What is Inventory?
The term inventory includes both the manufactured products that are available for sale and the raw materials utilized in the manufacturing process. Inventory is among the most valuable assets possessed by a business, as inventory turnover is one of the principal contributors to revenue generation and, consequently, shareholder returns. Inventory is classified as a current asset on the balance sheet of the company. Raw materials, finished goods, and work-in-progress constitute the three categories of inventory.
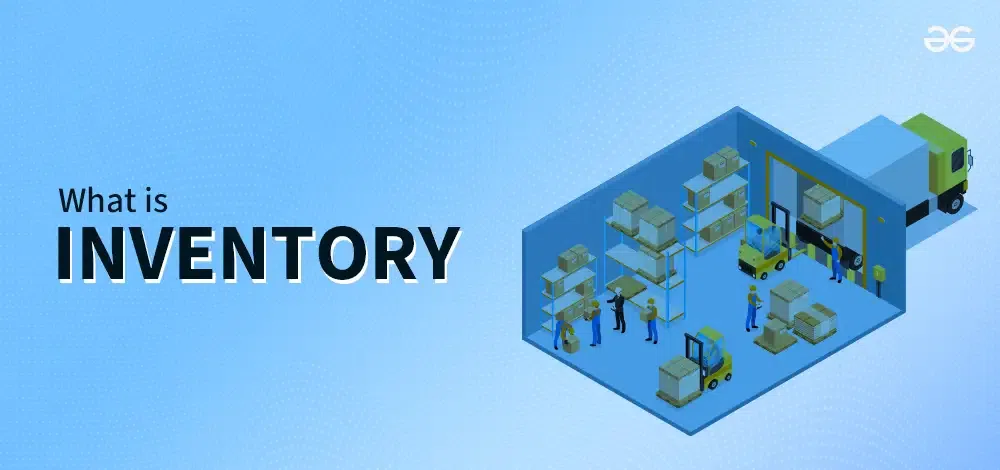
Geeky Takeaways:
- Inventory includes both raw materials used in the production of goods and finished goods for sale.
- Inventory is recorded as a current asset on a company’s balance sheet.
- Inventory is classified into three types, raw materials, work-in-progress, and finished goods.
Types of Inventory
There are four types of inventory, raw materials, work-in-progress (WIP), finished items, and maintenance, repair, and overhaul (MRO).
1. Raw Material: Raw materials are all of the materials that your organization uses to manufacture finished goods. Raw materials can be purchased from any external supplier or can be produced within the organization. There are two types of raw materials, direct and indirect. Direct raw materials are those that are used directly in the final product. These materials are easy to measure and account for on an individual or batch basis. Indirect raw materials are those that are not part of the completed product but are used during the manufacturing process. Indirect raw materials are more difficult to identify and account for since they are not tied to specific batches or units. However, these are necessary for the manufacturing process.
2. Work-in-Progress (WIP): Work-in-progress inventory refers to the inventory the production of which has started but is not completed yet. Work-in-progess inventory needs to go through more stages of production in order to get converted into final goods. It may include both direct and indirect raw materials; the only thing to remember is that the product is not finished and is still in development.
3. Finished Goods: Your finished goods inventory includes all items that are ready to sell. Of course, depending on the manner of operation you choose, this may include slightly different steps. If you employ a make-to-order technique, the finished product is already produced and ready for shipment to clients. If you employ the make-to-stock workflow, the inventory must be stored in a warehouse until an order arrives. In either case, your finished goods inventory should be quite simple to account for and track.
4. Maintenance, Repair, and Operations (MRO): As the name suggests, maintenance, repair, and operations (MRO) inventory is essential for keeping your manufacturing running. MRO inventory is only available for consumption and cannot be purchased by customers.
What is Inventory Management?
Having an excessive quantity of inventory on hand for an extended period of time is generally a bad idea for a business. This is owing to the difficulties it addresses, such as storage costs, spoilage charges, and the risk of obsolescence. Having too little inventory also has its disadvantages. For example, a company risks losing market share and future sales revenue. It is generally a good idea for firms to invest in an efficient inventory management system. This is particularly true for larger businesses with several sales channels and storage facilities. These systems can detect waste, low turnover, and fraud/robbery.
Importance of Inventory Control
Inventory control is critical for businesses across industries for several reasons,
1. Cost Management: Effective inventory control assists organisations in lowering holding costs associated with excess inventory, such as storage, insurance, and depreciation charges. It also minimises the likelihood of inventory obsolescence, which can result in substantial financial losses.
2. Optimised Cash Flow: Maintaining optimal inventory levels allows organisations to free up cash that might otherwise be locked up in excess inventory. This allows them to better organise resources, invest in expansion prospects, and meet other financial obligations.
3. Customer Satisfaction: Effective inventory management guarantees that products are available when customers require them. This reduces stockouts and backorders, resulting in greater customer satisfaction and loyalty. Furthermore, firms can avoid stockpiling commodities that may become obsolete, ensuring that clients have access to the most recent offerings.
4. Improved Operational Efficiency: Inventory control systems offer valuable information about demand patterns, lead times, and reorder points. Businesses can use this data to streamline their procurement, production, and distribution operations, resulting in shorter lead times, fewer stockouts, and more efficient resource allocation.
5. Effective Supply Chain Management: Inventory control is critical for ensuring smooth and effective supply chain operations. By managing inventory levels with suppliers and distributors, organisations can decrease supply chain interruptions, reduce reliance on expedited shipment, and strengthen relationships with key stakeholders.
6. Reduced Risk of Theft and Loss: Implementing strong inventory control methods, such as regular audits, security standards, and inventory tracking systems, can help reduce the risk of theft, shrinkage, and inventory inaccuracy. This safeguards firms from financial losses and assures the accuracy of their inventory data.
Example of Inventory
Let’s take an example of inventory for a retail apparel store.
1. Raw Materials: This store’s raw materials would comprise fabrics, buttons, zippers, threads, and other products used in the creation of clothes.
2. Work-in-Progress (WIP): These are partially completed garments that are still being fitted, sewn, or customised. They are not yet available for purchase but are in the production stage.
3. Finished Goods: These are finished garment items that are ready to sell. This comprises shirts, trousers, dresses, jackets and so forth.
4. Maintenance, Repair, and Operations (MRO) Inventory: This could include products like sewing machines, needles, scissors, hangers, and other tools and equipment required to keep the store running and help the manufacturing process.
5. Cycle Inventory: Inventory that changes as new collections are launched or existing ones are phased out. For example, the store may stock up on winter goods in the autumn and lower its inventory of summer clothing throughout that time.
6. Seasonal Inventory: Inventory stored in preparation of seasonal demand swings. For example, the retailer may stock up on swimsuits and beachwear during the summer and coats and scarves during the winter.
These are just a few examples of the merchandise that a retail clothes store may handle. Each sort of inventory serves a distinct purpose and necessitates careful management to maximise stocking levels, save costs, and satisfy customer demands.
Inventory Turnover
Inventory turnover is an important part of managing inventory. This indicator, often called stock turnover, measures how much and how frequently a company’s inventory is sold, replaced, or used. This graph indicates how profitable a company is and whether any shortcomings need to be addressed. Consumer demand is important in determining whether inventory levels fluctuate quickly or not at all. Higher demand typically suggests that a company’s products and services will move quickly from the shelves to consumers’ hands, whereas low demand frequently results in a poor turnover rate.
A company’s inventory turnover is frequently stated as a ratio. The inventory ratio is calculated by dividing the cost of goods sold by the average inventory value. The inventory turnover ratio is computed using the following formula:

This data can be used by company management to make key decisions such as whether to continue manufacturing specific products and services or whether to handle difficulties that arise.
What is Inventory Analysis?
Inventory analysis is the act of examining and assessing a company’s inventory to acquire insight into its performance, efficiency, and effectiveness. It involves analysing many characteristics of inventory, such as composition, turnover, carrying costs, and replenishment patterns, in order to inform strategic decisions and improve inventory management procedures. Inventory analysis seeks to provide answers to crucial questions about inventory levels, trends, and drivers, allowing businesses to increase operational efficiency, cut costs, and improve customer service.
Benefits of Inventory Analysis
Inventory analysis provides significant advantages to organisations in several industries,
1. Optimised Inventory Levels: By analysing inventory data, firms may identify the best inventory levels to maintain. This helps to avoid overstocking, which takes up capital and warehouse space, as well as stockouts, which can result in lost sales and unsatisfied consumers.
2. Cost Reduction: Effective inventory analysis can save money by lowering holding costs for surplus inventory, lowering the risk of obsolescence, and expediting procurement processes.
3. Better Cash Flow Management: Maintaining ideal inventory levels prevents capital from being held up in surplus inventory, allowing organisations to use resources more efficiently and increase cash flow.
4. Enhanced Customer Service: Businesses can boost customer satisfaction and loyalty by keeping the proper things in stock when they’re needed. Inventory analysis assists in identifying high-demand items and ensuring their availability.
5. Better Demand Forecasting: Inventory analysis reveals demand patterns and trends, allowing for more accurate forecasting. This helps to correlate inventory levels with predicted demand, lowering the possibility of stockouts or surplus inventory.
6. Reduced danger of Stockouts: By analysing demand patterns and lead times, firms can proactively manage inventory levels, reducing the danger of stockouts and ensuring that products are accessible when customers require them.
7. Increased Profitability: Optimising inventory levels and lowering holding costs help to boost profitability. Furthermore, having the proper products in stock allows organisations to capitalise on sales opportunities and maximise revenue.
What is the Impact of Inventory on Businesses?
Inventory management has a huge impact on enterprises in several ways,
1. Financial Performance: Inventory makes up an important part of a company’s assets. Efficient inventory management has a direct impact on financial KPIs like cash flow, profitability, and ROI. Excess inventory ties up money and incurs holding costs, while stockouts can lead to lost sales and revenue.
2. Customer Service: Keeping the right quantity of inventory guarantees that products are available when customers require them. Stockouts can result in dissatisfied consumers, lost sales, and damage to reputation. Excess inventory, on the other hand, can clog resources and lead to poor customer service if unpopular items are overstocked.
3. Supply Chain Efficiency: Inventory management has an impact on the supply chain’s efficiency. Effective inventory management strategies can help to reduce lead times, and stockouts, and increase supplier coordination. This results in a more efficient and cost-effective supply chain operation.
4. Production Planning: Inventory levels affect production planning and scheduling. Accurate demand forecasting and inventory management guarantee that the necessary supplies are available for production, avoiding delays and disturbances in the manufacturing process.
5. Costs: Inventory expenses include holding costs (storage, insurance, obsolescence), ordering costs (procurement, transportation), and stockout costs (missed sales, rush orders). Poor inventory management can lead to high holding costs from surplus inventory or increased ordering costs from frequent minor orders.
6. Risk Management: Inventory management helps to reduce risks including stockouts, obsolescence, and demand fluctuations. Businesses can mitigate their exposure to supply chain interruptions and market variations by keeping adequate inventory levels and diversifying product ranges.
Frequently Asked Questions (FAQs)Â
1. What is inventory?
Answer:
Inventory includes both finished products for sale and raw materials needed in the production process. It is a valuable asset for enterprises and contains raw materials, work-in-progress, and finished products.
2. What are the different types of inventory?
Answer:
Raw materials (used in production), work-in-progress (partially completed goods), finished goods (available for sale), and maintenance, repair, and overhaul (MRO) inventory (necessary for operations).
3. Why is inventory management important?
Answer:
Inventory management helps control costs, optimise cash flow, improve customer happiness, enhance operational efficiency, ensure supply chain effectiveness, and reduce theft and loss.
4. How is inventory turnover calculated?
Answer:
Inventory turnover, an important indicator in inventory management, is derived by dividing the cost of goods sold (COGS) by the average value of inventory. It reveals how effectively a company’s inventory is sold, replaced, or utilised.
5. What are the benefits of inventory analysis?
Answer:
Inventory analysis can help optimise inventory levels, reduce costs, improve cash flow management, improve customer service, forecast demand, reduce stockouts, increase profitability, and manage supply chains efficiently.
Share your thoughts in the comments
Please Login to comment...