The primary errand of a motor starter is to start as well as stop the motor to which it is united. Starters, like relays, are electromechanical switches designed specifically to protect the motor from overload. The starter gives the supply to the motor manually or automatically as well as protects the motor from faults or overload. It based on the types of motors, the motor starters are available in various sizes with different ratings in the market. This article discusses 3 point starter which is used in business as well as industrial applications.
What is a Three-Point Starter?
An electrical device known as a three-point starter is used to start and maintain the speed of a DC shunt motor. The connection of resistance in this circuit is in series which decreases the initial high current and protects the equipment against any electrical failures. Here, the event of back e.m.f plays an essential part in operating the motor. This EMF extends when the motor’s armature begins to rotate in the magnetic field by acting against the voltage supply.
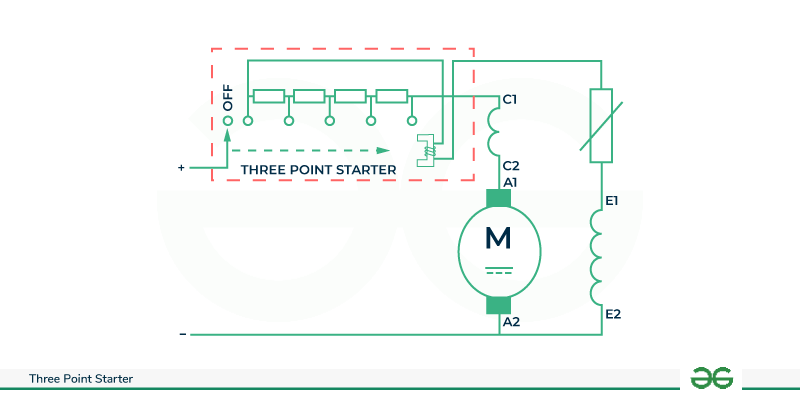
Three Point Starter
A 3-point starter helps to start and run DC shunt or compound wound DC motors.
Now let’s discuss why these type of DC motors require the starter in the first place?
Well, it is because there is back EMF (Eb), which plays a critical role in governing the operation of the motor. The back emf creates as the motor armature begins to rotate in presence of the magnetic field, by generating action and counters the supply voltage. Consequently the back emf at the starting of the motor is zero, but it develops continuously as the motor gathers speed.
The general motor emf equation is:
E = Eb + Ia Ra
Where
E=Supply Voltage
Eb=Back EMF
Ia=Armature Current
Ra=Armature Resistance
E = Ia since Eb = 0,
Then
E = Ia.Ra.
Subsequently we can modify for the armature current Ia
Ia = E / Ra
We can see from the above equation that the current will be dangerously high at starting (as the armature resistance Ra is small) this end we really must used a device like the 3 point starter toward limit the starting current to acceptably low value.
Construction of 3 Point Starter
Construction wise a starter is a variable resistance, integrated into the number of sections as shown in the figure close to. These sections’ contact points, designated OFF, 1, 2, 3, 4, 5, and RUN, are referred to as studs. Apart from these, there are three primary points, commonly known as
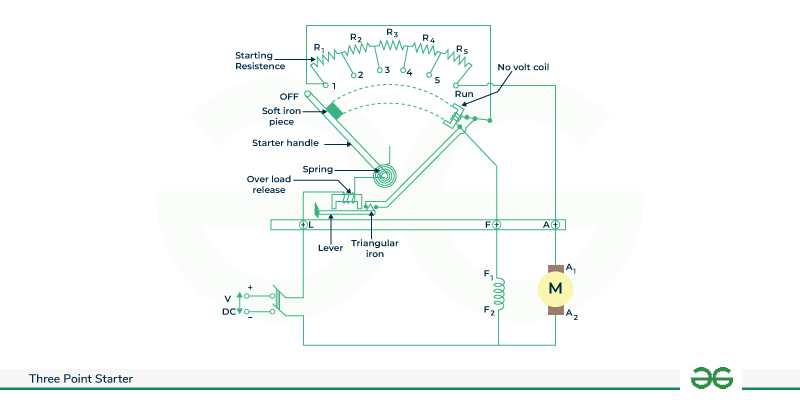
Construction of 3 Point Starter
- ‘L’ Line terminal (Connected with positive of supply)
- ‘A’ Armature terminal (Connected with the armature winding)
- ‘F’ Field terminal (Connected with the field winding)
From that point it gets the name 3 point starter. Now discuss on the construction of 3 point starter in further details that the point ‘L’ is connected with an electromagnet called over-load release (OLR) as shown in the figure. The other end of OLR is connected with the lower end of conducting lever of starter handle where spring is also attached with it, and the starter handle additionally contains a soft iron piece housed on it. This handle is allowed to move to the opposite side RUN against the force of the spring. This spring carries ease the handle to its unique OFF position affected by its own force. Another parallel path is gotten from the stud ‘1’, given to another electromagnet called No Volt Coil (NVC) which is additionally associated with terminal ‘F.’ The starting resistance at starting is completely in series with the armature. The OLR and NVC go about as the two protecting devices of the starter.
Working of Three Point Starter
In above we discussed about construction, let us now discuss into the working of the 3 point starter. Initially, the handle is set to the OFF position when the power is supplied to the DC motor. Then handle is gradually moved against the spring force to connect with stud No. 1. As of now, field winding of the shunt or the compound motor helps supply through the parallel path given to starting resistance, through No Voltage Coil. whereas the entire initial resistance is connected to the armature in series. The high starting armature current subsequently gets limited as the current equation at this stage becomes:
Ia = E /(Ra + Rst )
The handle continues to make contact with studs 2, 3, 4, and so on as it moves further.. thus gradually cutting the series resistance from the armature circuit as the motor gathers speed. When the starter handle is in ‘RUN’ position, the entire resistance is eliminated, and the motor runs with normal speed.
This is because back emf is developed thus with speed to counter the supply voltage and reduce the armature current.
So the external electrical resistance isn’t needed any longer and is removed for ideal operation. The handle is manually shifted from the OFF to the RUN position as the speed increases. Now the question is once the handle is taken to the RUN position the way things should remain there, as long as the motor is running.
To find the answer to this question let us look the working of No Voltage Coil.
Functions of No-volt Release
At the point when the motor reaches at the normal speed and the arm is reached at the ON position, the entire starting resistance is cut off from the circuit. Now in running condition, assuming that the supply is interrupted or disconnected, the starting arm remains at the ON position. Additionally, the armature winding is connected directly across the primary supply when the supply is restored, so there is no back EMF in the circuit.
Hence, in this condition, an excessive amount of current starts flowing through the armature winding and it might harm. Thus, to stay away from this situation no-volt release is used in a circuit to pull back the arm to the OFF position.
The no-release coil consists of an electromagnet that is connected in series with the shunt field winding. At the point when the supply is ON, it attracts the soft iron keeper. In any case if supply fails or intruded on, the electromagnet is demagnetized and releases a soft iron keeper. Because of the spiral force of the spring, the arm is pulled back to the OFF position and disconnects the main supply.
Additionally, the shunt field winding open-circuit prevention function of no-volt release is an additional function. Since the no-volt discharge is associated in series with the shunt field winding. Assuming that the shunt field winding is open-circuited, the current flowing through the no-volt release is zero. Additionally, it releases the coil to the OFF position and demagnetizes the coil.
Functions of Over-load Release
To prevent overloading, a second overload release device is connected in series to the motor. The overload release receives the same amount of current as the motor because this device is connected in series with it.
A coil is what makes up the overload release. In normal conditions, the current flows through this coil are insufficient for the pull armature in a upward direction. In any case, in an over-load condition, an excess amount of current will flow through the motor and coil of over-load release. Furthermore, this high measure of current is sufficient to pull the armature in a upward direction.
In this way, as the armature is pulled up, it short-circuited the no-volt release and resulted to demagnetize the no-volt discharge coil. In this way, the soft iron keeper separated from the no-volt release, and the arm is pulled back to the OFF position. Consequently, in over-load conditions, the motor will detach from the supply with the help of over-load release.
Uses of Arc
We know that arc provides supply to the NVC and field winding. Also, without an arc, we can supply current by directly connecting across the first resistance i.e., to the terminal-1, as shown by a dotted line. Be that as it may, when the handle is moved to the ON position. The whole resistance which is connected in the armature circuit during starting will comes under the field circuit. This increase in field resistance will influence its performance.
This problem can be overcome by the use of an arc made up of brass or copper. It allows the direct linking of the field circuit to the power source without any impact from starter resistances. The arc maintains continuous contact with the handle whenever it is moved from the OFF position.
Comparison between 3-Point Starter and 4-Point Starter
FEATURES
|
3-POINT STARTER
|
4-POINT STARTER
|
Terminals
|
It has three terminals they are supply, armature, and field
|
It has four terminals they are supply, armature, and two field
|
Cost
|
It is low cost
|
It is high cost compared to 3-point starter
|
Starting Torque
|
It has less starting torque
|
It has high starting torque
|
Durability
|
It has a less durable compared to four point starter
|
It has a high durable
|
Size
|
Smaller in size
|
Larger in size
|
Power Factor
|
It provides the low power factor
|
It provides the high power factor
|
Applications
|
It is used in compound and shunt motor
|
It is compatible with a motor that offers adjustable speed
|
Advantages of 3-Point Starter
- A 3-point starter is used with DC shunt motors.
- The three-point starter aids in motor speed control.
- This starter can be also used in machine processing plants and spinning factories.
- It reduces the high starting current.
- A three-point starter protects the motor from short-circuits and over-load issues.
Disadvantages of 3-Point Starter
- The primary disadvantage of 3 point starter motor is, that it is a huge variation of speed by adjustment of the field rheostat.
- This starter isn’t suitable for variable-speed motors.
- While increasing the high resistance from accomplish a high speed, the field current will always be extremely low.
- Large field current adjustments are not suitable with 3-point starters.
- The holding electromagnet will not have the option to persevere through the power of the spring on the off chance that the field current is generally low.
- At a low field current, the NVC fails to keep the handle in the ON position, which would disconnect the motor from the supply.
- This magnet can disengage the H handle from the power source and delivery its arm by means of the typical engine capability.
- The 4-point starter can therefore be utilized when there is no associated volt trip coil in the parallel field.
- The field winding doesn’t have additional opposition in series, so speed regulation isn’t possibilities.
- Because there is no additional resistance to protect against faults, the condition circuit may become damaged.
Applications of 3-Point Starter
A 3-point starter is a type of starter that’s commonly used to control DC motors. It’s mainly used in situations where precise control over motor speed and torque is necessary. Given Below Are Some Applications of 3-Point Starter.
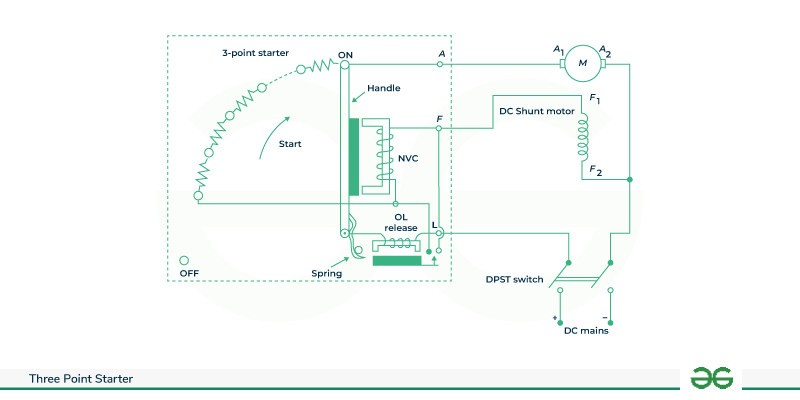
3 Point Starter Connected to DC Shunt Motor
- DC Motor Control: Three-point Starter are used by many machinery, such as rolling mills, lifts, cranes, and conveyor belts, to control speed and Torque of DC motors.
- Machine Tools: In machine tools like lathes machines and milling machines, three point Starter Plays important Role to ensures that these tools operate at the desired levels and produce accurate results.
- Electric Traction: Electric trains, trams, and even some electric cars using DC motors uses Three-point starters to efficient control speed and torque regulation. These starters contribute to the performance and overall control of the motors.
- Welding Machines: The use of 3-point starters in welding machines is highly advantageous. They help regulate the welding current, ensuring stable and controlled operation of the DC motors. This leads to better welding outcomes.
- Hoists and Cranes: Hoists and cranes rely on 3-point starters to effectively control lifting and lowering speeds. Furthermore, these starters help in managing the torque during heavy loads, ensuring safe and effective operation.
- Escalators and lifts: In lifts and elevators powered by DC motors, 3-point starters become possibly the most important factor. They provide the necessary control and regulation of speed, ensuring smooth acceleration and deceleration for an comfortable ride.
- Textile Industry: DC motors are commonly used in various textile machinery, and 3-point starters are employed to precisely control speed in processes like spinning and weaving. These starters contribute to the overall efficiency and quality of textile production.
3-point starters and their widespread applications in controlling DC motors. Whether it’s industrial machinery, electric traction, welding machines, hoists and cranes, lifts and elevators, or the , these starters plays a vital role in maintain optimal performance and ensuring smooth operations.
Conclusion
The 3-point starter is a fundamental part in electrical designing, playing a vital role across a great many applications. It drives the pinion wheels of modern apparatus as well as impels electric trains forward. This starter’s viability in directing DC engines has established its persevering through pertinence in different areas, including assembling, transportation, and heavy-duty machinery.
The 3-point starter continues to hold its ground despite the availability of cutting-edge motor control technologies because of its simplicity, reliability, and cost-effective. Its clear yet exceptionally productive plan settles on it the favored decision in circumstances where exact control is of most extreme significance. Whether it’s in the controlled climate of an assembling plant or the consistently changing scene of electric foothold frameworks, the 3-point starter ensure ideal motor performance. This, thus, adds to the general effectiveness and usefulness of the systems it governs.
As businesses progress and innovation propels, the meaning of the 3-point starter stays in one piece. It shows that even despite advancement, certain fundamental parts stay indispensable to the smooth activity of intricate apparatus and systems.
FAQs on 3-Point Starter
1. What is a three-point starter?
3-point starter is used to control the speed and torque of DC motors. It comprises of three terminals connected with the armature, field winding, and external resistance.
2. Are 3-point starters still significant with the advent of advanced motor control technologies?
Yes, 3-guide starters stay pertinent due toward their effortlessness, unwavering quality, and cost-viability. While trend setting innovations like variable recurrence drives are acquiring notoriety, 3-guide starters go on toward be utilized in different applications where their characteristics are advantageous.
3. For what reason are 3-point starters preferred in certain applications?
3-point starters are liked in applications requiring exact command over DC motor performance. These are suitable for a wide range of industrial and commercial applications due to their ability to regulate speed, torque, and smooth acceleration.
4. How does a 3-point starter work?
The 3-point starter works by controlling the current flow to the armature of a DC motor. During startup and operation, it adjusts the circuit’s resistance to regulate the motor’s speed and torque.
5. Where are 3-point starters commonly used?
3-point starters are normally used in modern apparatus, electric traction systems, welding machines, lifts, cranes, hoists, and different manufacturing processes that use DC motors.
Share your thoughts in the comments
Please Login to comment...