Heat plays a very important role in our daily life. All heat requirements in our daily lives such as cooking, space warmers, submersion water heaters, and electric toasters, as well as in industrial applications such as fusion, annealing, liquefaction of metals, and solidifying can be effortlessly fulfilled by electric heating, over the other forms of traditional heating.
Heat and Electricity are interconvertible. Heat can be generated by allowing the flow of electricity through the material to be heated. This is termed electric heating; there are diverse approaches to heating a substance, but electric heating is considered significantly superior compared to the heat produced by coal, oil, and natural gas.
When the current is allowed to flow through a conductor, it gets heated up due to I2R losses, and this heating characteristic of the electric flow is employed in industrial and domestic gadgets. This form of heating is also considered safe and efficient as compared to others as most of the electrical energy is converted into heat energy. The regulation of heat is also easy as by varying the amount of potential applied or current supplied more the amount of heat can be generated.
Heating Effect Of Electric Current
when an electrical current is allowed to pass through a conductor, it generates excess heat due to the resistance of the conductor to the flowing current. The work done in overcoming the resistance of the conductor to the current generates heat in that conductor. The fast-moving electrons have high kinetic energy. These mobile electrons collide with the ions of the conductor and transfer their kinetic energy, inducing ions to oscillate. As a resist-moving, the ions vibrate at a very large rate, and consequently, the temperature of the conductor increases
The heating effect of an electric current depends mainly on the below mentioned three factors:
- The resistance, R of the conductor. As the resistance increases heat produced also increases.
- The time, t for which current flows. with time the amount of heat produced increases.
- The amount of current, I. larger the current, larger the amount of heat generated.
Hence the heat generated due to electric current, I through a conductor of resistance, R for a time, t is given by
H=I2RT
This equation of electrical heating is called the Joule’s equation of electrical heating.
Electrical Heating Devices
Electric Iron
Electric iron is made using Mica which is an insulator. So in the iron mica is placed between the metal part and the electrical coil. As the current is supplied the coil becomes warm which then transfers the heat to the metallic part through the mica used. Finally the metallic part gets heated up to a very high temperature and is used in the ironing of clothes. The amount of heat generation or the temperature of the iron can be regulated by regulating the current flow in the coil which is controlled by the temperature regulator used in electric iron.
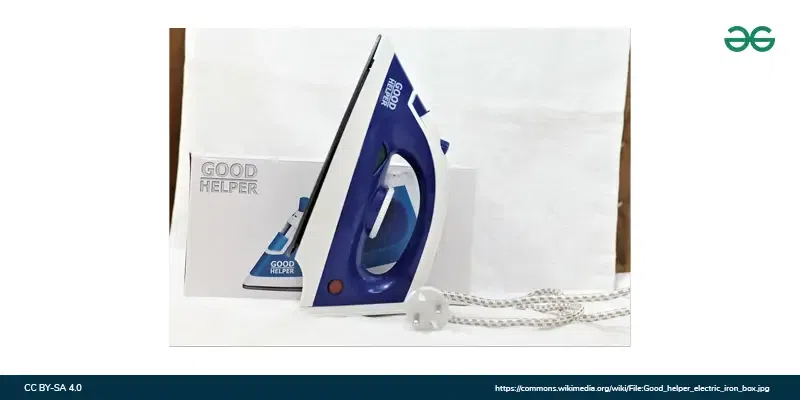
Electric Iron
Electric Bulb
Electric bulb consists of a very thick metallic wire of tungsten. Tungsten is very high resistance element, most of the electrical current which is passed through it is converted into heat because of its highly resistive nature. The heated up tungsten in turn emits light. The metallic wire is kept in an inert environment (usually the bulb is filled with some inert gas like argon) so that it does not easily gets weared out. Most of the energy is wasted in the form of heat energy and a small part is useful as light energy, that is the reason it is not being widely used these days.
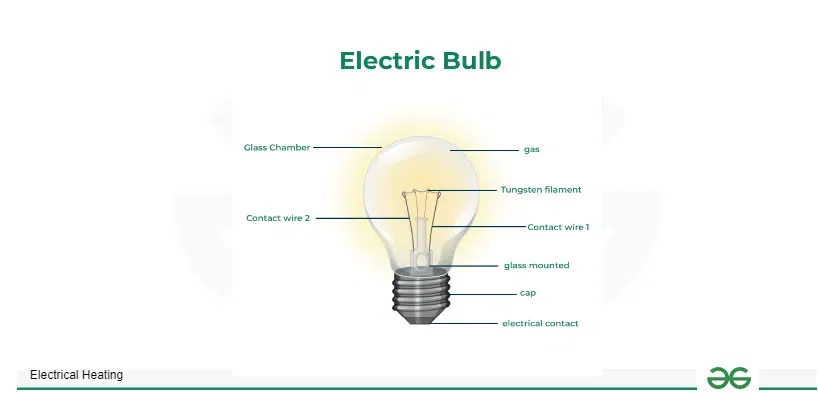
Electric Bulb
Electric Fuse
It is one of the most used and important use of the heating effect of electric current. In various circuits be it in houses, buildings, industries circuit protection is required for overcurrent. Current exceeding limits can damage the equipment and can also cause fire. So to protect the equipment households are usually installed with fuses. Fuse contains a conducting wire which has a very low melting point. It is connected in series with the circuit, so whenever the current rises above limit for a certain period of time it gets heated up and melts down breaking the circuit. The current bearing capacity of the fuse wire can be altered by changing the material used or the thickness of wire.
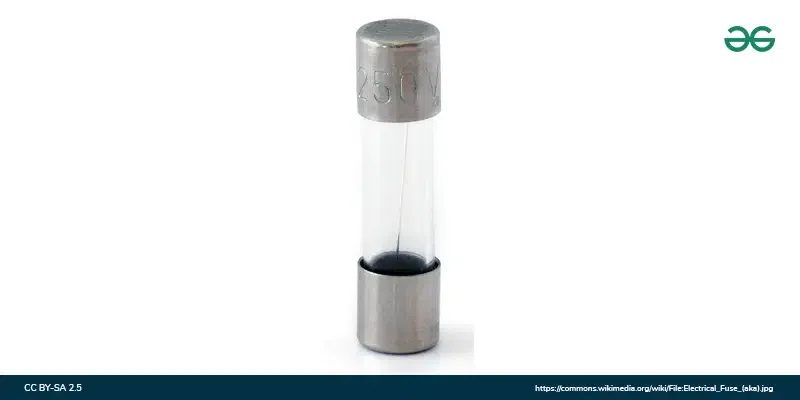
Electric Fuse
Types of Electrical Heating
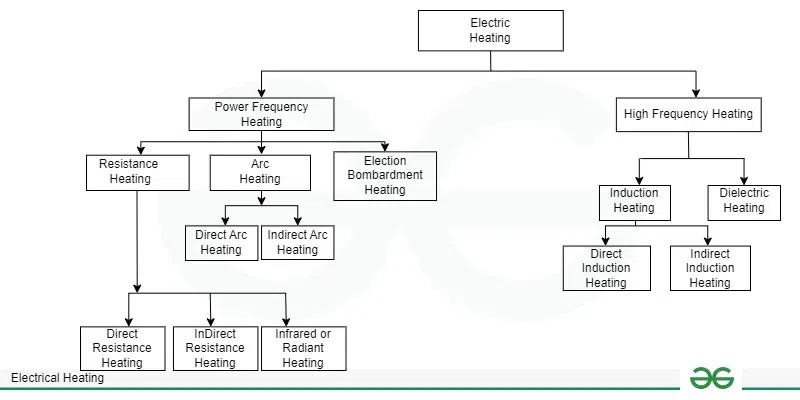
Types of electrical heating
Power Frequency Heating
In this type of electrical heating the supply directly generates large amount of heat in which the target item is placed. Usually this power supply is at 50Hz.In this heating AC current is passed through resistive element such as wire and coil, which is in direct contact with the target material. The resistance of the material causes heat up rapidly as electric energy is converted into thermal energy.
one of the advantage of those heating is its simple and effective in generating heat. It is widely used in applications such as industrial melting of metals, heat treatment of materials, drying processes, and domestic heating appliances like electric stoves and water heaters.
Power Frequency can Categorized as :
- Resistance Heating
- Arc Heating
- Election Bombardment Heating
Resistance Heating
We already know that there will always be a power loss in a conductor due to its resistance which results in the generation of heat . This property resistance can be used for heating a substance, known as resistance heating.
It is also of 2 types :
- Direct Resistance Heating
- Indirect Resistance Heating
- Infrared or Radiant Heating
Direct Resistance Heating: In this type of electrical heating the supply directly generates high heat in which the item to be heated is placed. In this heating method, the material or charge which is to be heated is taken as resistance and current is passed through it. The charge can be in the form of pieces, powder or a liquid. For example resistance welding as discussed next, electrode boiler for heating water etc.
As shown below is the resistance welding, it is a process in which work pieces are welded due to a combination of a pressure applied to them and a localized heat generated by a high electric current passing through the contact area.
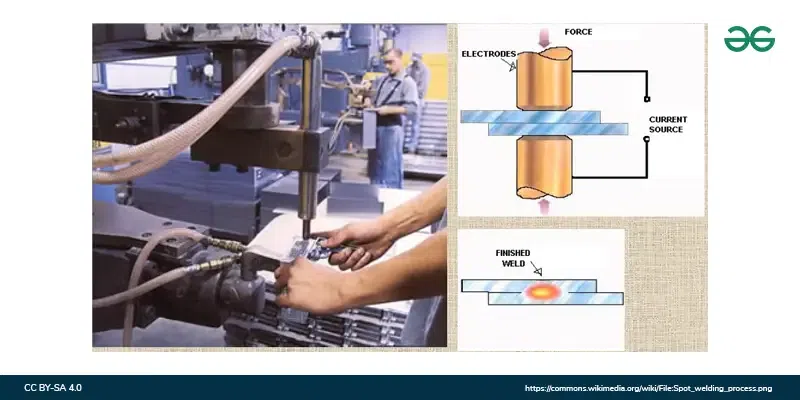
Resistance welding
As shown below is another representation of direct resistance heating in which charge is placed in a container and supply is passed through the electrodes, the heat produced in the electrodes is directly transferred into the charge resulting in direct resistance heating.
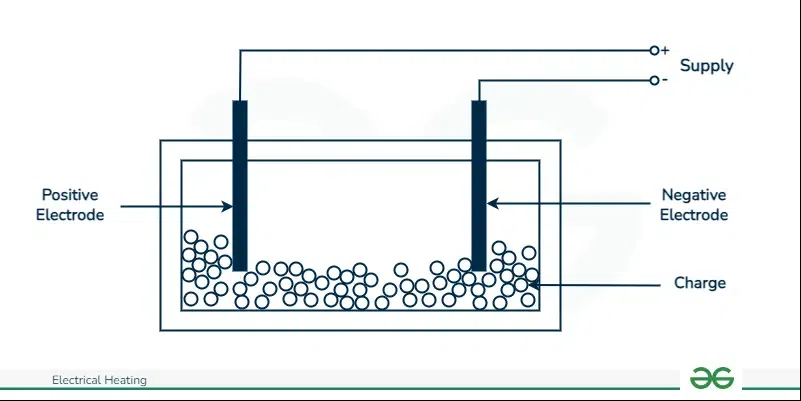
Direct Resistance Heating
Indirect Resistance Heating : In this the heat is produced which is proportional to I2R and is then delivered to the charge by one or more of the modes of transfer of heat like conduction, convection and radiation. So Unlike Direct Resistance Heating in this type of electrical heating power supply does not directly generates high heat in which the target item is placed. For example room heater, hair dryer etc.
As shown below is the representation of indirect resistance heating. In this unlike direct resistance heating configuration the heating element is not in direct contact of the charge therefore the name indirect heating is used. The heating element gets heated up on the application of supply voltage/current and the heat is transferred to the charge by one of the methods – conduction (in which heat is transferred through physical contact), convection(heat transfer mechanism in fluids), radiation(transfer of heat without direct physical contact).
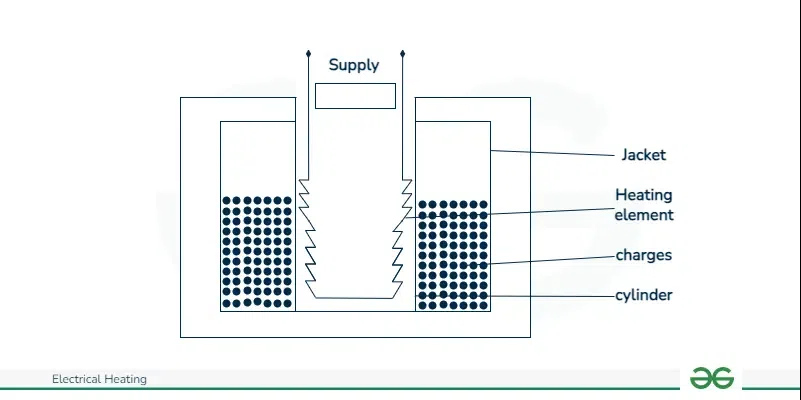
Indirect Resistance Heating
Radiant or Infrared heating: In this the heat energy is transferred through electromagnetic radiations. It is the heat transfer from hot source to the people or objects in the room via infrared radiations. It is the effect we feel from the warmth of a hot stove element from across the room. It is usually more efficient than the normal baseboard heating and also more efficient than forced air heating because it reduces duct losses. Its popularity these days is increasing because it is clean, quiet, dependable, invisible and efficient.
Radiant heating can be applied on the floor or the walls as shown below, the heater on wall emits infrared waves that heat up the room gradually.
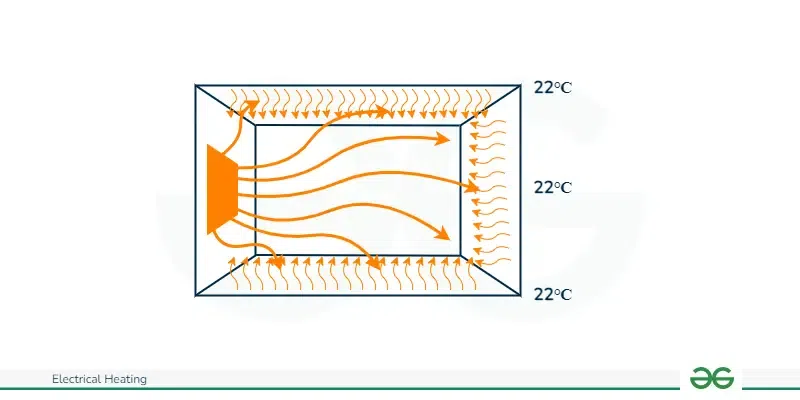
Infrared Heater
Applications
- It can be used for drying purpose.
- Heat treatment of metals such as hardening, annealing, etc.
- it can be used in Commercial and domestic cooking
- In various equipment like electric heater, kettle, iron etc. use resistance heating.
Temperature Control of Resistance Heating
All the types of electric resistance heating are controlled with the use of a thermostat. Baseboard heaters typically uses line-voltage thermostats, directly managing power to the heating unit. On the other hand, other devices utilize low-voltage thermostats, which employ a relay for switching the device on and off. Line-voltage thermostats can be built into the baseboard heater, but they often don’t sense the room temperature accurately. It’s best to use a remote line-voltage or low-voltage thermostat installed on the interior wall. Both the line and the low-voltage thermostats are programmable thermostats for automatically lowering down the temperature at night or while you’re away.
Arc Heating
Arc heating can be Categorized as
- Direct Arc Heating
- Indirect Arc Heating
Direct Arc Heating: In this form of electric heating, the arc is produced by striking the electrode to the body to be heated and the developed heat is directly conducted and absorbed by the object. In the production of steel this kind of Arc heating is generally used.
Below mentioned diagram is a Direct Arc Furnace which is very popular for the melting of alloys of steel and it ranges in size from a few kilograms to 100 tons. The arc furnace typically consists of a cylindrical steel shell which is lined up with acid/basic refractories. The roof generally contains 3 carbon electrodes as shown in the diagram which operates on a high tension 3 phase supply. The distance between the electrodes and the bath is controlled automatically and it determines the input power into the bath. Some of the advantages of this arc furnace include high pouring temperatures, high melt rates etc.
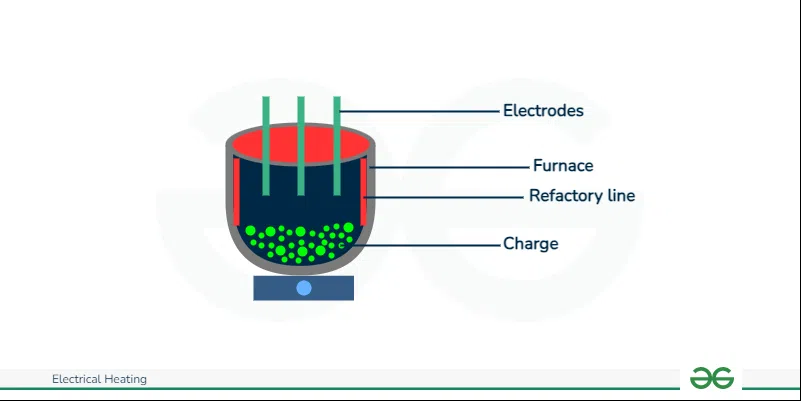
Direct Arc Furnace
As shown above when 3 phase electricity is supplied to the electrodes the charge inside furnace gets ionized and heated up.
Indirect Arc Heating: In indirect arc heating, the arc is formed between the two electrodes, the developed heat is transferred to the substance by radiation. This method is generally used in the melting of metals which are non-ferrous in nature.
Indirect Arc furnace shown below generally consists of a horizontal barrel shaped steel shell lined up with refractories. The heating process involves the formation of arc between the 2 carbon electrodes which generates heat which is further transferred to the charge via radiation. The structure of the arc which is barrel shaped steel is specifically designed to rotate and reverse through approx. 180 degree centigrade to increase the melting efficiency of the unit. These are suitable for melting various ranges of alloys but are used particularly for copper based alloys.
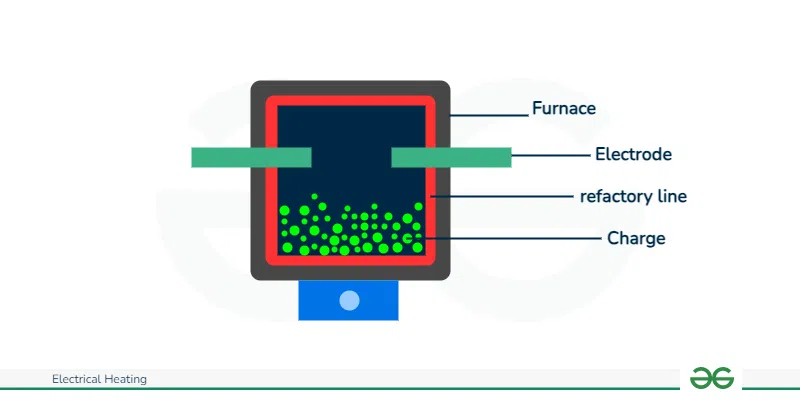
Indirect Arc Furnace
Electron Bombardment Heating
It is an electrical heating method in which high energy electrons under variable degrees of vacuum depending upon the source of the electrons are bombarded/fired over an material releasing their energy and thus causing the material to get heated up. Example: used in the processes for treating semiconductor wafers.
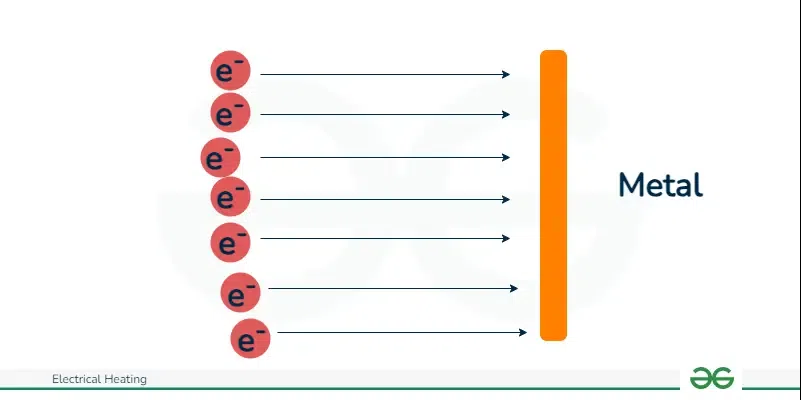
Electron Bombardment Heating
High Frequency Heating
In this method of heating a specific frequency energizes the molecules to cause heat within the target items (By using the electromagnetic resonance). This method is more efficient and usually quicker.
It can be categorized as:
- Induction heating
- Dielectric heating
Induction Heating
It is a method in which a material which is electrically conductive, is heated, by placing it in an alternating electromagnetic field.
Direct Induction Heating: In direct induction heating, the electric current is induced by electromagnetic action in the body that is to be heated. The induced current when flow in the body is opposed by the resistance of the body which develops the heat and hence raise the temperature of the body. Direct induction heating is usually used to melt the object in induction furnace, and also the eddy current heaters are used for heat treatment of metals.
It generally includes the below mentioned basic components/processes:
- Induction Coil: A conductive coil generally made out of copper or aluminum is wound around the object to be heated.
- Magnetic Field Generation: As per Faraday’s law of electromagnetic induction when an AC current flows through a coil, it generates a rapidly changing magnetic field around it.
- Eddy Currents: This varying magnetic field induces eddy currents in the electrically conductive element places near the coil.
- Heating: Due to these eddy currents heat is generated in the material due it resistance.
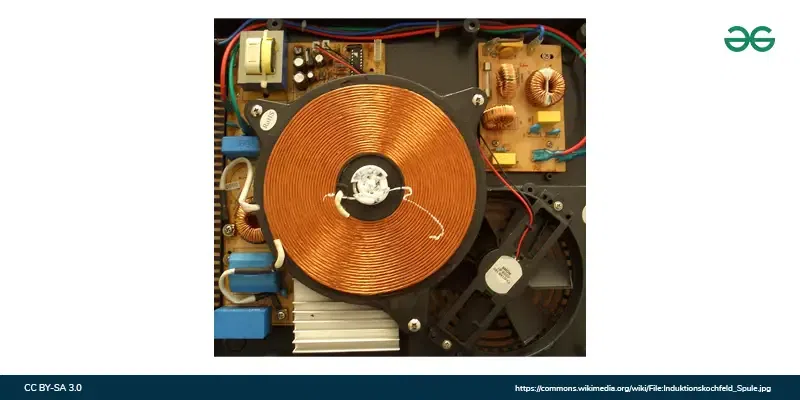
Direct Induction Heating
Indirect Induction Heating: In this method of electric heating, the eddy currents are induced in the heating element and not the body to be heated, by electromagnetic induction. The eddy currents formed in the heating element produce the heat which is then transferred to the body that is to be heated up by convection or radiation. Indirect induction heating is generally used in certain ovens used for heat treatment of metals. The reference can be taken from the induction cooking image used in applications of electrical heating section.
Dielectric Heating
when high-frequency alternating electric field/radio waves /microwave electromagnetic radiation are used to heat the dielectric materials is known as dielectric heating. Dielectric heating is usually used for heating insulators such as wood, plastic, etc. which cannot be heated easily by other electric heating methods as discussed above. It is also called the high-frequency capacitive heating. The supply frequency required for dielectric heating varies from 5 MHz to 5 GHz and the applied voltage is about 20 kV.
The main principle behind its working is same as that of a capacitor. As shown below is the pictorial representation of dielectric heating. There are 2 electrodes between which there is a dielectric workpiece. when a potential difference is applied the electrode and dielectric material combination act as a capacitor. the capacitor formed may not be a pure capacitor but a small amount of resistance also exists.
The power consumption for the capacitor configuration is directly proportional to frequency of the supplied voltage and the square of voltage itself.
P ∝ f*V2
The main advantages of using this method of heating is that with this technique the material is uniformly heated, also the heating process can be accelerated by increasing the frequency. Also it is the one and only efficient method of heating the non conducting material.
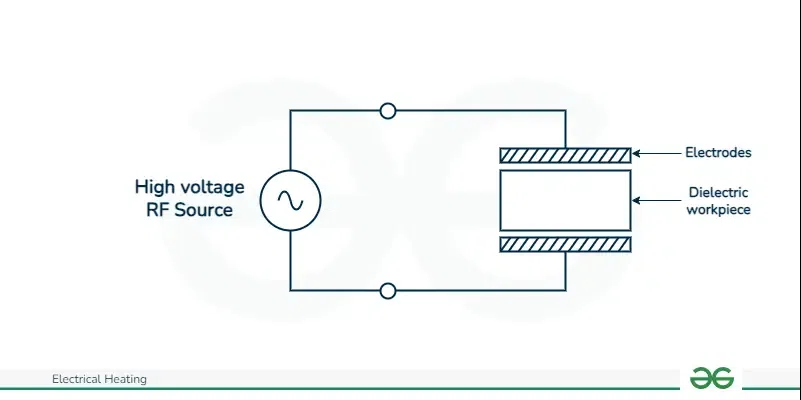
Dielectric Heating
Requirements for a Good Heating Material
For a good heating material, the heating element must have fallowing properties:
- It should have a high specific resistance such that a small length of wire (R =ρl/a , ρ =Ra/l ) can produce the required amount of heat.
- The melting point should be high so that high temperature can be obtained.
- The temperature co-efficient should be low as for accurate temperature control, the resistance should be nearly constant at all temperature is possible only if the resistance does not change with changing temperature.
- It should not get oxidized at higher temperatures otherwise its life is reduced and needs frequent replacements.
The most widely used heating elements are either alloy of nickel and chromium or nickel-chromium-iron(Ni-Cr-Fe), nickel-chromium-aluminum(Ni-Cr-Al), nickel-copper(Ni-Cu). Iron can be used as it reduces the cost but it has a drawback that it lowers the life of the element.
Design of Heating Element
The aim of design of heating element is to find size and length of wire require as a heating element. Wire used may be circular in shape or rectangular like a ribbon depending upon the requirements. Here we are going to discuss the most commonly used design, the circular one.
Circular Wire
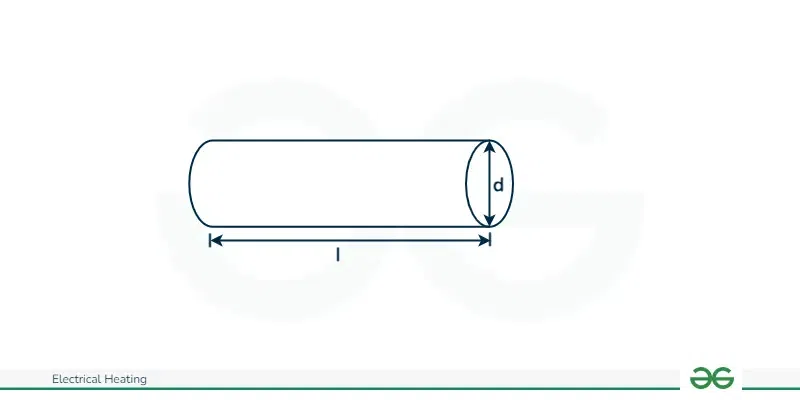
Heating Element With Circular Cross Section
R =ρl/a => R =4ρl/πd2 ———1
P=V2/R ———2
putting value of R from eqn 1 in eqn 2
l/d2 = πV2/4ρP ——-3
Surface Area, S=πdl
Total heat dissipated, Ht = πdlH
where, H=Heat dissipated / Unit area
At steady state temperature,
Power input=Heat Dissipated
P=πdH
πd2V3/4ρl = πdlH
d/l2 = 4ρH/V2 ——–4
solving equation 3 and 4 length and diameter of wire can be determined.
l = ( V2P / 4πρH2 )1/3
d = ( 4ρP2 / π2V2H )1/3
Advantages of Electrical Heating
The primary advantages of electric heating over alternate systems of heating (i.e. coal, gas, or oil) heating are:
- Economical: Electric heating is economical as electric furnaces are less costlier in initial cost as well as maintenance cost. It does not necessitate any care, so there is a substantial saving in labor cost over other methods of heating. Furthermore, the electric power is also inexpensive as it is generated on a large scale.
- Cleanliness: As dirt and ash are wholly eradicated in electric heating system, so it is a tidy system and scrubbing expenses are rendered to a minimum.
- Absence of fuel gases: As no fuel gases are produced in this system, the environment around is clear and pollution-free.
- Simplicity of regulation: Uncomplicated, precise, and trustworthy , temperature of a furnace can be regulated with the aid of manual or automatic mechanisms. The desired temperature can be regulated in electric heating system, which is not convenient in other heating methods.
- Efficiency: It has been essentially found that 75 to 100% of the heat generated by electric heating can be effectively utilized as the origin can be brought directly to the point where there is a heat requirement, thereby diminishing the losses.
- Automatic protection: Suitable switchgears in electric heating systems can offer automatic protection against overcurrents or overheating.
- Better working conditions: This type of heating system produces no irritating noise and the radiation losses are negligible. Thus working with electric furnaces is quite convenient.
- Safety: Electric heating is notably safe and responds quickly.
- Upper limit temperature: There exists no Upper limit temperature maximum temperature limit, aside from the material’s capacity to withstand heat.
- Special heating requisites: specific requirements of heating such as uniform heating of material or heating of one particular part of the job without affecting others, heating of insulated materials, heating without oxidation can be met only in electric heating system
Conclusion
One of the best advantages of electrical heating is that unlike some traditional heating methods, electrical heating allows for rapid and accurate adjustments to temperature. In addition to this such systems are often compact and easy to install. In industrial applications, electrical heating plays a critical role in processes such as melting, drying, and curing. Its precision and responsiveness are of much importance in critical manufacturing process. Advancements in material and technology continue to increase the efficiency and performance of heating systems.
Despite all these merits there are some challenges in overall efficiency and environmental impact. The efficiency of electrical heating system is dependent on the energy mix used for electricity generation, with concerns about carbon emissions and resource consumption. Therefore implementation of cleaner and more energy-efficient technologies is required.
In conclusion, electrical heating plays a very important role in meeting various heating needs with an advantage of speed, precision and adaptability. The requirement is to reduce environmental implications by introducing renewable energy sources in electricity generation.
FAQs on Electrical Heating
Are electric heating systems energy-efficient?
These systems are efficient usually but efficiency of the heating system depends on various parameters like heating material, thermostat settings, operating voltage, maintenance etc.
Is it expensive to operate electric heating systems?
Electric heating can be more expensive than some other heating methods, especially in areas where electricity costs are high. However, advancements in technology, such as programmable thermostats, can help manage and reduce energy consumption.
Can electric heating be used for whole-house heating?
yes electrical heating can be used for whole house heating. However, their suitability depends on factors such as the size of the house, insulation, and local climate.
Are there any safety concerns with electric heating?
It is considered safe generally but as electricity is involved in this so precautions should be taken to avoid overloading circuits, and proper installation by qualified professionals is essential.
What maintenance is required for electric heating systems?
Periodic cleaning of heating elements, checking for loose connections, and ensuring proper insulation are some of the kinds of maintenance required.
Share your thoughts in the comments
Please Login to comment...