What Is Lean Project Management?
Last Updated :
28 Mar, 2024
Lean project management is a strategy for running projects that aim to make them more efficient and effective. Rather than just focusing on completing tasks, it looks at how to cut out any unnecessary steps or waste in the process. This method started in manufacturing but has spread to other fields. The main goal is to give customers value while using as few resources as possible. This saves time and money, boosts quality, and keeps customers satisfied. Essentially, lean project management is about working smarter, not harder, to get better outcomes.
What Is Lean Project Management?
Lean Project Management is a method for overseeing projects with a focus on efficiency and resource optimization. Instead of just completing tasks, it prioritizes delivering value to customers while minimizing waste. Originating from manufacturing practices, it’s now used in various industries like IT, construction, and healthcare. It involves identifying and cutting out unnecessary activities and processes that don’t add value to the project. By emphasizing continuous improvement and team collaboration, it aims to boost productivity, cut costs, and speed up project delivery.
- Key principles include defining value from the customer’s perspective, eliminating waste, optimizing workflow, minimizing inventory, and striving for continuous improvement.
- Ultimately, lean project management helps organizations achieve better outcomes by maximizing efficiency and providing superior value to customers.
Why Lean Management Is Important?
Lean management is crucial for many industries because it helps to make processes more efficient, cuts waste, and boosts overall effectiveness.
- Cost Savings: Lean management is all about finding ways to do things more efficiently, which means saving money. By cutting out unnecessary steps and resources, companies can significantly reduce their costs over time. This can include anything from using fewer materials to streamlining transportation or production. Ultimately, these savings can make a big difference to a company’s bottom line, making them more competitive in the market.
- Better Quality: Lean management focuses on doing things right the first time. By standardizing processes and continually improving them, companies can produce higher-quality products and services. This not only makes customers happier but also saves money by reducing mistakes and the need for rework. Plus, delivering better quality can help companies build a strong reputation and gain loyal customers.
- Increased Productivity: Lean management helps companies work smarter, not harder. By identifying and eliminating process bottlenecks, companies can get more done with the same amount of resources. This can involve anything from rearranging workflows to empowering employees to make decisions on the ground. Ultimately, this leads to higher productivity and a more competitive edge.
- Customer Satisfaction: At its core, lean management is all about delivering value to customers. By focusing on what customers want and delivering it efficiently, companies can keep their customers happy and coming back for more. This can involve anything from faster delivery times to better customer service. Happy customers are more likely to stick around and recommend a company to others, leading to long-term success.
- Employee Engagement: Lean management involves everyone in the organization, from top to bottom. By giving employees a voice in how things are done and encouraging them to continuously improve, companies can boost morale and motivation. This can lead to higher job satisfaction, lower turnover rates, and ultimately, better business results.
Improve Your Workflow with Lean Project Management
Improving your workflow with lean project management means making your processes more efficient and effective.
- Visualizing Workflows: In lean project management, it’s crucial to have a clear picture of how work flows through your project. This can be done using simple visual tools like boards or charts. When everyone can see what needs to be done and where things are at, it becomes easier to spot any bottlenecks or inefficiencies and make improvements.
- Standardizing Processes: Standardization is about creating consistent ways of doing things. By establishing standard procedures for tasks, you reduce errors, save time, and make it easier to train new team members. When everyone follows the same process, it becomes easier to predict outcomes and maintain quality.
- Empowering Teams: Lean project management encourages teams to take ownership of their work and make decisions independently. When team members have the freedom to solve problems and make improvements on their own, they become more engaged and motivated. This leads to better collaboration and ultimately, better results.
- Continuous Improvement: Lean project management is all about getting better over time. This means constantly looking for ways to improve your processes and make them more efficient. By regularly reviewing your workflows, gathering feedback, and making adjustments, you can ensure that your projects are always running as smoothly as possible.
Improving your workflow with lean project management is about finding ways to work smarter, not harder. By visualizing your processes, standardizing your procedures, empowering your teams, and continuously seeking improvement, you can achieve better results with less effort.
What Are the Benefits of Lean Project Management?
Lean project management brings numerous benefits to organizations, enhancing their operations and outcomes:
- Faster Project Delivery: By streamlining processes and eliminating unnecessary steps, lean project management enables teams to complete projects more swiftly. This efficiency results from a focus on essential tasks and continuous improvement efforts, ensuring that projects move forward without delays caused by inefficiencies.
- Reduction of Project Risks: Lean project management consists of proactive risk management, identifying potential issues early and implementing measures to mitigate them. This approach minimizes the likelihood of project disruptions, such as delays or budget overruns, ensuring smoother project execution and successful outcomes.
- Enhanced Flexibility and Adaptability: Lean project management encourages flexibility in project planning and execution, enabling teams to adapt quickly to changing circumstances or requirements. By breaking down projects into smaller, manageable tasks and prioritizing resource flexibility, organizations can respond promptly to evolving needs, maintaining project momentum and achieving desired results.
- Sustainable Growth and Scalability: Embracing lean project management principles fosters a culture of continuous improvement and innovation within organizations. By regularly reviewing and optimizing processes, teams can identify opportunities for growth and scalability while minimizing waste and inefficiencies. This approach enables organizations to adapt to evolving business needs and expand into new markets, ensuring long-term success and viability.
- Greater Customer Satisfaction: Lean project management prioritizes delivering value to customers by focusing on their needs and preferences. By eliminating waste and delivering high-quality products or services efficiently, organizations can enhance customer satisfaction levels. Timely delivery, product reliability, and responsiveness to customer feedback are crucial aspects that contribute to building strong relationships and loyalty with customers, ultimately driving business success.
The Five Key Principles of Lean Project Management
The five key principles of lean project management serve as fundamental guidelines for organizations aiming to improve efficiency and productivity:
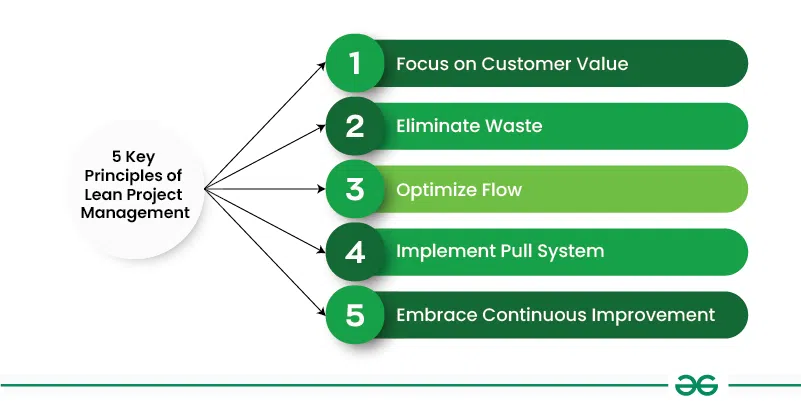
Five Key Principles of Lean Project Management
1. Focus on Customer Value:
The first principle revolves around understanding and prioritizing what customers truly value. By aligning project objectives with customer needs and preferences, organizations can ensure that resources are allocated to tasks that directly contribute to customer satisfaction. This customer-centric approach helps organizations focus on delivering outcomes that meet or exceed customer expectations, ultimately driving business success.
2. Eliminate Waste:
Lean project management consists of the identification and elimination of waste in project processes. This includes activities or resources that do not add value to the final product or service. By minimizing waste, organizations can streamline workflows, reduce costs, and improve overall efficiency. This principle encourages teams to constantly evaluate their processes and eliminate any non-essential activities or bottlenecks that hinder productivity.
3. Optimize Flow:
Creating a smooth flow of work is essential for efficient project management. This principle consists of the removal of obstacles and bottlenecks to ensure that tasks move seamlessly from one stage to the next. By optimizing workflow, organizations can minimize delays, reduce lead times, and improve project throughput. This enables teams to deliver projects more quickly and effectively, meeting deadlines and exceeding customer expectations.
4. Implement Pull Systems:
Lean project management advocates for the implementation of pull systems to minimize inventory and overproduction. Pull systems operate based on customer demand, with work initiated only when there is a specific need. This approach helps organizations avoid excess inventory and resources, leading to cost savings and improved efficiency. By adopting pull systems, organizations can respond more quickly to changes in customer demand and market conditions, ensuring that resources are used effectively.
5. Embrace Continuous Improvement:
The final principle of lean project management consists of the importance of continuous improvement. Organizations are encouraged to regularly review their processes and seek opportunities for optimization. This involves fostering a culture of learning, experimentation, and innovation within the organization. By embracing continuous improvement, teams can identify areas for enhancement, implement changes, and strive for ongoing excellence in project execution.
Conclusion: Lean Project Management
In conclusion, lean project management provides organizations with an effective framework for enhancing project processes and meeting customer needs efficiently. By prioritizing customer requirements, minimizing waste, optimizing workflow, adopting pull systems, and continuously improving practices, organizations can enhance productivity and customer satisfaction. Lean project management encourages collaboration, innovation, and accountability within teams, fostering adaptability to evolving circumstances and ensuring long-term success.
FAQs: Lean Project Management
1. What is Lean Project Management?
Lean project management focuses on efficiency and waste reduction in project processes. It aims to streamline workflows, eliminate non-value-added tasks, and continuously improve project outcomes.
2. How does lean project management differ from traditional project management?
Unlike traditional project management, which follows a rigid approach with fixed requirements, timelines, and processes, lean project management prioritizes flexibility, adaptation, and customer value. It consists continuous improvement and waste reduction.
3. What are the main benefits of implementing lean project management?
Implementing lean project management can lead to faster project delivery, cost savings, improved quality, increased customer satisfaction, and higher employee engagement. By eliminating waste and optimizing processes, organizations can achieve better results more efficiently.
4. How can organizations start implementing lean project management?
Organizations can begin implementing lean project management by assessing their current processes, identifying areas for improvement, and prioritizing projects based on customer value.
Share your thoughts in the comments
Please Login to comment...