SAP MM – Introduction, Components and Features
Last Updated :
15 Dec, 2023
One of the main components of the SAP ERP (Enterprise Resource Planning) system is SAP MM (Materials Management). It is essential to the management of an organization’s inventory and buying procedures. From the point of acquisition to the point of consumption, SAP MM helps companies optimize their material and logistics management procedures, guaranteeing effective and economical handling of items.
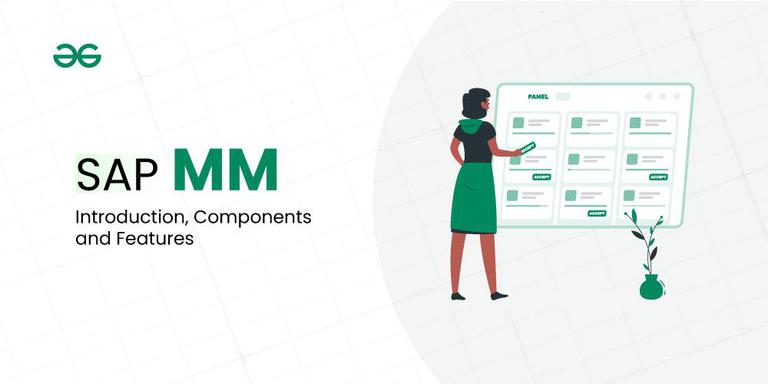
SAP MM – Introduction, Components and Features
What does SAP MM stand for?
SAP MM stands for “Materials Management.” SAP MM (Materials Management) is a SAP ERP Central Component (ECC) module that allows businesses to manage materials, inventory, and warehouses.
What is SAP MM?
SAP MM, which stands for Materials Management, is a critical module within the SAP ERP (Enterprise Resource Planning) system. Its primary focus is on managing an organization’s procurement processes and the logistics of the supply chain. SAP MM is designed to streamline and optimize the management of materials, ensuring that businesses can effectively plan, procure, store, track, and consume goods.
Master Data Components in SAP MM:
Master data in SAP MM is crucial information that is shared across the organization and used in various business processes. It forms the foundation for transactional data in procurement and materials management. The key master data components in SAP MM include:
1. Material Master: The Material Master is a central repository that contains detailed information about all materials a company procures, produces, stores, and sells.
Key Data Fields:
- Basic Data: Includes material type, industry sector, material group, and classification.
- Sales Data: Contains information relevant to sales processes, such as sales organization and distribution channel.
- Purchasing Data: Includes data related to procurement, like the material group, purchasing organization, and preferred vendor.
- Plant Data: Provides details about the material’s storage location, unit of measure, and valuation class.
- Warehouse Management Data: Includes storage type and storage section data for materials managed in a warehouse.
2. Vendor Master: The Vendor Master contains information about the suppliers or vendors from whom the organization procures materials or services.
Key Data Fields:
- General Data: Includes vendor name, address, communication details, and terms of payment.
- Company Code Data: Contains data specific to the company code, such as reconciliation account and payment methods.
- Purchasing Data: Provides details about the vendor’s currency, delivery conditions, and order currency.
- Accounting Data: Includes information related to the vendor’s account, such as tax information and payment terms.
3. Info Record: The Info Record (Information Record) links a material and vendor, storing information related to their procurement relationship.
Key Data Fields:
- Material-Specific Data: Includes details about the material, such as the order unit, purchase info record category, and minimum order quantity.
- Vendor-Specific Data: Contains vendor-specific information like vendor material number and vendor-specific order unit.
- Pricing Conditions: Includes details about pricing, such as standard prices, conditions, and scales.
4. Source List: The Source List specifies the sources of supply for a material, indicating which vendors are approved for procurement.
Key Data Fields:
- Vendor: Identifies the approved vendors for a specific material.
- Plant: Specifies the plant or location for which the source list is valid.
- Status: Indicates the procurement status, such as active or inactive.
5. Purchase Info Record: The Purchase Info Record combines information from the material master, vendor master, and source list, providing a comprehensive view for procurement.
Key Data Fields:
- Material Data: Includes material-specific information from the material master.
- Vendor Data: Contains vendor-specific information from the vendor master.
- Source List Data: Provides information from the source list for the specified material and vendor.
Features of SAP MM (Materials Management):
SAP MM is a comprehensive module that encompasses various features to facilitate efficient procurement, inventory management, and materials handling within an organization. Here are key features of SAP MM:
1. Procurement Processes:
- Purchase Requisition (PR): Allows users to initiate the procurement process by creating requests for materials or services.
- Request for Quotation (RFQ): Enables the organization to invite quotations from potential suppliers.
- Purchase Order (PO): Facilitates the creation of purchase orders detailing the terms, conditions, and quantities for materials or services.
2. Inventory Management:
- Goods Receipt (GR): Records the receipt of materials into inventory, updating stock levels.
- Goods Issue (GI): Documents the removal of materials from inventory for various purposes like production or consumption.
3. Invoice Verification:
- Three-Way Match: Validates invoices against purchase orders and goods receipts to ensure accuracy before processing payments.
- Vendor Invoice Management (VIM): An extension for automating and streamlining the accounts payable process.
4. Master Data Management:
- Material Master: Central repository containing comprehensive information about materials, including purchasing, sales, and inventory details.
- Vendor Master: Stores information about suppliers and vendors, facilitating efficient procurement.
5. Logistics Execution:
- Warehouse Management (WM): Integrates with SAP WM for advanced warehouse handling and optimization.
- Handling Unit Management (HUM): Manages packaging materials and their tracking during logistics processes.
6. Integration with Other SAP Modules:
- Integration with SAP SD (Sales and Distribution): Ensures seamless coordination between procurement and sales processes.
- Integration with SAP PP (Production Planning): Facilitates planning and execution of production processes.
7. Reporting and Analytics:
- SAP Analytics: Provides a range of reporting tools and analytics for monitoring and analyzing procurement, inventory, and materials data in real-time.
8. User Interface and Accessibility:
- SAP Fiori: Introduces a modern and intuitive user interface for better user experience and accessibility.
Conclusion:
In conclusion, SAP MM provides a robust set of features that cover the entire materials management lifecycle, from procurement to inventory management. These features contribute to the efficiency, transparency, and control of an organization’s materials and procurement processes.
Share your thoughts in the comments
Please Login to comment...