An electric motor that operates at a constant speed is known as a synchronous motor as the frequency of the AC voltage that is used and the rotor rotation are synchronized. The fixed connection between the stator and rotor magnetic fields is maintained by it. Imagine a world free of electricity, where every job is carried out by hand. Let us imagine for a moment a device that both is simple and moves in time with the electrical beat: a synchronous motor.
A Synchronous motor is fundamentally a fascinating electrical device that synchronizes with the rise and fall of electric currents. It synchronizes its rotation with the frequency of the alternating current, like a partner in dance following each step, forming a smooth transition between the electrical world and the physical world we live in. Its synchronous dance style separates it from its asynchronous equivalents, offering an accurate symphony in performance.
Imagine your daily ritual, the soft sound of your blender, and the grinding sound of your coffee grinder. The appealing mechanisms of synchronous motors, which silently power these appliances with a precision similar to a well-choreographed dance, are hidden behind these accepted sounds. Synchronous motors, in contrast to their asynchronous counterparts, are able to keep a firm hold on time, which enables them to rotate in perfect sync with electrical beats for dependable and efficient efficiency.
What is a Synchronous Motor?
Synchronous motor is a type of AC motor. A rotating machine that transforms electrical energy into mechanical energy using an AC source is known as an AC motor. Two varieties of AC motors exist:
- Synchronous motor
- Asynchronous motor(induction motor)
Synchronous motors are AC motors that spin at synchronous speed. A flexible rotor and a fixed stator make up a synchronous motor. Synchronous motors, like induction motors, use stator technology to produce a rotating magnetic field (RMF).
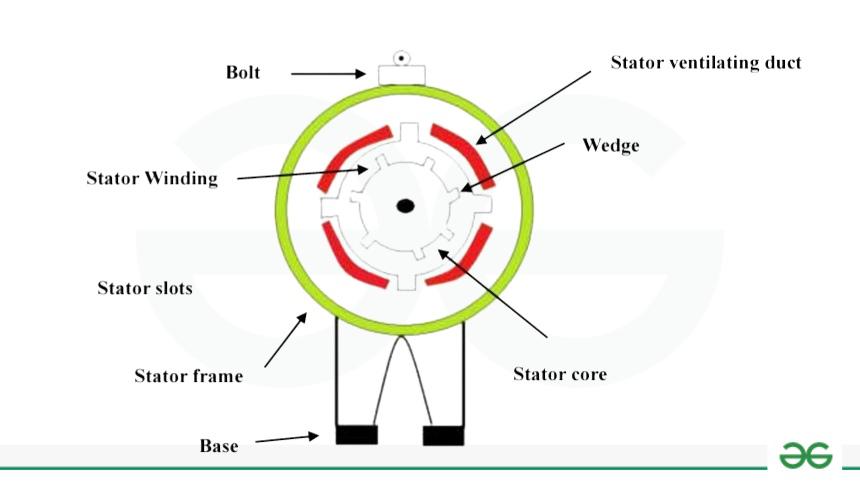
Synchronous Motor
A DC supply powers the rotor’s permanent-magnetic coils for synchronous motors. When an AC source delivers power to the stator, it generates a rotating magnetic field, or RMF. The rotor’s poles are polarity-different. Due to their differing polarities, the rotor magnetic field and stator RMF lock when they interact, causing the rotor to begin rotating at a synchronous speed while the RMF continues to move at a synchronous speed. Thus, they are also known as constant speed motors or synchronous motors.
The foundation of synchronous motors is the magnetic interlocking principle. Synchronous motors are started in the same way as induction motors, with the stator receiving an initial three-phase AC supply. A DC source is supplied to the rotor if the machine has reached its maximum speed, which is 90% of its speed.
When the armature winding is connected to a three-phase source, the armature generates a rotating magnetic field that rotates at a synchronous speed of 120 f/P. In order to attract the opposite pole of the rotating magnetic poles, we must first excite the permanent poles of the field winding produced by the DC source. The rotor will continue to rotate at synchronous speed if the magnetic poles are drawn to one another and locked.
Synchronous speed =[Tex]\frac{120f}{p}
[/Tex]
Where , f= frequency
and p = no. of poles
Construction of Synchronous Motor
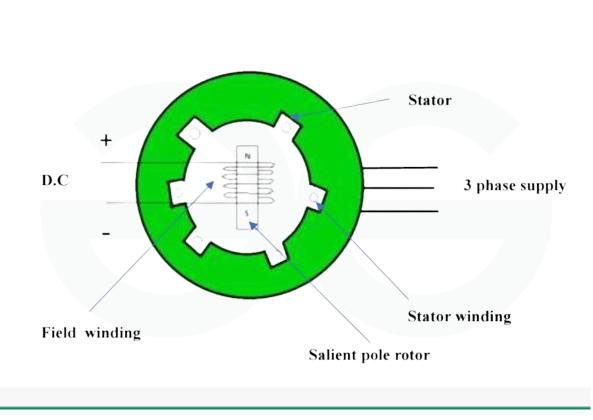
Construction of Synchronous Motor
Stator
The stationary portion of a Synchronous Motors is called the stator. It is composed of a coated iron sheet core that minimizes eddy current losses. Usually consisting of three phases, distributed windings are fitted into holes on the stator. These windings produce a revolving magnetic field as they are connected to an AC power source.
Rotor
Salient Pole Rotor: This kind of rotor features outward-extending poles that resemble prominent poles. The magnetic field is concentrated at these poles.
These salient poles are surrounded by the rotor windings, which are linked to one another by a metallic core.
Some industrial applications and hydroelectric generators frequently use salient pole rotors.
Non-Salient Pole Rotor: Alternatively, this kind of rotor has a smooth, cylindrical shape and no projecting poles.
The rotor’s windings are distributed uniformly around its circumference. On-salient pole rotors are robust and simple, and they are frequently found in turbo-generators.
Salient and non-salient rotors both function by rotating inside the magnetic field of the stator. The synchronous speed of the rotor is determined by the frequency of the AC power source and the number of poles in the stator winding. Synchronization is required for synchronous motors to operate well in a range of surroundings, such as industrial machinery and power generation.
Main Features of Synchronous Motor
Some interesting features that set synchronous motors apart are as follows:
- Synced motors function similarly to flawless dancers. They are precisely in time with the electricity they receive, rotating at a steady speed. It is comparable to having a partner in dance who never skips a step.
- The stator, a fixed component, functions similarly to a powerhouse. It produces a magnetic field, which rotates the rotor. Imagine it like an orchestra conducted by a conductor.
- The rotor is the moving component. It comes in two varieties: one with salient poles, or standout poles, and the other without (non-salient pole). Every kind has a distinct style, much like various dance steps.
- AC power is ideal for synchronous motors. With the alternating current (AC) in your house, they function flawlessly. It seems like their all-time favorite song is quietly playing.
- The timing of these motors is crucial. They rotate at a precise speed in accordance with the electrical frequency. It resembles a musician playing with impeccable timing.
- Synchronous motors are useful in factories and power plants alike. They are the go-to performers in many applications because they always bring their A game to the table.
Principle of Operations of Synchronous Motor
Synchronous Motors operates on the basis of a continuous and synchronized rotation generated by the interaction of the stator and rotor.
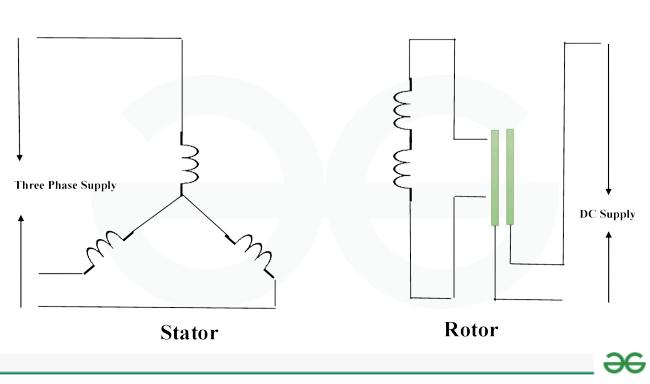
Operation of synchronous motor
- Magnetic field of the state: The stator is linked to an AC power source. When AC power is applied, the stator’s internal rotating magnetic field (RMF) is created.
- Interaction of Rotors: This revolving magnetic field covers the motor’s moving component, the rotor. Depending on the type of motor, the rotor may have smooth cylindrical shape or salient poles (significant poles). The rotor experiences an electromagnetic force due to the stator’s magnetic field.
- Synchronization: Because of the electromagnetic force, the rotor tries to follow the magnetic field’s rotation. Synchronous speed is necessary for synchronous motors to function effectively.
- Constant Rotation: After reaching synchronous speed, the rotor continues to rotate continuously to maintain the stator’s changing magnetic field.
- Output Power: The rotor produces mechanical power during rotation, which can be used for various purposes like electricity generation and device powering.
Methods of Starting of Synchronous Motor
Synchronous motors do not start themselves by nature. As a result, it needs an additional starting method. A synchronous motor can be started using one of the two methods below:
- Using an external prime mover first
- Initially, damper windings
Synchronous Motor Starting with an External Prime Mover
- This method involves driving the synchronous motor with a third-party motor.
- After the synchronous motor has been brought to synchronous speed by the external motor, it is synchronized with the AC supply to function as a synchronous generator. Next, the outside motor, also known as the prime mover, is disconnected. The synchronous machine functions as an engine once it is synchronized.
- At this point, the synchronous motor’s shaft can be attached to the mechanical load. Since the load has been removed from the synchronous motor prior to synchronization, the prime mover motor only has to get past the momentum of the synchronous motor in absence of a load. Therefore, the rating of the starting motor or prime mover is substantially lower than that of the synchronous motor.
Synchronous Motor Starting with Damper Windings
- The most common method to start a synchronous motor is with damper windings. A damper winding is composed of heavy copper bars that fit into slots cut into the rotor’s pole faces. This configuration of copper bars and end rings creates a squirrel cage winding because those copper bars are subsequently short-circuited by end rings at the two ends of the rotor. The synchronous motor with damper winding will initially operate as a three-phase squirrel lock induction motor when its armature is linked to a three-phase supply.
- The DC field excitation is applied to the rotor field windings when the motor reaches a speed that is closer to the synchronous speed. After that, the motor runs at synchronous speed as the rotor follows the magnetic field of the frame as it rotates.
Applications of Synchronous Motor
Synchronous motors are used in many different applications because of their special qualities and accurate control. The following are a few typical uses for synchronous motors:
- Electric generators often utilize synchronous motors in power plants to convert mechanical energy into electrical energy.
- Synchronous motors are used in many industrial machinery because of their efficiency and capacity to operate at constant speeds.
- Synchronous motors are often utilized to power pumps in chemical processing facilities, where the production procedure requires a constant speed.
- As synchronous motors operate at a constant speed; they are a reliable and efficient choice for large-scale air conditioning systems.
- Synchronous motors are used in communication networks to synchronize timing mechanisms, among other uses for them.
Bringing Synchronous Motors Up to Speed
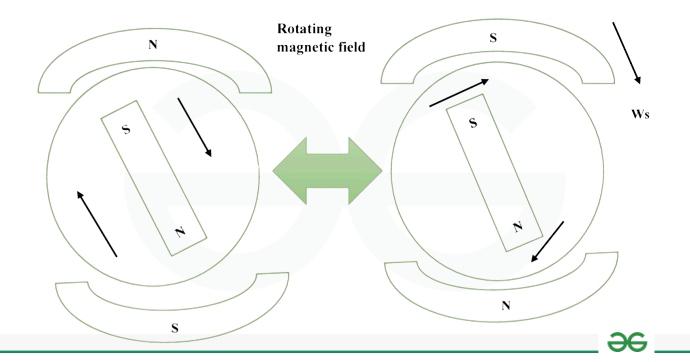
Bringing synchronous motor upto speed
Synchronous motors must be carefully started to rotate in time with the alternating current in order to reach their maximum speed. There are several techniques used, including auto-transformer starting, direct online starting, and the use of soft starters. In order to prevent sudden inrush current during startup, the motor’s voltage and frequency are adjusted to accelerate gradually.
For smoother acceleration, specialized methods such as damper windings or pole amplitude modulation may be employed. When the motor reaches synchronous speed, it locks into the rotating magnetic field, which makes energy conversion more effective. The size of the motor, the intended use, and the requirement to reduce electrical and mechanical stress during acceleration all influence the starting technique selection.
3- Phase Synchronous Motor
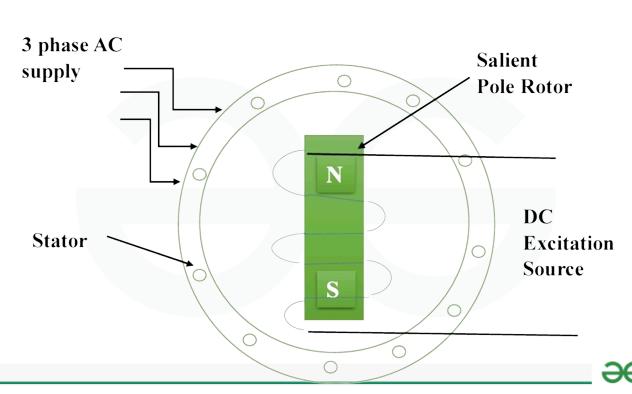
3-phase synchronous motor
Synchronous motors with three phases are strong and widely used in various environments. They are made up of rotor and stator that are both driven by three-phase AC power. The stator produces a magnetic field that rotates in a circular motion, which the rotor coordinates with. These motors are appropriate for applications needing accurate and stable performance because they provide precise speed control and maintain a constant speed.
Three-phase synchronous motors, whether they have non-salient pole or salient pole rotors, are widely used in automation, industrial machinery, and power generation. Their effectiveness, dependability, and capacity to function in tandem with the AC power grid render them indispensable in a wide range of electromechanical systems, facilitating the seamless operation of numerous industrial operations.
Types of Synchronous Motors
The way in which the rotor is excited is a common basis for categorizing different types of synchronous motors. Direct current (DC) excited synchronous motors and non-excited synchronous motors are the two most common types
Non-Excited Synchronous Motor: – Also referred to as a hysteresis motor or a reluctance motor. Unlike a DC field winding, the rotor lacks a separate excitation source. Often used in low-power applications and scenarios where simplicity is valued.
Depends on the magnetic resistance of the rotor material to follow the rotating magnetic field produced by the stator.
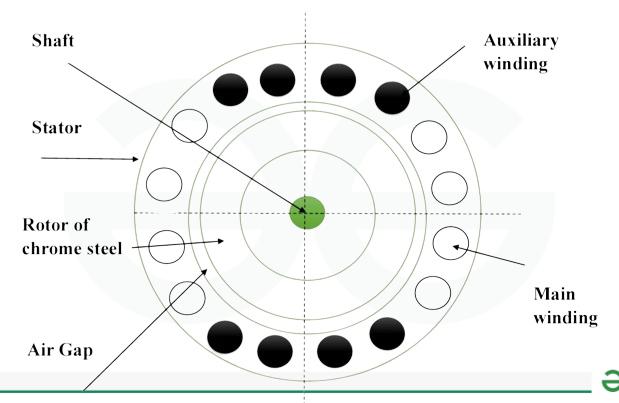
Non excited synchronous motor
Direct Current Excited Synchronous Motor: The rotor of this kind of Synchronous Motors has a DC field winding process. The rotor is excited by a separate DC power source, creating a magnetic field that works with the stator’s rotating magnetic field. DC excitation enables accurate management of the motor’s operation, including power factor and speed. Frequently utilized in medium- to large-scale power applications—like power plants and industrial processes—where increased control and efficiency are essential.
Difference Between Synchronous Motor and Induction Motor
Synchronous Motor | Induction Motor |
---|
Operates on the principle of synchronism , the rotor rotates at the same speed as the RMF of stator.
| Operates on the principle of electromagnetic induction , the rotor is not synchronized with the stator.
|
Construction is complex.
| Construction is simpler.
|
It requires separate DC source for rotor excitation.
| It does not require separate DC source as it uses induced e.m.f
|
It is less costly compared to induction motor .
| It is costlier than synchronous motor.
|
It is capable of being made with a leading power factor.
| It usually has a lagging power factor.
|
Speed can’t be controlled.
| Speed may be controlled.
|
Advantages and Disadvantages of Using Synchronous Motors
Given Below Are some of the Advantages and Disadvantages of Using Synchronous Motors :
Advantages of using synchronous Motors
- Synchronous motor provide constant speed helping in steady and accurate speed performances.
- Synchronous motors often have high efficiency levels, which lowers operating costs and saves energy.
- By adjusting the excitation, synchronous motors can be made to achieve a leading power factor.
- These motors have less torque ripple and run more smoothly, reducing the mechanical vibrations for steady and quiet operation.
- Synchronous motors are used in various industries for the production of electrical power and industrial machinery.
Disadvantages of Synchronous Motors
- Compared to induction motors, synchronous motors can be more difficult to start.
- Compared to induction motors, synchronous motors typically have a higher initial cost.
- Synchronized motors can become sensitive to sudden changes in load.
- DC-excited synchronous motors require additional maintenance for their excitation system and DC field winding.
- Synchronous motors are less appropriate for applications requiring high torque.
Conclusion
In conclusion, the synchronous motor is a strong electric device that works on the unusual principle that the rotation of the stator’s magnetic field and the motion of the rotor are synchronized. Because of its accuracy in sustaining a constant speed, it is perfect for applications needing precise synchronization, like synchronous clocks and power factor correction systems. There are several types of synchronous motors, each designed to meet specific industrial requirements.
Among its advantages are its leading power factor and suitability for applications requiring constant speed; on the other hand, two known drawbacks are the complexity of construction and the need for external starting mechanisms. The synchronous motor is still an essential part of many industries where accuracy and efficiency are critical, in spite of its drawbacks.
Synchronous Motors – FAQs
A synchronous motor can’t produce its maximum torque when it starts operating normally. How come?
- There may be a low exciter voltage.
- The field shaft could be upside-down.
- There may be an open circuit or a short circuit in the field.
Why is an induction motor referred to as a rotating transformer?
The rotor acquires power in the same way as a two-winding transformer. This is why an induction motor is also called a rotating transformer at times.
Can single-phase power systems employ synchronous motors?
Synchronous motors are usually designed for three-phase power systems. Although they exist, single-phase synchronous motors are less common and have lesser uses.
Share your thoughts in the comments
Please Login to comment...