Thermodynamic cycles are used to explain how heat engines, which convert heat into work, operate. A thermodynamic cycle is used to accomplish this. The application determines the kind of cycle that is employed in the engine. The thermodynamic cycle consists of a series of interrelated thermodynamic processes involving heat and works going in and out of the body, simultaneously changing pressure, temperature, and other changes in body state, and eventually returning to the initial state.
In this article, we will learn all about the Thermodynamics Cycles including various types of cycles such as Carnot, Rankin, Otto, Diesel, Brayton, Stirling, etc. Also, we will learn about the various processes happening during these cycles. So, let’s start our learning of Thermodynamics Cycles.
What is Thermodynamics Cycle?
A thermodynamic cycle is a series of thermodynamic actions that, when carried out repeatedly, leave the system in the same state as when it was first created. Thermodynamic cycles are used to explain how heat engines, which convert heat into work, operate. The thermodynamic cycle is a closed cycle that has many changes due to temperature, pressure, and volume, but whose end and initial states are equal. This cycle is important because it allows the piston in the engine to move continuously and the fluid working in the refrigerator to expand/compress. Without this cycle, the vehicle will not be able to continue running or the refrigerator will not be able to cool when restarted.
Types of Thermodynamic Cycles
There are various types of cycles in thermodynamics, and some of those important cycles are listed as follows:
- Carnot Cycle
- Rankine Cycle
- Otto Cycle
- Diesel Cycle
- Brayton Cycle
- Stirling Cycle
Now, let’s understand these cycles in detail.
Carnot Cycle
The French physicist Sadi Carnot proposed the imagined Carnot cycle in 1824. It is a thermodynamic cycle. Transforming heat into work or work into heat, is the most effective cycle that is currently known to exist. The Carnot cycle consists of four processes that can be reversed:
- Isothermal expansion: When a working substance (usually a gas) comes into thermal contact with a heated reservoir, it expands and takes heat from the reservoir with it.
- Adiabatic expansion: The functioning substance is thermally detached and extends, taking care of business with its environmental elements.
- Isothermal compression:Â The functioning substance is in warm contact with a chilly supply and packs, emitting intensity to the repository.
- Adiabatic compression:Â The functioning substance is thermally secluded and packed, taking care of business based on its environmental factors.
The Carnot cycle can be addressed on a temperature-entropy graph as a closed circle. The proficiency of the Carnot cycle is determined by the situation.
η = 1−TH/​TC
​​Where,
- TC is the temperature of the cool supply, andÂ
- TH is the temperature of the hot repository.
The Carnot cycle is an optimal cycle, and no genuine motor can accomplish its effectiveness. In any case, the Carnot cycle is a valuable hypothetical model that can be utilized to look at the proficiency of various motors.
The Carnot cycle is likewise significant in the field of refrigeration. A fridge works by retaining heat from a cold space and delivering it to a hot space. The Carnot cycle can be utilized to determine the greatest effectiveness of a cooler.
Here is a diagram of the Carnot cycle:
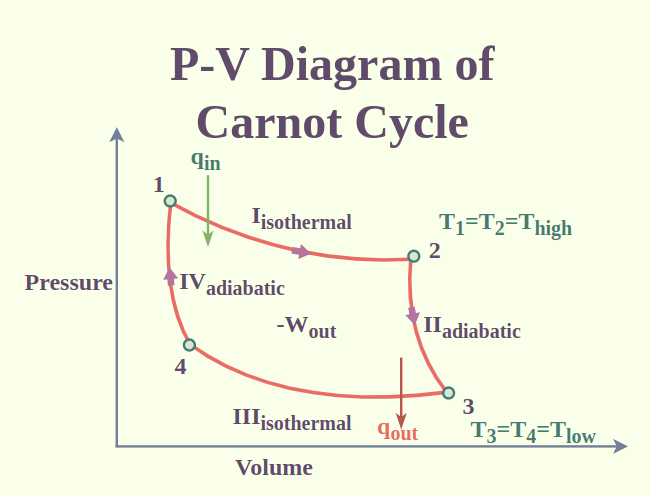
Â
The four processes are labeled as 1-2, 2-3, 3-4, and 4-1. The arrows indicate the direction of heat flow and work done.
An essential idea in thermodynamics is the Carnot cycle. As a helpful theoretical model for comprehending these appliances, it sets a maximum efficiency limit for heat engines and refrigerators.
Learn more about Carnot Engine
Rankine Cycle
A steam turbine’s method of converting heat into mechanical work is described by the Rankine cycle, a thermodynamic cycle. The cycle is named after Scottish engineer William John Macquorn Rankine, who created it in the middle of the 19th century.
The Rankine cycle has four steps, which are as follows:
Step 1: Isentropic compression.
Within a pump, the working fluid (water) is compressed from low pressure to high pressure. Since no heat is added to or lost from the fluid during this isentropic process.
Step 2: Heat addition.
The heated compressed water is next converted to steam by vaporization in a boiler. A combustion process, such as burning coal or natural gas, is usually used to generate heat.
Step 3: Isentropic expansion.
A turbine expands the steam, turning its thermal energy into mechanical work. Additionally, since no heat is added to or taken from the fluid, this process is isentropic.
Step 4: Condensation.
After that, a condenser converts the steam back into water. In this process, heat is released and often transmitted to a cooling medium like water or air.
The fundamental thermodynamic cycle used in all steam power plants is the Rankine cycle. Other applications, such as solar thermal power plants and geothermal power plants, also make use of it.
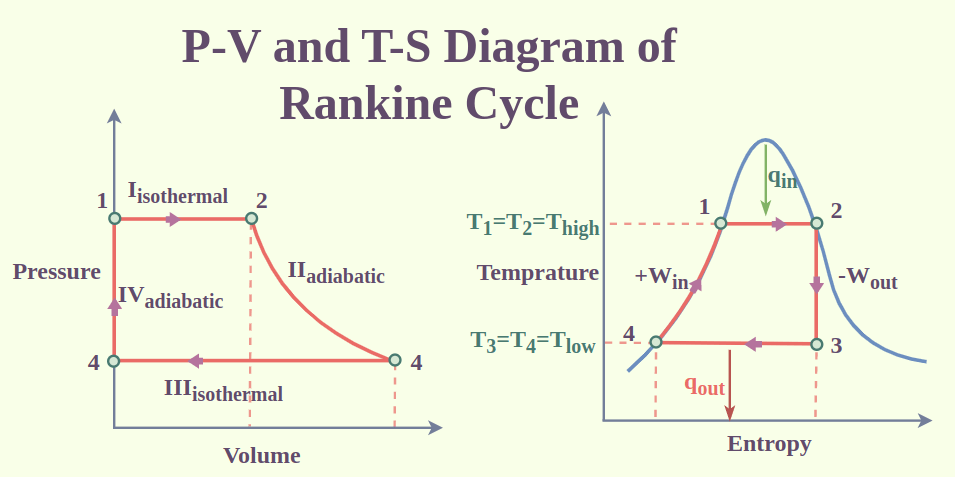
The Rankine cycle is a thermodynamically reversible cycle, which means that all of the heat input may be converted back into labour. Friction, heat transmission, and other variables cause losses in practice nevertheless. As a result, the Rankine cycle’s efficiency is normally between 30 and 40%.
The Rankine cycle is available in a variety of forms, including the supercritical, reheat, and regenerative cycles. Through a reduction in the quantity of heat rejected by the environment, these modifications aim to increase the cycle’s efficiency.
Otto Cycle
Nikolaus August Otto, who patented the first four-stroke internal combustion engine in 1876, is the inspiration for the Otto cycle. Many modern internal combustion engines still use the Otto cycle, however other cycles, such as the Atkinson cycle, are still used in some applications.
The Otto cycle is a simplified thermodynamic cycle that depicts how a common spark ignition piston engine works. It is the Highest frequent thermodynamic cycle seen in car engines. The Otto cycle is made up of four processes:
- Isentropic compression: In the cylinder, the piston compresses the air-fuel mixture. Because this is an isentropic process, no heat is transmitted to or from the system.
- Constant Volume Heat Addition: The air-fuel mixture is ignited by a spark, causing it to combust and expand. Because the expansion occurs at a steady rate, no work is done during this process.
- Isentropic Expansion:Â The expanding gases force the piston down, causing it to accomplish work on the environment. This is an additional isentropic process.
- Constant Volume Heat Rejection: The cylinder’s exhaust gases are evacuated, and the piston returns to the top of the cylinder. Because this is a constant-volume process, no work is done during this time.
The Otto cycle is an imagined cycle, although actual engines do not follow it exactly. The Otto cycle, on the other hand, is a valuable model for understanding how spark ignition engines work.
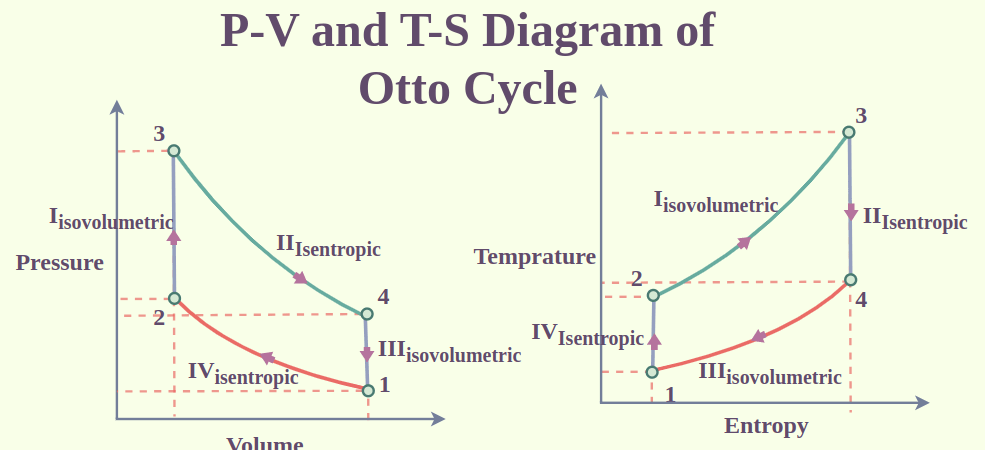
Â
The compression ratio, which is the ratio of the volume of the cylinder at the end of the intake stroke to the volume of the cylinder at the conclusion of the compression stroke, determines the Otto cycle’s efficiency. The cycle is more effective with a higher compression ratio.
Diesel Cycle
The operation of a diesel engine is described by the Diesel cycle, a thermodynamic cycle. It has a four-stroke cycle, which means that one cycle of operation requires the piston in the engine to make four strokes. There are four strokes:
- Intake Stroke:Â A vacuum is created as the piston descends in the cylinder, drawing in air.
- Compression Stroke: The air is compressed as the piston rises in the cylinder. Since a diesel engine normally has a higher compression ratio than a petrol engine, the air in the cylinder is compressed to a significantly higher pressure.
- Combustion Stroke: Injection of fuel into the cylinder occurs at the conclusion of the compression stroke. Fuel is ignited by the heat from the compressed air, which causes it to burn quickly. The piston is pushed downward by the expanding gases, producing power.
- Exhaust Stroke: Pushing the engine’s exhaust gases outside, the piston rises within the cylinder.
Compared to the Otto cycle, which is utilized in petrol engines, the Diesel cycle is more effective. This is so that the gasoline may ignite more readily and completely. A diesel engine’s increased compression ratio raises the temperature at the end of the compression stroke. Diesel engines are therefore more efficient than petrol engines.
Additionally, the Diesel cycle is stronger than the Otto cycle. This is due to the fact that a spark plug is not used to ignite the fuel in a diesel engine, thus there is no chance of a misfire if the spark plug breaks. As a result, diesel engines are frequently utilized in settings where dependability is crucial, such as heavy-duty vehicles and buses.
Here is a P-V and T-S diagram of the Diesel cycle:
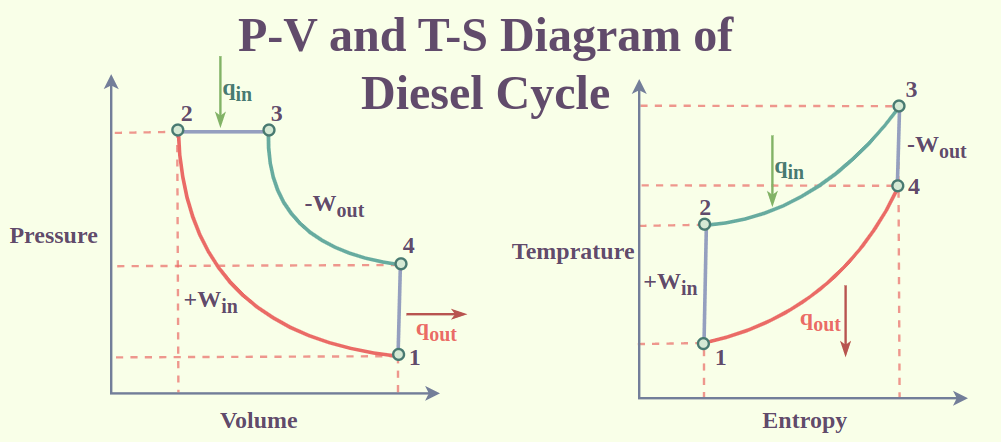
The Diesel cycle’s four strokes are identified by the numbers 1-2-3-4. The direction of the piston movement is shown by the arrows. The lines’ colors represent several thermodynamic processes:
- Isentropic Compression in Blue
- Red: Continuously Adding Heat
- Isentropic Growth in Yellow
- Green: Continuously Rejecting Heat.
Brayton Cycle
One type of heat engine that uses air or another gas as its working fluid operates according to a thermodynamic cycle called the Brayton cycle. Modern gas turbine engines and air-breathing jet engines also follow the Brayton cycle; however, the original Brayton engine had a piston compressor and piston expander.
The Carnot efficiency, which is determined by the following equation, is what determines the Brayton cycle’s efficiency:
η = 1 – TC / TH
Where,
- η is the Brayton cycle’s effectiveness.
- TC is the cold reservoir temperature
- TH is the hot reservoir temperature
Here are some more specifics on the four steps of the Brayton cycle:
Step 1: Without any heat transmission, the working fluid is compressed during an isentropic compression process. This is an unrealistic method that cannot be carried out in real life. However, by making the compression process as isentropic as feasible, the Brayton cycle’s effectiveness can be increased.
Step 2: In a process called constant pressure heat addition, the working fluid is heated at a fixed pressure. Typically, this is accomplished by burning fuel with the help of air. The working fluid receives heat from combustion, which raises its temperature and pressure.
Step 3: Isentropic expansion is a process in which no heat is transferred and the working fluid expands. This is an unrealistic method that cannot be carried out in real life. Making the expansion process as isentropic as possible, however, can boost the Brayton cycle’s effectiveness.
Step 4: In a process called constant pressure heat rejection, the working fluid is cooled at a fixed pressure. Most frequently, a heat exchanger is used to do this. The environment’s temperature and pressure decrease as a result of the working fluid’s heat being transferred to it.
Heat may be converted into work very effectively using the Brayton cycle. However, the heated reservoir’s temperature has a limit on the cycle’s efficiency. In reality, the materials used to build the engine have a limit on how hot the hot reservoir can go.
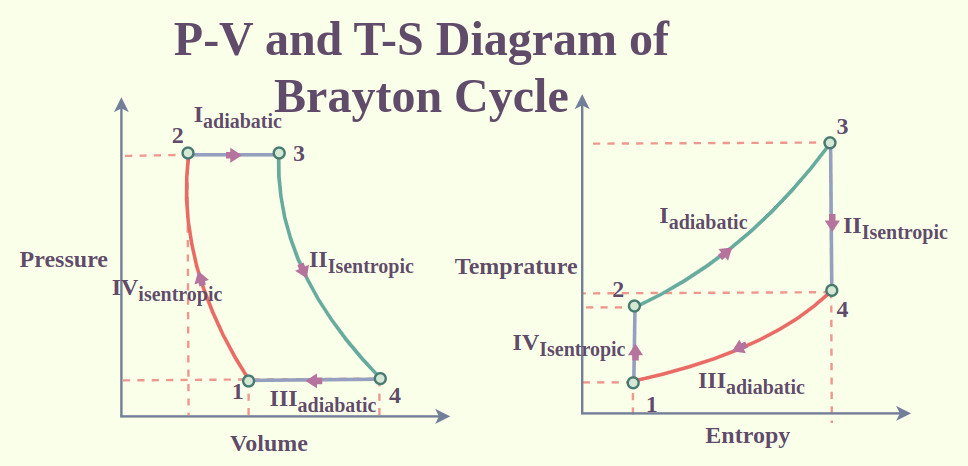
Â
There are numerous applications for the Brayton cycle, including:
- Gas Turbine Engines
- Jet Engines
- Turbochargers
- Air Compressors
- Spacecraft Power Systems
Stirling Cycle
The operation of a Stirling engine, a particular kind of heat engine, is described by the Stirling cycle, a thermodynamic cycle. It bears the name of Scottish cleric Robert Stirling, who developed the engine in 1816. Because of its great efficiency and versatility in heat sources, the Stirling engine is popular for use in applications like electricity production, heating, and cooling.
The Stirling cycle consists of four main processes:
- Compression: The cycle starts with an isothermal compression process, in which the working fluid (usually a gas, such helium or hydrogen) inside the engine is heated by an external heat source (such as a burner or solar radiation). The gas expands as a result of the heat, raising the pressure.
- Heat Addition: The working fluid enters a regenerator, a heat exchanger that stores and releases thermal energy, after compression. The working fluid is in contact with a high-temperature heat source during a constant volume heat addition procedure after that. As a result, the temperature and pressure rise and the expansion continues.
- Expansion: From the hot side of the engine to the cold side, where it enters the expansion area, the working fluid is expanded and heated. Since the gas cools and its pressure drops during this expansion, it is an isothermal process, meaning that the temperature stays constant.
- Heat Rejection: The working fluid then enters a constant volume heat rejection procedure on the cold side of the engine. A low-temperature heat sink, like air or water, contracts and loses pressure when heat is released into it.
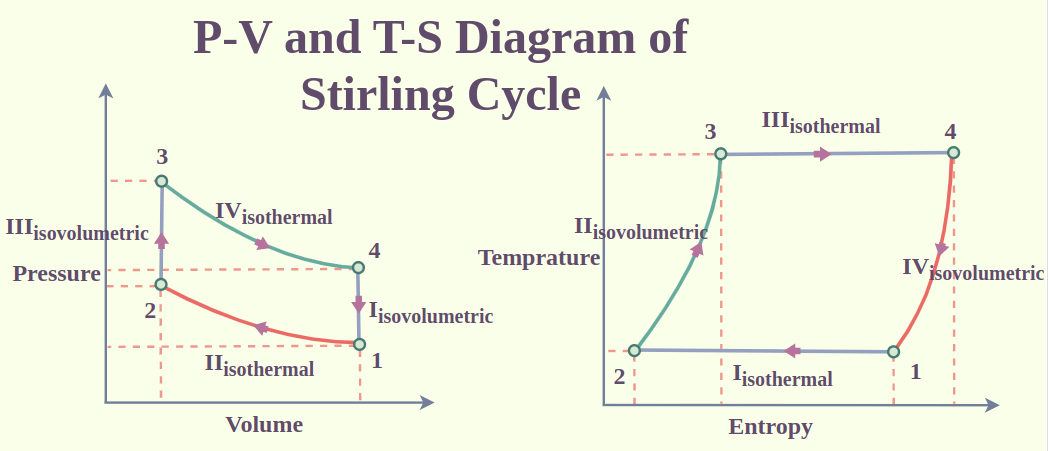
After heat rejection, the working fluid goes back to the compression space to start the cycle over. The Stirling cycle is a closed-loop process, which means the working fluid stays inside the engine and goes through the same cycle repeatedly.
Processes in Thermodynamic Cycles
There are various processes in each Thermodynamic Cycle, some of these processes are:
Heat Addition and Rejection
The working fluid enters a regenerator, a heat exchanger that stores and releases thermal energy, after compression. The working fluid is in contact with a high-temperature heat source during a constant volume heat addition procedure after that. As a result, the temperature and pressure rise and the expansion continues.
The working fluid then enters a constant volume heat rejection procedure on the cold side of the engine. A low-temperature heat sink, like air or water, contracts and loses pressure when heat is released into it.
Compression and Expansion
The cycle starts with an isothermal compression process, in which the working fluid (usually a gas, such as helium or hydrogen) inside the engine is heated by an external heat source (such as a burner or solar radiation). The gas expands as a result of the heat, raising the pressure.
From the hot side of the engine to the cold side, where it enters the expansion area, the working fluid is expanded and heated. Since the gas cools and its pressure drops during this expansion, it is an isothermal process, meaning that the temperature stays constant.
Isentropic and Adiabatic Processes
Isentropic expansion is a process in which no heat is transferred and the working fluid expands. This is an unrealistic method that cannot be carried out in real life. Making the expansion process as isentropic as possible, however, can boost the Brayton cycle’s effectiveness.
Adiabatic processes are those processes in thermodynamic cycles, which involve the transfer of energy without the transfer of heat or mass to the surrounding. In both expansion and compression condition remains the same. Change of temperature of a gas by applying and removing the pressure is an example of an Adiabatic process.
Constant Volume and Constant Pressure Processes
The air-fuel mixture is ignited by a spark, causing it to combust and expand. Because the expansion occurs at a steady rate, no work is done during this process. The cylinder’s exhaust gases are evacuated, and the piston returns to the top of the cylinder. Because this is a constant-volume process, no work is done during this time.
In a process called constant pressure heat addition, the working fluid is heated at a fixed pressure. Typically, this is accomplished by burning fuel with the help of air. The working fluid receives heat from combustion, which raises its temperature and pressure. In a process called constant pressure heat rejection, the working fluid is cooled at a fixed pressure. Most frequently, a heat exchanger is used to do this. The environment’s temperature and pressure decrease as a result of the working fluid’s heat being transferred to it.
Also, Read
FAQs of Thermodynamics Cycle
Q1: What is a Thermodynamic Cycle?
Answer:
A series of thermodynamic processes that result in a system returning to its initial condition is known as a thermodynamic cycle. This implies that the internal energy of the system remains constant throughout the entire cycle. Heat engines, which turn thermal energy into work, are modelled using thermodynamic cycles.
Q2: What are the Different Types of Thermodynamic Cycles?
Answer:
Some of the most common types of thermodynamic cycles are:
- Carnot Cycle
- Rankine Cycle
- Otto Cycle
- Diesel Cycle
- Brayton Cycle
- Stirling Cycle
Q3: How is Thermodynamics used in Engines?
Answer:
Engines employ thermodynamics to turn thermal energy into work. This is accomplished by using a thermodynamic cycle, which is a series of thermodynamic processes that the system goes through. The quantity of work completed throughout the cycle in relation to the amount of heat input into the cycle determines an engine’s efficiency.
Q4: What are the Uses of the Thermodynamic Cycles?
Answer:
The most common use cases of various Thermodynamic Cycles are:
- Fuel-powered engines employ the Otto cycle.
- Diesel engines employ a cycle called the Diesel cycle.
- Use of the Rankine cycle in steam turbines
- Gas turbines employ the Brayton cycle.
Q5: Which Thermodynamic Cycle is used in Power Plants?
Answer:
The 2 main thermodynamic cycles used in the generation of electricity are the Rankine and Brayton cycles. These cycles are also referred to as power cycles, as they convert heat input into mechanical work output.
Q6: Is Otto Cycle a Thermodynamic Cycle?
Answer:
Yes, Otto Cycle is a thermodynamic cycle. An Otto cycle is an idealized thermodynamic cycle that describes the functioning of a typical spark ignition piston engine. It is the thermodynamic cycle most commonly found in automobile engines.
Share your thoughts in the comments
Please Login to comment...