resistance change .This is mainly possible because of their linear nature which makes predicting temperature over a large range possible with such high accuracy. We have also seen that although RTDs have various benefits yet there are some characteristics where other transducers work better than RTDs like in case where more sensitivity devices are needed. Discussing all this has helped us analyse what are the situations where it is best to choose RTDs for temperature measuring purpose an what are the situations where we need to search for an alternate. Some Frequently Asked Questions have been answered for readers and it is suggested that they go through them for better understanding.
FAQs on Resistance Temperature Detector
What are other temperature measurement devices?
Some other devices that can be used for measurement of temperature indirectly are thermocouple which measures temperature by converting it to voltage and thermistor which measures temperature by showing non-linear variation.
What is the temperature range in which RTD gives accurate results?
RTDs have a small range where they give accurate results. This range is 260-8500C
What are some materials that are used to makes RTDs?
Some of the metals that make up RTDs are platinum, nickel and copper. Materials that make up RTDs must be conductive and must show linear change in resistance with temperature which is seen in case of these metals.
Share your thoughts in the comments
Please Login to comment...