Methodology of Six Sigma
Last Updated :
29 Apr, 2024
Six Sigma is a powerful methodology for process improvement and quality management that originated with Motorola Corporation. This approach revolves around expressing process capability in terms of defects per million opportunities (DPMO), where a Six Sigma level implies a mere 3.4 parts per million defect probability.
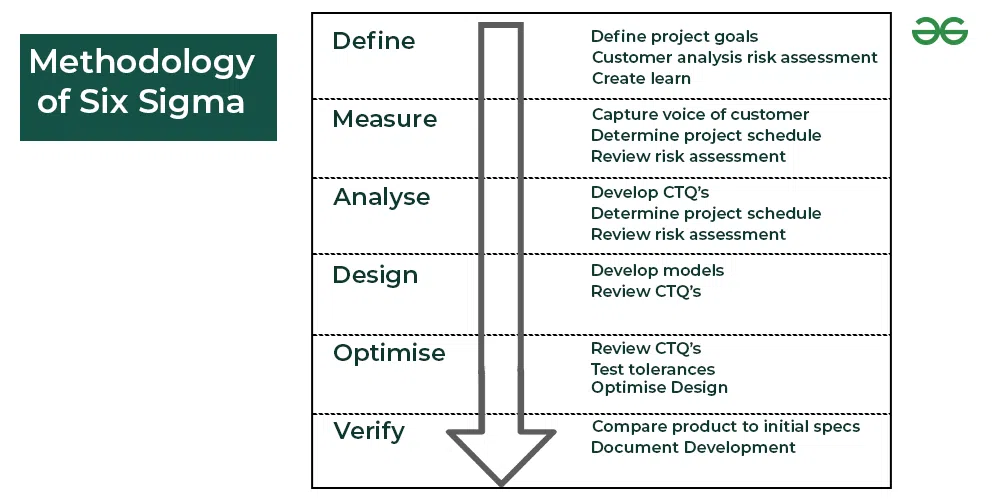
Key Concepts of Six Sigma
- Critical to Quality: Attributes most important to customers
- Defect: Failure to deliver what the customer value
- Process Capability: What process can deliver
- Variation: What the customer sees and feels
- Stable Operations: Ensuring consistent, predictable processes to improve what the customer sees and feels
- Design for Six Sigma: Designing to meet customer needs and process capability
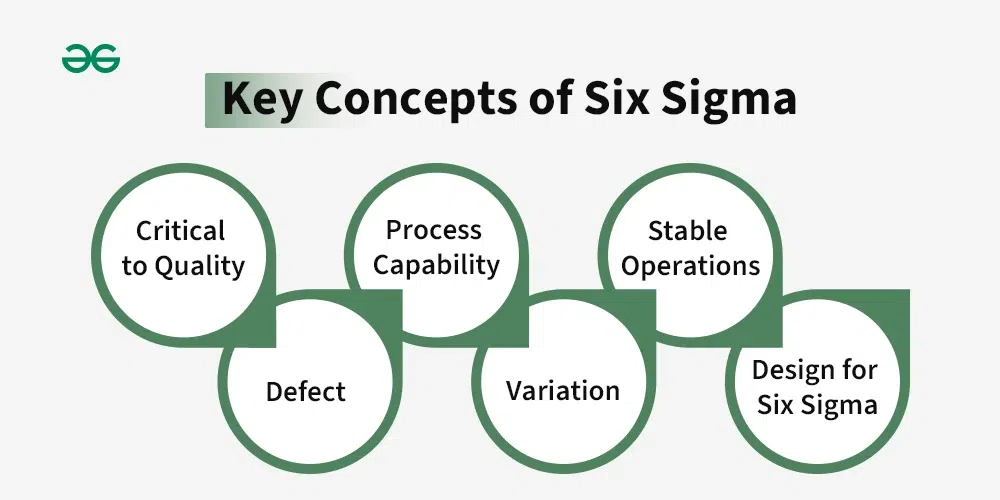
Methodology of Six Sigma
The Six Sigma methodology follows a well-defined and structured approach known by the acronym DMAIC: Define, Measure, Analyze, Improve, and Control. This powerful framework guides organisations in identifying and addressing challenges, optimizing processes, and achieving outstanding performance:
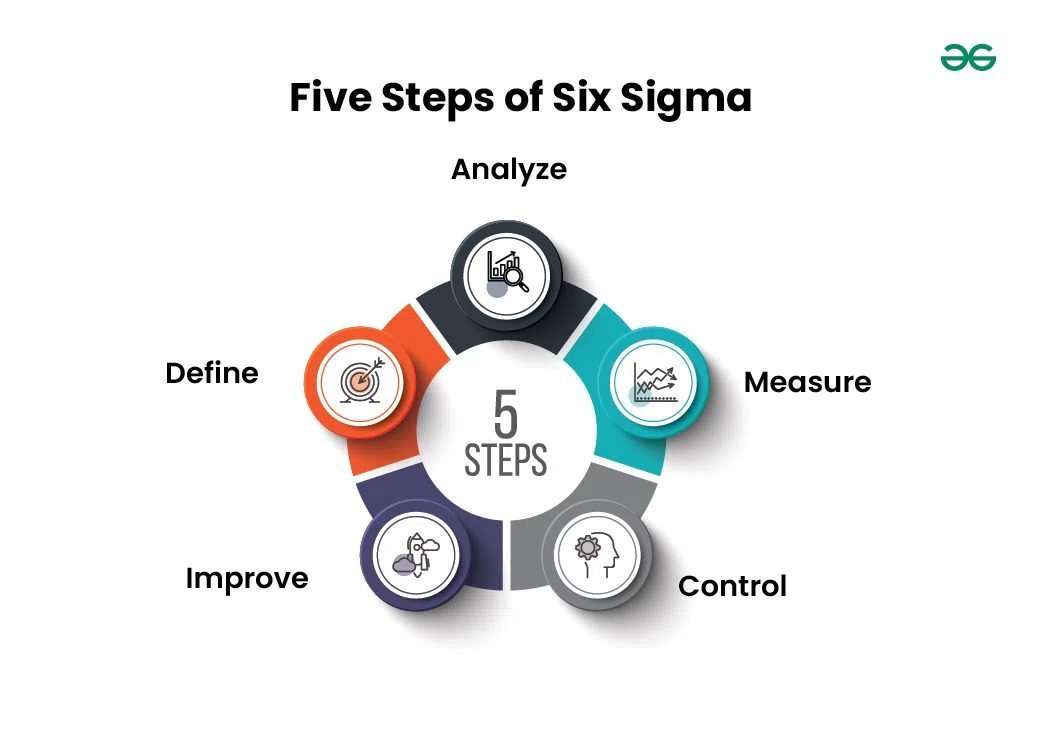
Methodology of Six Sigma
1. Define
The first step involves a clear definition of the problem at hand. By precisely identifying the areas that require improvement, organisations can set the stage for focused and effective problem-solving.
Â
2. Measure
In this crucial phase, data collection and analysis take center stage to quantify the problem’s extent. By understanding the current performance levels and assessing the problem’s impact, teams gain valuable insights for informed decision-making.
Â
3. Analyze
Armed with relevant data, the Analyze phase delves deeper into the root causes of the problem. By employing advanced Six Sigma tools and techniques, organisations gain a comprehensive understanding of the factors contributing to the issue and areas requiring attention.
Â
4. Improve
With data-driven solutions in hand, the Improve phase sets out to address the root causes and implement effective changes. This phase is pivotal in optimizing processes, bringing about tangible improvements, and achieving exceptional results.
Â
5. Control
The final phase, Control, ensures that the improvements made during the previous stages are sustained over time. By implementing robust control measures, organisations safeguard against the problem’s recurrence and maintain stable and efficient processes.
Share your thoughts in the comments
Please Login to comment...