DC motor is a machine that converts electrical energy of direct current into mechanical energy. In a DC motor, the input electrical energy is direct current which is converted into mechanical rotation.
In this article, we will learn what is DC motor, its Diagram, Construction, Working, types, and applications. We will also compare DC and AC Motors based on various parameters.
What is DC Motor?
DC Motor is an electrical machine which, when provided with direct current electrical energy, converts it into mechanical energy. It is based on electromagnetic induction, where a conductor carrying current (normally a coil of wire) placed in a magnetic field experiences force to rotate. This rotation is used to perform mechanical work.
There are many applications for DC motors, they can be used in robotics; electric vehicles, and some industrial machinery as well as household devices. DC motor can be used at such places where speed control is required. That is why DC motors are often used in trolleys, electric train production systems, elevators, etc.
DC Motor Definition
DC motor, also known as a direct current motor, is an electric motor that converts mechanical energy from the electrical energy of direct current.
DC Motor Diagram
Diagram of Direct Current Motor is shown below:
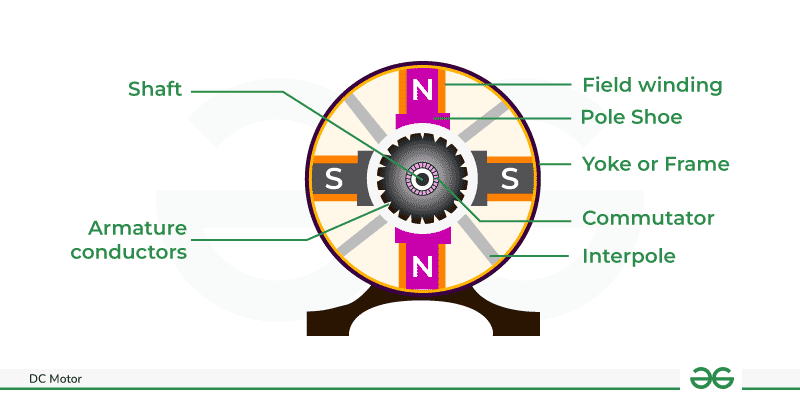
Construction of DC Motor
DC motor has such basic components, as a stator (stationary part of the element producing magnetic field) and a rotor part that rotates carrying winding or coil. When a DC voltage is connected to the coil, current flows through it and generates an electromagnetic field. When the magnetic field of this rotor interacts with that produced by the stator, a torque is induced which causes this piece to start spinning.
DC Motor Parts
DC achine has the following main parts:
- Field System or Stator
- Armature
- Commutator
- Brushes
Field Coil or Stator
As the name suggests, the field coil or stator is the non moving or the stationary part of the DC motor around which coil is wounded and produce magnetic field
The stator consists of various parts:
- Yoke
- Pole Core
- Pole Body
- Shoe for the pole
- Field Winding
- End Plates
Yoke: The structure of a DC machine works to create the magnetic circuit between the poles.
Pole Core: Pole Core is usually of laminated iron or other magnetic material. Its function is to serve as a passage for the magnetic flux generated by the field winding.
Pole Body: Pole body works with the pole core. When an electric current passes through the field winding, a magnetic flux is established not only in the pole core but also around it. The poles and their bearings are known as the pole body.
Shoe: Shoe is a synonym for one of the brushes inside an electric motor. DC motors have brushes to make contact with the rotating armature, and typically they are sodded.
Field Winding: Field winding is on the pole core next to the stator. Field winding uses insulated copper wire. An insulated copper coil is wound round the pole core. If this coil on the pole core is excited with direct current, we get magnetic flux.
End Plates: End plates encapsulate the entire motor. They provide a casing for all of the internal parts–the armature, commutator and brushes as well sometimes also including field windings
Armature
Armature is the rotating part of the motor which generates mechanical energy. Armature core has windings. The armature core is made of 0.3 to 0.5 mm thick high magnetic strength (silicon steel lamination) and a thin layer of varnish is applied on each sheet.
Commutator
Commutators are used in DC appliances such as DC Motors and DC Generators. It periodically reverses the current between the armature and the circuit and produces steady torque
Brushes
Brushes or often called Carbon Brushes are made up of graphite. In DC Motors, brushes supplies current to the winding of the armature.
DC Motor Working Principle
When a current carrying conductor is placed in a magnetic field, a mechanical force acts on it, which can be determined by Fleming’s left hand rule. Due to this force the conductor becomes mobile in the direction of the force.
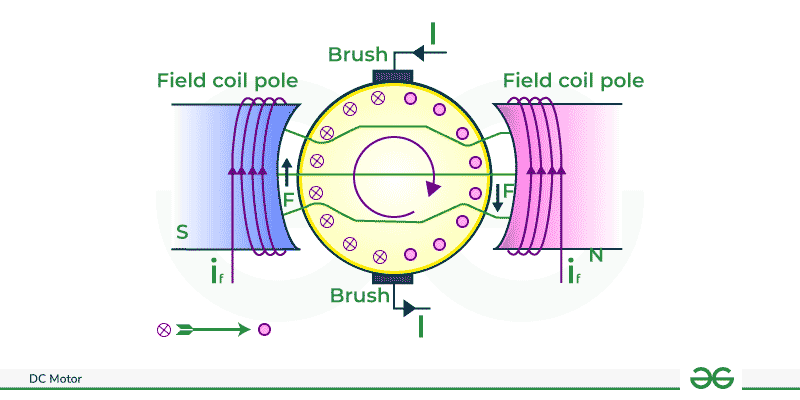
DC Motor Working
Imagine that a current-free conductor (which is not connected to the supply) is placed in the main magnetic field the and without the magnetic field flowing through the conductor. Assume, there is an air gap from N pole to S pole.
Current is flowing in the conductor but the magnetic effect of N pole and S pole has been removed. In this situation the conductor will maintain its own magnetic field. The magnetic field lines of force of the conductor will be clockwise according to the cork screw rule.
Current is flowing in the conductor and main magnetic field is also present. The magnetic field produced due to the current in the conductor acts along with the main field above the conductor but opposes the main field below the conductor. The result is that flux accumulates in the region above the conductor and flux density reduces in the region below.
From this it is clear that when the force is acting on the conductor, it works to push the conductor downwards. If the direction of current in the conductor is changed, the flux will accumulate downwards and will try to move the conductor upwards.
DC Motor Characteristics
If length of conductor = L meter, field intensity = B weber per square meter (Bwb/m2) and current flowing in the conductor = i ampere, then the force experienced by the conductor will be F = iBL Newton.
F= B.L.I.Sinθ
where,
- B = flux density (in Tesla).
- L = length of conductor (in meters).
- I = current flowing in the conductor.
- Sinθ = angle between the conductor and magnetic lines of force.
DC Motor Torque Formula
Torque, also known as moment or moment of force, is the force that tends to rotate or move an object around a central axis. A force is a push or pull, similarly, torque creates twisting to an object. Mathematically, torque is given as T = F × r. For DC Motor, the torque is given as
T = (0.159PΦNZ/A)Ia
where,
- T is Torque of Armature
- Ia is the armature current
- P is Number of Poles
- Ф is Flux per pole
- N is Speed of motor in (RPM)
- Z is Number of conductors
- A is Number of parallel paths
DC Motor EMF Equation
EMF or the electromotive force is responsible for flow of current in the electrical appliances. EMF is not an force but the electric potential. In case of DC Motor, a back EMF is produced which counters the armature current. The direction of this back EMF is given by Lenz Law. The formula of back emf is given as
Eb = PΦNZ/60A
where,
- P is Number of Poles
- Ф is Flux per pole
- N is Speed of motor in (RPM)
- Z is Number of conductors
- A is Number of parallel paths
DC Motor Speed
The formula for DC Motor speed is given as:
N = KEb/Φ
where,
- N is speed in RPM
- K is constant proportionality which is equal to 60A/ZP
Types of DC Motors
DC Motors can be classified into various categories based on the application and winding connections. Based on the winding of armature DC Motor is of two types
- Self Excited DC Motors
- Separately Excited DC Motors
Self Excited DC Motor
DC motors that excite themselves have a part and coil of field connected in series or partly so, same for parallel connection. They can also have combination of series and Parallel connections. They also get power from only one place. Three types of self-excited DC motors exist:
- Series DC motor
- Shunt DC motor
- Compound DC Motor
Series DC Motor
It is a motor in which the field is in series with the armature and its starting torque is very high. This means that the same flow of current goes through both the coil and armature. Series motors always go in one direction and their speed is affected by the physical load.
Shunt DC Motor
Shunt motor is a DC motor in which the field is jointed in parallel to the armature and its starting torque is less than that of series motor. Inside the shunt motor the field winding is connected parallel to the armature winding. The field winding is made of more turns of thin wire. Shunt motors are used in applications where continuous speed is required.
Compound DC Motor
Compound Motor is a Motor in which both series and parallel fields are added. Compound DC motors use both parallel and connected field windings. In the armature winding, everything is in series. However, field coils can be shunt or series types.
Separately Excited DC Motor
In DC motors with a separate excite, field coil to make permanent magnets. But, the armature and field coils are not connected electrically to each other. They work separately and do not bother the other. But, the result of the engine is added up with both.
More Types of DC Motor
Some more types of DC Motor on the various parameters are discussed below:
1. Based on Commutation:
- Brushed Motors: Use brushes and a commutator for current reversal.
- Brushless Motors: Switch currents in the windings by electronic commutation.
2. Based on Application:
- DC Servo Motors: Exact control of position and speed. Applied in robotics, CNC machine tools and automation.
- Stepper Motors: Take small steps, accurate position control. Widely employed in printers and CNC machines.
- Hysteresis Motors: The materials ‘motion makes use of their magnetic hysteresis. Used in devices such as record players, rather simple.
- Brushed DC Gear Motors: Have a gearbox for high torque at low speeds. Applied in robotics, electric vehicles and automation.
- DC Traction Motors: Intended for use in traction devices, including electric vehicles and trains.
3. Based on Speed-Torque Characteristics:
- High-Speed DC Motors: Designed for uses involving high rotational speeds. Examples include tools and appliances.
- Low-Speed DC Motors: Offer high torque at low speeds. Commonly used in industrial machinery.
4. Based on Size and Shape:
- Micro DC Motors: Applications such as consumer electronics call for very small motors.
- Large DC Motors: As used in industrial purposes such as steel mills, paper industries and ship propulsion.
5. Based on Control System:
- Closed-Loop DC Motors: Feedback mechanisms can be employed for more precise control. Applications where precision control is important.
- Open-Loop DC Motors: Control without feedback, simpler design. In applications where control is not so critical.
Difference between DC Brushed Motor and DC Brushless Motor
The difference between DC Brushed Motor and DC Brushless Motor is given below:
DC Brushed Motor vs DC Brushless Motor
|
Comparison
|
DC Brushed Motor
|
DC Brushless Motor
|
Construction
|
Consists of a stator and rotor with windings. Uses brushes and a commutator to switch current.
|
Consists of a stator with permanent or electromagnetic magnets and rotor windings. Electronic commutation is achieved without the use of brushes and commutators.
|
Maintenance
|
Requires frequent maintenance because of brush and commutator wear.Brushes may have to be changed and commutators need cleaning.
|
Generally requires less maintenance because no brushes or commutators to wear out
|
Lifespan
|
Typically runs out faster due to the wear and tear in brushes, commutators.
|
It usually has a longer life since there are no brushes and commutators to wear off.
|
Efficiency
|
May have reduced efficiency due to friction and wear in brushes, commutators.
|
Usually, more effective since there are no brush-related losses.
|
Noise and Vibration
|
May generate additional noise and vibration resulting from physical interaction of brushes with the commutator.
|
Generally less noisy and smoother in operation.
|
Cost
|
Generally less expensive upfront.
|
Normally costlier as they require electronic controllers.
|
AC and DC Motors
AC and DC Motors are two types of motors based on the input of the type of current. As the name suggests AC Motor uses AC Current produce mechanical energy while DC Motor produces mechanical energy from Direct Current
Difference Between AC And DC Motor
The difference between AC and DC Motor are discussed below:
AC Motor vs DC Motor
|
AC Motor
|
DC Motor
|
AC motor runs on alternating current.
|
DC motors operate on direct current.
|
There is no need for conversion of current in AC motors. Like AC.
|
There is no need for conversion of current in AC motors. Like AC.
|
AC motors are used where power performance is demanded for extended periods of time.
|
DC motors are used where the speed of the motor needs to be controlled externally.
|
AC motors can be single-phase or three-phase.
|
All DC motors are single phase.
|
In an AC motor the armature does not rotate while the magnetic field keeps rotating continuously.
|
In a DC motor, the armature rotates while the magnetic field rotates.
|
Repairing AC motors is not expensive.
|
DC motors are very expensive to repair.
|
Brushes are not used in AC motor.
|
Brushes are used in DC motor.
|
AC motors have a very long life span
|
DC motors do not have a very long life span.
|
The speed of AC motors can be controlled by simply changing the frequency of the current.
|
The speed of DC motors can be controlled by changing the current of the armature winding.
|
Application of DC Motor
‘DC motor’ is used to refer to any rotary electrical machine that converts direct current electrical energy into mechanical energy. DC motors can vary in size and power, ranging from small motors in toys and appliances to large mechanisms that power vehicles.
DC motor is used at the following places.
- DC motor is used in traction work, machine tools, industry, elevators etc.
- DC motors have the widest variation in speed (compared to other motors).
- DC series motor has very high starting torque and is commonly used to start high inertia loads such as trains, elevators or hoists.
- Shunt DC Motors are used in drilling machines, centrifugal machines etc.
Also, Check
Direct Current Motor FAQs
What is a DC Motor?
DC motor is an electrical machine that transforms direct-current (DC) electricity into motion
How does a DC Motor Function?
DC motors work on the principle of electromagnetic induction, using magnetic fields and current to achieve rotation.
How many Types of DC motor?
There are basically DC motor two types of DC Motor namely, self excited DC Motor and separately excited DC Motors
What is DC Seies Motor Application?
DC series motor produces, high torque and hence are used in cranes, locomotives, conveyors etc.
What is Application of DC Shunt Motors?
DC Shunt motors provide constant speed and hence are used in centrifugal machines, drilling machines etc.
What is Working Principle of Brushless DC Motors?
Brushless Motors don’t use carbon brushes. They work on the principle of Lorentz Force
What is the Role of Commutator in a DC Motor?
The commutator in the DC motor is responsible for controlling terminal which provides current to armature coil. It maintains rotation by altering where magnetic field interacts.
What is the Function of Brushes in a brushed DC motor?
In a brushed DC motor, brushes are used to transfer the electrical current between fixed and moving parts.
Share your thoughts in the comments
Please Login to comment...